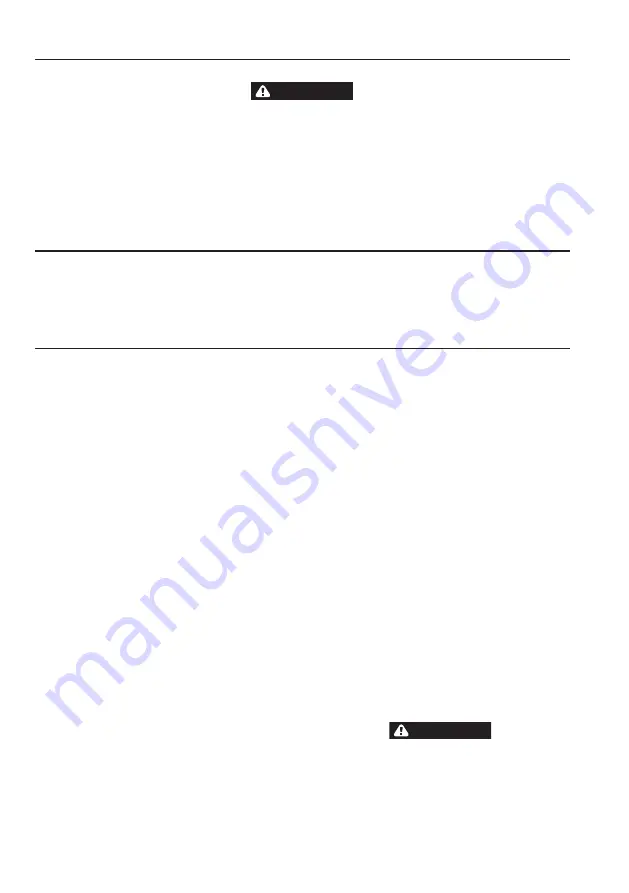
2
04581245_ed2
Product Safety Information
WARNING
Failure to observe the following warnings, and to avoid these potentially hazardous situations, could result in death or serious injury.
Read and understand this and all other supplied manuals before installing, operating, repairing, maintaining, changing accessories on, or
working near this product.
Always wear eye protection when operating or performing maintenance on this tool. The grade of protection required should be assessed
for each use and may include impact-resistant glasses with side shields, goggles, or a full face shield over those glasses.
Always turn off the air supply, bleed the air pressure and disconnect the air supply hose when not in use, before installing, removing or
adjusting any accessory on this tool, or before performing any maintenance on this tool or any accessory.
Do not use this tool if the actual free speed exceeds the rated rpm. Check the free speed of this tool before mounting any accessories, after
all tool repairs, before each job and after every 8 hours of use. Check speed with a calibrated tachometer, without the abrasive product
installed.
Note:
When reading the instructions, refer to exploded diagrams in parts Information Manuals when applicable (see under Related Documentation
for form numbers).
•
•
•
•
•
Whenever one of these Grinder, Die Grinder or Sander is
disassembled for overhaul or replacement of parts, lubricate the tool
as follows:
Always wipe the Vanes (28) with a light film of oil before inserting
them into the vane slots.
Inject 0.5 to 1.0 cm3 of Ingersoll Rand No. 10 Oil into the air Inlet
Assembly (1) after assembly.
1.
2.
Whenever a new Wick (53 or 72) is installed, soak the Wick in
approximately 1-1/2 cm³ of Ingersoll Rand No. 63 Oil. Do not
substitute any other oil.
Whenever the motor is disassembled, remove the old grease and
refill the cavity behind the Rear Rotor Bearing (25) with 3/4 cm³ of
Ingersoll Rand No. 68 Grease.
3.
4.
General Instructions
Do not disassemble the tool any further than necessary to replace
or repair damaged parts.
When grasping a tool or part in a vise, always use softsided vise
jaws to protect the surface of the part or tool and help prevent
distortion. This is particularly true of threaded members and
housings.
When grasping a tool in a vise, first place the tool housing in the
provided Clamp Tool (38), then grasp outer surface of Clamp Tool
in the vise to protect the housing from damage.
Do not remove any part which is a press fit in or on a subassembly
unless the removal of that part is necessary for repairs or
replacement.
Do not disassemble the tool unless you have a complete set of
new gaskets and O-Rings for replacement.
Do not press any needle bearing from a part unless you have a
new needle bearing on hand for installation. Needle bearings are
always damaged during the removal process.
Disassembly of all Angle Heads
For all Collet models
, grasp the tool, mounted in the Clamp Tool
(96), in soft-sided vise jaws with the Collet (77) upward. Using the
Collet Body Wrench (89) on the flats of the Collet Arbor (76) and
the Collet Nut Wrench (90) on the Collet Nut (78), unscrew the
Collet Nut and remove the Collet.
For All Wheel models
grasp the tool, mounted in the Clamp Tool
(96), in soft-sided vise jaws with the Flange Nut (85) upward.
For models ending in P945, P95 or P96
use a 4 mm hex wrench
to unscrew the Wheel Retaining Screw (87).
Use the Arbor Wrench (91) to hold the Arbor (76) and using the
Flange Nut Wrench (93 or 94), unscrew and remove the Flange
Nut. Remove the Wheel Retaining Screw Washer (88), the wheel,
Wheel Flange (84) and Flange spacer (86) from the Arbor.
For G2E models, using a 9/64” hex wrench, loosen the Wheel
Guard Adapter Screw (80) and remove the Guard Adapter
Assembly (79) from the Angle Housing Assembly (48).
For G2A and G2L models
, using a 5/32” hex wrench, loosen
Guard Adapter Screw (80) and remove the Guard Adapter
Assembly (79) from the Angle Housing Assembly (67).
6. Using a 1/8” hex wrench, unscrew and remove the three Guard
Mounting Screws (83), Guard Lock Washers (82) and Wheel Guard
(81).
1.
2.
3.
4.
5.
6.
1.
2.
3.
4.
5.
7. For all Sander models, grasp the tool, mounted in the Clamp Tool
(96), in soft-sided vise jaws with the Arbor (76) facing upward.
For All models - Continue Here
8.
For G2A and G2L models
, using a spanner wrench, unscrew and
remove the Arbor Bearing Cap (75). This is a left-hand thread.
Rotate the Cap Wrench clockwise to remove the Cap.
For G2E models
, using the Arbor Bearing Cap Wrench (92),
unscrew and remove the Arbor Bearing Cap (56). This is a left-
hand thread. Rotate the Cap Wrench clockwise to remove the
Cap.
9. For G2A and G2L models, using the Clamp Nut Wrench (95),
loosen the Clamp Nut (69) and pull the Angle Housing Assembly
(67) away from the Motor Housing (12) or Extension Housing (61).
This is a left-hand thread. Rotate the Nut Wrench clockwise to
loosen the Nut.
For G2E models, using the Clamp Nut Wrench (95), loosen the
Clamp Nut (50) and pull the Angle Housing Assembly (48) away
from the Extension Housing (43). This is a left-hand thread. Rotate
the Nut Wrench clockwise to loosen the Nut.
10. Grasp the Arbor and pull the assembled Arbor out of the Angle
Head. If the Wick (53 or 72) needs replacement, pull it out of the
Angle Housing.
11. If the Upper Arbor Bearing (52 or 71) needs replacement, support
the Angle Head on the table of an arbor press, bearing end down,
and press the Bearing out of the Angle Head.
12. Grasp the Arbor in soft sided vise jaws with the output end
downward. Using an adjustable wrench, unscrew and remove the
Bevel Gear Nut (54 or 73) and lift the Bevel Gear (66) off the Arbor.
13. If the Lower Arbor Bearing (55 or 74) must be replaced, use a
piece of tubing to support the Bearing on the table of an arbor
press and press the Arbor from the Bearing.
WARNING
When removing the Clamp Nut in the following procedure, take
all precautions necessary to prevent the Spacer from being
forcefully ejected in a manner or direction that is hazardous.
14. If the Clamp Nut (50 or 69) must be removed from the Angle
Housing, insert the blades of two screwdrivers, approximately
180 degrees apart, under the Clamp Spacer (49 or 68) and pry the
Spacer off the Housing.
Lubrication
Disassembly