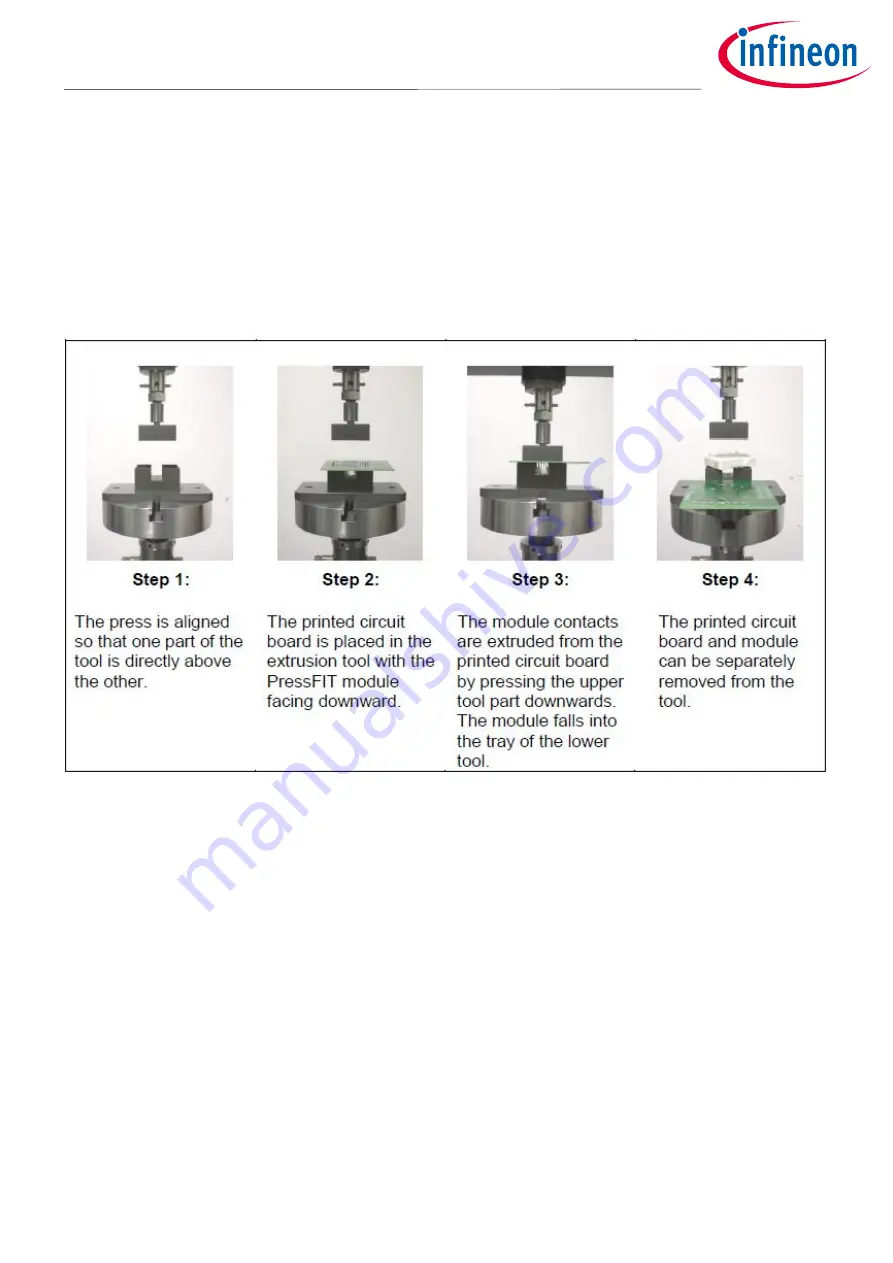
Application Note
10
<Revision 2.4>
<<2019-06-17>>
Assembly Instructions for the Easy-PressFIT Modules
4
The press-out process
This section deals with the necessary press-out forces and tools for the modules.
PressFIT modules are removed with the appropriate tools as shown in Figure 10 and Figure 11. The PCB is
placed with the PressFIT module on the device tray. Force is applied with the extrusion plate on the PressFIT
pins that protrude from the PCB. The press-out tools must be aligned parallel to each other so that the
individual components (such as the PCB and module) are not damaged. Once the PressFIT zone has been lifted
from the PCB, the module falls onto the tray in the lower part of the tool, and is separated from the board.
Figure 10
Extrusion of an Easy module
4.1
Press-out tools
As already mentioned above, the press-out tools consist of two parts. The upper part of the tool presses directly
downwards on the module pins. The lower part of the tool holds the module with the PCB, and serves as a base
for the pressing operation.
The disassembly tools must be aligned parallel to each other in order to obtain an equally distributed extrusion
process.
The dimensions of the press-out tool must be considered when designing the PCB so that the components
positioned around the module will not be damaged.