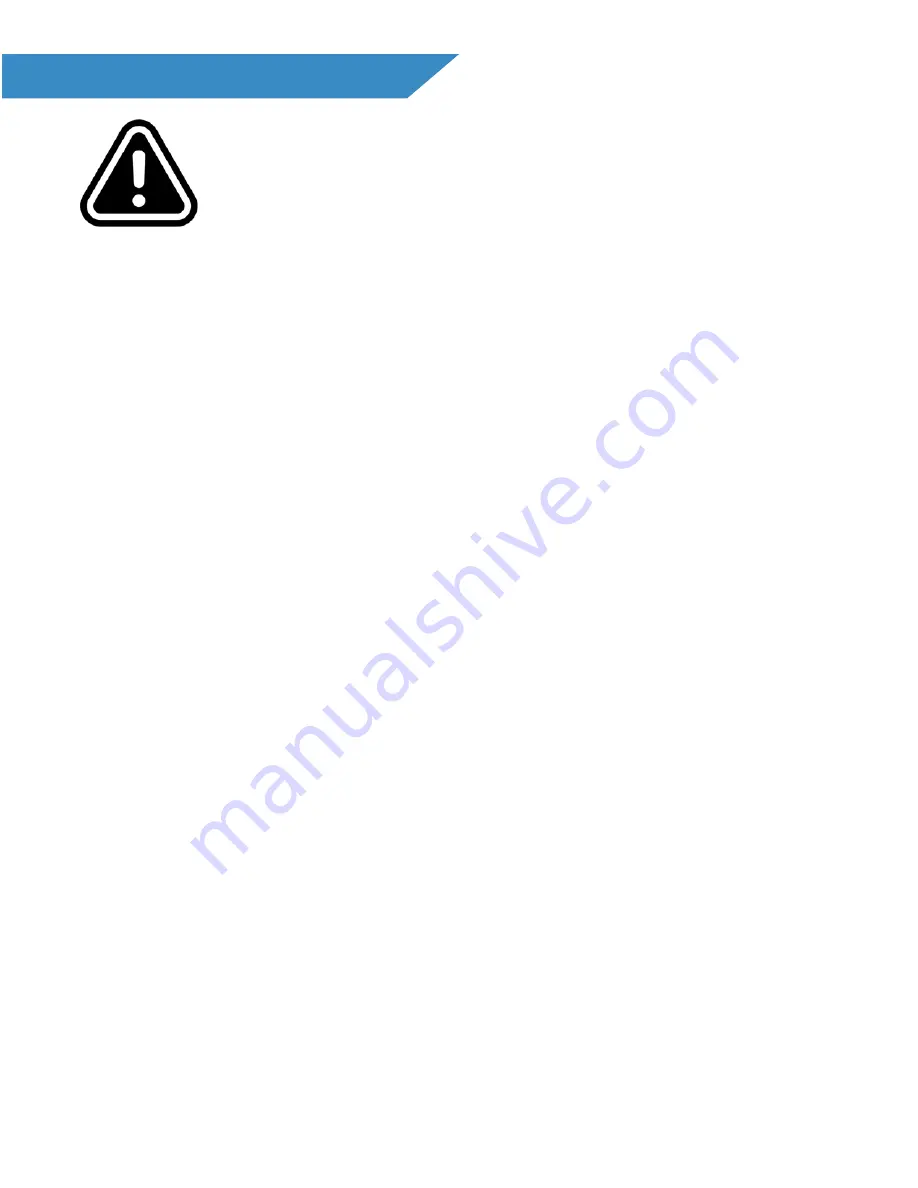
13
RECOMMENDED MAINTENANCE
WARNING
All aspects of the installation must conform to the requirements of
the NEC, including Article 430 (Motor circuits and Controllers), and all
local codes.
Wherever possible, each motor should be powered from a separate circuit of adequate capacity
to keep voltage drop to a minimum during starting and running. Increase wire size where motor is
located a distance from the power source. Wire size must be adequate to minimize voltage drop
during starting and running. Refer to Tables A and B for suggested wire sizes. Distances shown
are one-way between source and motor. Portable cords, if used, should be as short as possible
to minimize voltage drop. Long or inadequately sized cords, especially on hard starting loads, can
cause motor failure. All electrical connections in system must be secure to prevent voltage drop
and localized heating.
• Determine direction of rotation before connecting driven equipment to prevent damage.
• To prevent bearing damage, do not strike shafts with hammer or other tool.
•
If the motor has been damp or wet, then have motor serviced by a qualified motor repair
shop before operating.
Recommended Maintenance
Remove dirt accumulations in and around vent openings, by vacuuming.
Dirt accumulations
can cause motor overheating and a fire hazard.
Enclosed motors can be cleaned with an air
jet; wear eye protection.
Periodically inspect the installation. Check for dirt accumulations; unusual noises or vibration;
overheating; worn or loose couplings, sheaves and belts; high motor current; poor wiring or
overheated connections; loose mounting bolts or guards; and worn motor starter contacts.
Dayton ball-bearing motors without lubrication provision do not require periodic relubrication.
Where motor has provision for bearing lubrication, lubricate as follows:
1. After stopping motor and disconnection power, thoroughly wipe the housing around both of
the motor bearings, filler and drain plugs (on TEFC) ratings, remove fan cover for access
to plugs).
2.
Remove filler and drain plugs and install a 1/8” pipe thread lube fitting in filler hole.
3. Using a low pressure grease gun, pump new grease into motor until it appears at the drain
hole.
4.
Run motor for several minutes to discharge excess grease. Shut motor OFF, replace filler
and drain plugs, and reinstall fan cover.
See Table C for suggested regreasing intervals.