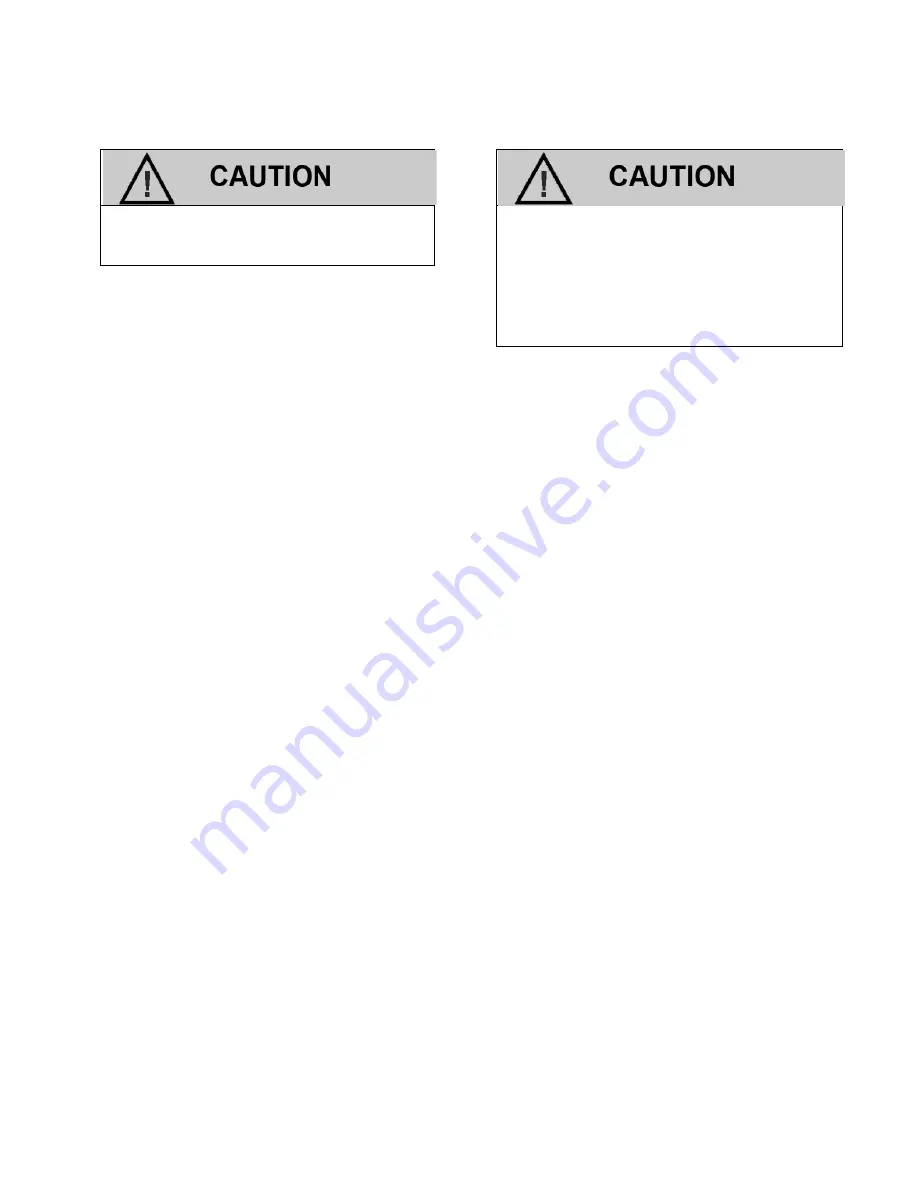
23
The EPR is an emission control device
and should only be serviced by qualified
technicians.
AIR FUEL MIXER
The air valve mixer is a completely self-contained
air-fuel metering device. The mixer is an air valve
design, utilizing a relatively constant pressure drop
to draw fuel into the mixer from cranking to full load.
The mixer is mounted in the air stream ahead of the
throttle control device.
When the engine begins to crank it draws in air with
the air valve covering the inlet, and negative pres-
sure begins to build. This negative pressure signal
is communicated to the top of the air valve chamber
through 4 vacuum ports in the air valve assembly.
A pressure/force imbalance begins to build across
the air valve diaphragm between the air valve va-
cuum chamber and the atmospheric pressure
below the diaphragm. The air valve vacuum spring
is calibrated to generate from 101.6 mm (4.0 inch-
es) of water column at start to as high as 355.60
mm (14.0 inches) of water column at full throttle.
The vacuum being created is referred to as Air
Valve Vacuum (AVV). As the air valve vacuum
reaches 101.6mm (4.0 inches) of water column, the
air valve begins to lift against the air valve spring.
The amount of AVV generated is a direct result of
the throttle position. At low engine speed the air
valve vacuum and the air valve position is low thus
creating a small venturi for the fuel to
flow. As the
engine speed increases the AVV increases and the
air valve is lifted higher thus creating a much larger
venturi. This air valve vacuum is communicated
from the mixer venturi to the EPR secondary
chamber via the low pressure fuel supply hose. As
the AVV increases in the secondary chamber the
secondary diaphragm is drawn further down forcing
the secondary valve lever to open wider.
The mixer is equipped with a low speed mixture
adjustment retained in a tamper proof housing.
The mixer has been preset at the factory and
should not require adjustment. In the event that the
idle adjustment should need to be adjusted refer to
the Fuel System Repair section of this manual.
The air/fuel mixer is an emission control
device. Components inside the mixer are
specifically calibrated to meet the engine’s
emissions requirements and should never
be disassembled or rebuilt. If the mixer
fails to function correctly, replace with an
OEM replacement part.
THROTTLE CONTROL DEVICE—DRIVE BY
WIRE
Drive By Wire Engine speed control is maintained
by the amount of pressure applied to the foot
pedal located in the engine compartment. In a
Drive By Wire (DBW) application, there is no di-
rect connection between the operator pedal and
the throttle shaft. Speed and load control are de-
termined by the ECM. Defaults programmed into
the ECM software and throttle position sensors
allow the ECM to maintain safe operating control
over the engine. In a drive by wire application the
Electronic Throttle Control device or throttle body
assembly is connected to the intake manifold of
the engine. The electronic throttle control device
utilizes an electric motor connected to the throttle
shaft. In addition, a Foot Pedal Position sensor
(FPP) is located in the operator’s compartment.
When the engine is running electrical signals are
sent from the foot pedal position sensor to the
engine ECM when the operator depresses or re-
lease the foot pedal. The ECM then sends an
electrical signal to the motor on the electronic
throttle control to increase or decrease the angle
of the throttle blade thus increasing or decreasing
the air/fuel charge to the engine. The electronic
throttle control device incorporates two internal
Throttle Position Sensors (TPS) which provide
output signals to the ECM as to the location of the
throttle shaft and blade. The TPS information is
used by the ECM to correct for speed and load
control as well as emission.
Summary of Contents for HHI
Page 4: ...4...
Page 5: ...5 General Information...
Page 10: ...10...
Page 11: ...11 Maintenance...
Page 19: ...19 LPG Fuel System...
Page 20: ...20 LPG FUEL SYSTEM OPERATION...
Page 27: ...27 LPG Closed Loop Schematic...
Page 28: ...28...
Page 29: ...29 LPG System Diagnosis...
Page 38: ...38...
Page 39: ...39 LPG Symptom Diagnostics...
Page 54: ...54...
Page 55: ...55 Gasoline Fuel System...
Page 56: ...56 GAS FUEL SYSTEM OPERATION...
Page 61: ...61 Gasoline Closed Loop Control Schematic...
Page 62: ...62...
Page 63: ...63 Gasoline System Diagnosis...
Page 70: ...70...
Page 71: ...71 Gasoline Symptom Diagnostics...
Page 84: ...84...
Page 85: ...85 Electrical Section...
Page 86: ...86...
Page 87: ...87 Diagnostic Scan Tool...
Page 89: ...89 Open the DST_Series III folder Open the Latest_GCP_Display folder...
Page 91: ...91 Click Next to continue Click Next to continue...
Page 92: ...92 Click the Finish box to complete the installation Click Yes to restart your computer...
Page 96: ...96 Double click on setup exe application file Click Next to continue...
Page 97: ...97 Select install ECOM drivers only Click Next and follow the on screen prompts...
Page 116: ...116 Message is displayed confirming the update was successful...
Page 120: ...120...
Page 121: ...121 Engine Wire Schematic...
Page 122: ...122 HHI 2007 2009 Emission Certified LPG Bi Fuel System 2 0L Engine...
Page 124: ...124...
Page 125: ...125 Engine Wire Harness Repair...
Page 129: ...129 Diagnostic Trouble Codes DTCs...
Page 133: ...133...
Page 137: ...137...
Page 145: ...145...
Page 151: ...151...
Page 155: ...155...
Page 161: ...161...
Page 169: ...169...
Page 173: ...173...
Page 177: ...177...
Page 187: ...187...
Page 191: ...191...
Page 195: ...195...
Page 199: ...199...
Page 203: ...203...
Page 211: ...211...
Page 221: ...221...
Page 225: ...225...
Page 229: ...229...
Page 233: ...233...
Page 237: ...237...
Page 241: ...241...
Page 245: ...245...
Page 249: ...249...
Page 253: ...253...
Page 257: ...257...
Page 261: ...261...
Page 265: ...265...
Page 269: ...269...
Page 273: ...273...
Page 277: ...277...
Page 281: ...281...
Page 285: ...285...
Page 291: ...291...
Page 295: ...295...
Page 307: ...307...
Page 313: ...313...
Page 317: ...317...
Page 323: ...323...
Page 329: ...329...
Page 333: ...333...
Page 337: ...337...
Page 341: ...341...
Page 345: ...345...
Page 349: ...349...
Page 353: ...353...
Page 357: ...357...
Page 361: ...361...
Page 377: ...377...
Page 399: ...399...
Page 403: ...403...
Page 407: ...407...
Page 411: ...411...
Page 415: ...415...
Page 419: ...419...
Page 423: ...423...
Page 429: ...429...
Page 433: ...433...
Page 437: ...437...
Page 441: ...441...
Page 445: ...445...
Page 449: ...449...
Page 453: ...453...
Page 457: ...457 Servicing the Fuel System...
Page 475: ...475 Definitions...
Page 480: ...480...
Page 481: ...481 TOOL KIT ACCESSORIES 1 2 3 4 5 6 7 8 9 10 11 12 13 14...
Page 483: ...483 Appendix...