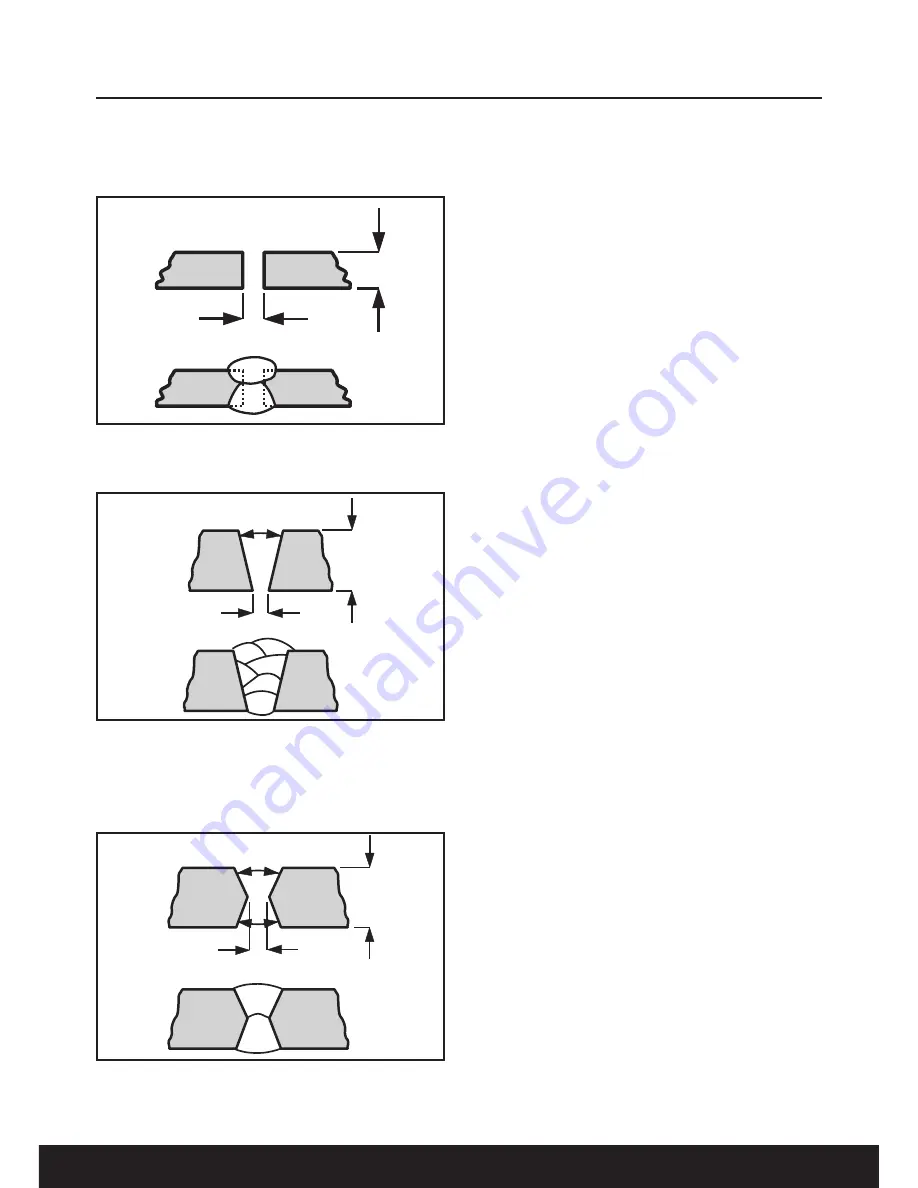
15
OPERATION
When welding material up to 7mm in thickness
place the pieces 2-3mm apart, run the welding
bead along the join. A second bead can go
along the underside for extra strength (Fig.10).
When welding material from 7mm to 30mm thick
prepare the material as shown in Fig.11 filling up
the space with several layers of weld.
When welding together material over 30mm in
thickness prepare the material as shown in
Fig.12 filling up the space with several layers of
weld, welding each side in turn with each
welding pass.
Disconnect the Welding Power Supply from the
mains supply before changing or removing
electrodes. Use pliers to remove used
electrodes from the electrode holder or to move
the welded pieces.
The Manual Metal Arc Process
When an arc is struck between the metal rod
(electrode) and the workpiece, both the rod and
workpiece surface melt to form a weld pool.
Simultaneous melting of the flux coating on the
rod will form gas and slag which protects the
weld pool from the surrounding atmosphere. The
slag will solidify and cool and must be chipped
off the weld bead once the weld run is complete
(or before the next weld pass is deposited).
The process allows only short lengths of weld to
be produced before a new electrode needs to
be inserted in the holder. Weld penetration is low
and the quality of the weld deposit is highly
dependent on the skill of the welder.
Types of Flux/Electrodes
Arc stability, depth of penetration, metal
deposition rate and positional capability are
greatly influenced by the chemical composition
of the flux coating on the electrode. Electrodes
can be divided into three main groups:
• Cellulosic
• Rutile
• Basic
Cellulosic electrodes
contain a high proportion
of cellulose in the coating and are characterised
by a deeply penetrating arc and a rapid burn-off
rate giving high welding speeds. Weld deposit
can be coarse and with fluid slag, deslagging
can be difficult. These electrodes are easy to
use in any position and are noted for their use in
the stovepipe (vertical down position) welding
technique.
Features:
•
• Deep penetration in all positions
• Suitability for vertical down welding
• Reasonably good mechanical properties
• High level of hydrogen generated - risk of
cracking in the heat affected zone
Fig 10
7mm
2-3mm
Fig 11
>30mm
60º
2-3mm
1
2
4
3
5
6
Fig 12
>30mm
60º
2-3mm
Summary of Contents for IM-MMA140
Page 2: ...Always Read Instruction Manual Retain for Future Reference IM MMA140 140A MMA WELDER...
Page 22: ...21 NOTES...
Page 23: ...22 NOTES...
Page 24: ...23 NOTES...