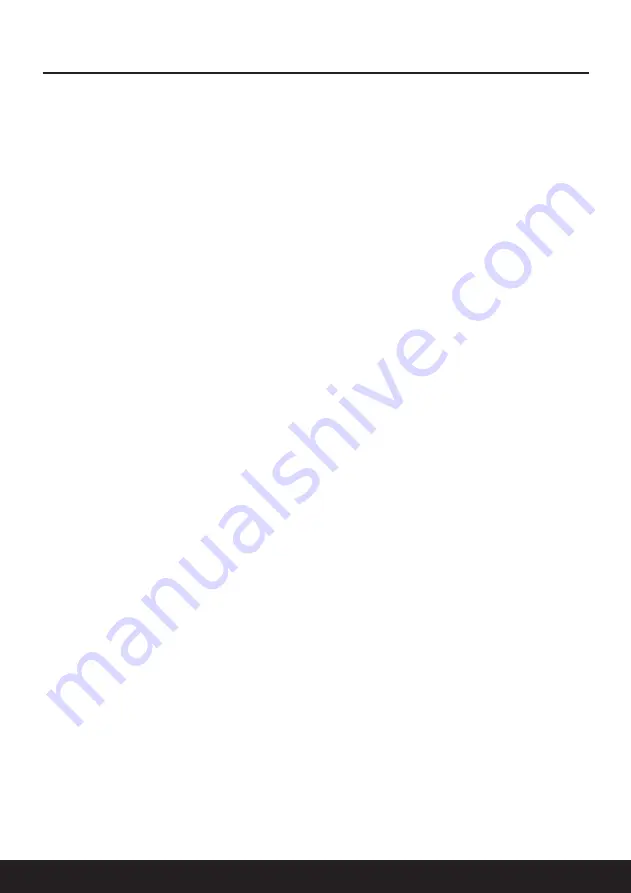
26
MMA OPERATION
Efficiencies as high as 130 to 140% can be
achieved for rutile and basic electrodes without
marked deterioration of the arcing
characteristics but the arc tends to be less
forceful which reduces bead penetration.
Care of Electrodes
The quality of weld relies upon consistent
performance of the electrode. The flux coating
should not be chipped, cracked or, more
importantly, allowed to become damp.
Drying of Electrodes
Drying is usually carried out following the
manufacturer's recommendations and
requirements will be determined by the type of
electrode.
Storage
Electrodes should always be kept in a dry and
well-ventilated store. It is good practice to stack
packets of electrodes on wooden pallets or
racks well clear of the floor. Also, all unused
electrodes which are to be returned should be
stored so they are not exposed to damp
conditions to regain moisture. Good storage
conditions are 100°C above external air
temperature. As the storage conditions are to
prevent moisture from condensing on the
electrodes, the electrode stores should be dry
rather that warm. Under these conditions and in
original packaging, electrode storage time is
practically unlimited. It should be noted that
electrodes are now available in hermetically
sealed packs which obviate the need for drying.
However, if necessary, any unused electrodes
must be redried according to manufacturer's
instructions.
IMPORTANT – Thermostatic Protection
(Duty Cycle)
This product has a rated duty cycle of 15%. The
percentage represents the welding time in a 10
minute period for example 15% means that the
welding time is 1.5 minutes with a rest time of
8.5 minutes in a ten minute period although the
actual duty cycle will depend on the amperage
used. If the Welding Power Supply is used for
longer than the duty cycle or if you are welding
using large welding rods you may experience a
temporary current shut off. This is to protect the
transformer inside the Welding Power Supply
from overheating.
The thicker the material being welded, the
greater the current required, therefore, the hotter
the machine will become and the quicker it will
cut out. When the windings reach performance
temperature the cut out switch will operate and
the digital display will show “E-3”. After a few
minutes the cut out switch will reset and the
welder will be ready for use.