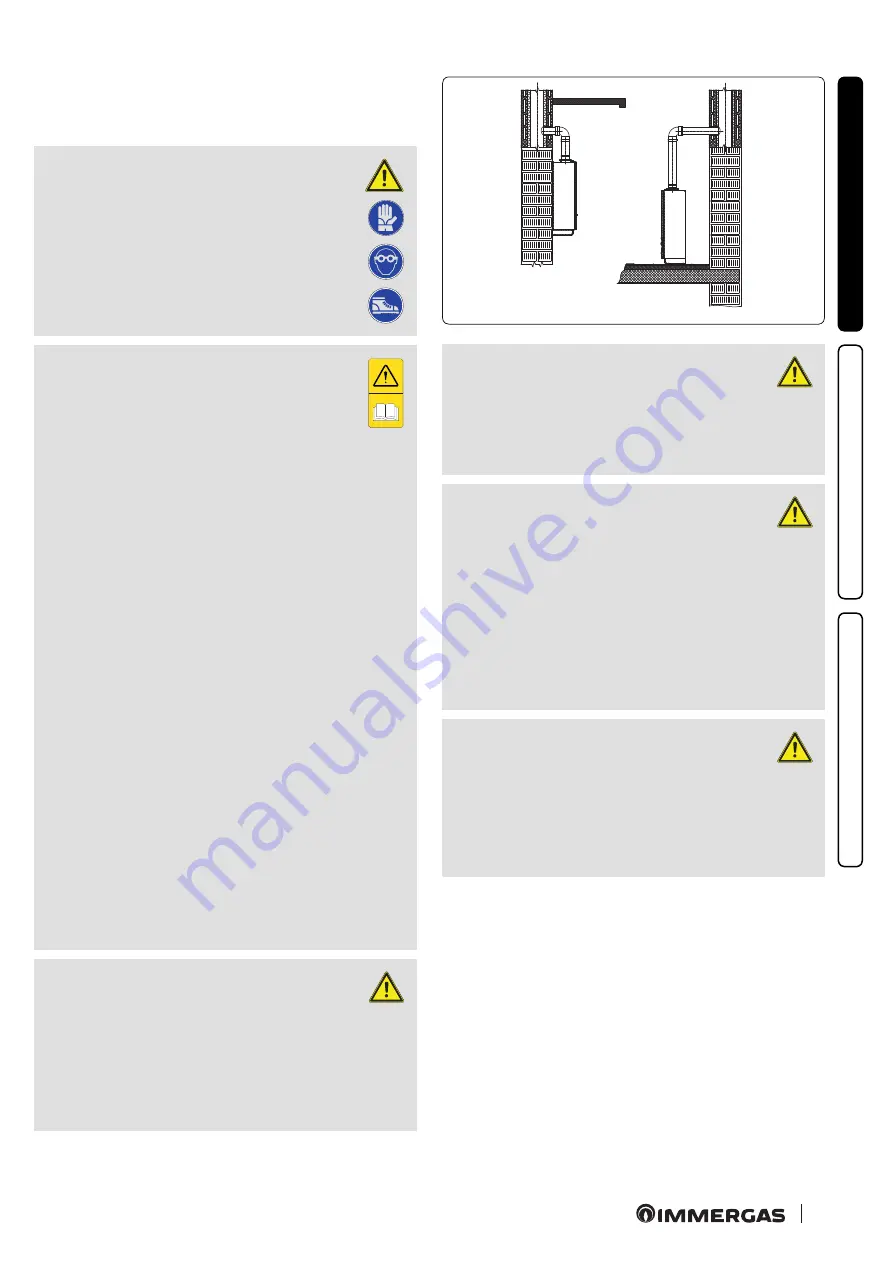
1
SI
NO
INS
TALLER
US
ER
MAINTEN
AN
CE TECHNI
CI
AN
5
1
BOILER INSTALLATION.
1.1 INSTALLATION RECOMMENDATIONS.
ATTENTION:
operators who install and service the
appliance must wear the personal
protective equipment required by ap-
plicable law.
The Victrix Tera boiler has been designed for wall
mounted installation only; for central heating and
production of domestic hot water for domestic use
and similar purposes.
The place of installation of the appliance and relative
Immergas accessories must have suitable features
(technical and structural), such as to allow for (always in safe,
efficient and comfortable conditions):
- installation (according to the provisions of technical legisla-
tion and technical regulations);
- maintenance operations (including scheduled, periodic,
routine and special maintenance);
- removal (outdoors in the place for loading and transporting
the appliances and components) as well as their eventual
replacement with appliances and/or equivalent components.
The wall surface must be smooth, without any protrusions or
recesses enabling access to the rear part. They are not designed
to be installed on plinths or floors (Fig. 1).
By varying the type of installation the classification of the boiler
also varies, precisely:
- Type B
23
or B
53
boiler if installed using the relevant terminal
for air intake directly from the room in which the boiler has
been installed.
- Type C boiler if installed using concentric pipes or other types
of pipes envisioned for the sealed chamber boiler for intake
of air and expulsion of flue gas.
Only professionally qualified companies are authorised to
install Immergas gas appliances.
Installation must be carried out according to regulation stand-
ards, current legislation and in compliance with local technical
regulations and the required technical procedures.
ATTENTION:
It is not permitted to install boilers that
are removed and decommissioned from
other systems. The manufacturer declines all
liability for damage caused by boilers removed
from other systems or for any non-conformi-
ties of such equipment.
ATTENTION:
check the environmental operating
conditions of all parts relevant to in-
stallation, referring to the values shown in the
technical data table in this booklet.
ATTENTION:
Installation of the Victrix Tera boiler
when powered by LPG must comply
with the rules regarding gases with a greater
density than air (remember, as an example,
that it is prohibited to install plants powered
with the above-mentioned gas in rooms where
the floor is at a lower quota than the country
level).
ATTENTION:
if installing a kit or servicing the ap-
pliance, always empty the system’s
domestic hot water circuit first so as not to
compromise the appliance’s electrical safety
(Par. 2.10).
YES
NO