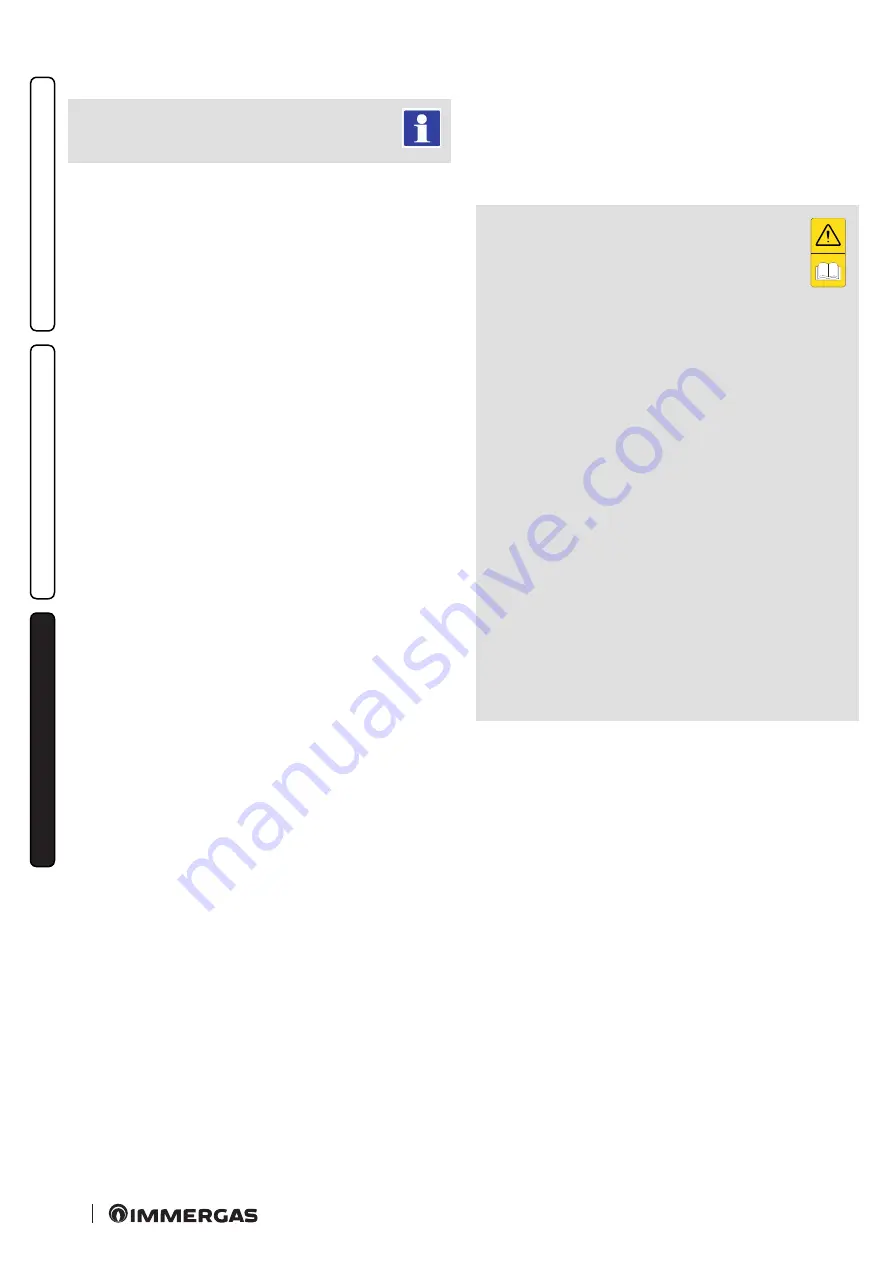
INS
TALLER
US
ER
MAINTEN
AN
CE TECHNI
CI
AN
44
3.6 POSSIBLE PROBLEMS AND THEIR CAUSES.
Maintenance interventions must be carried out by
an authorised company (e.g. Authorised After-Sales
Technical Assistance Service).
- Smell of gas.
Caused by leakage from gas circuit pipelines. Check
tightness of gas intake circuit.
- Repeated ignition blocks.
It can be caused by no gas, check the
presence of pressure in the network and that the gas adduction
cock is open. Incorrect adjustment of the gas valve, check the
correct calibration of the gas valve.
- Irregular combustion or noisiness.
It may be caused by: a
dirty burner, incorrect combustion parameters, intake-exhaust
terminal not correctly installed. Clean the above components
and ensure correct installation of the terminal, check correct
setting of the gas valve (Off-Set setting) and correct percentage
of CO
2
in flue gas.
-
Non-optimal ignition of first ignitions of the burner.
Even
if the burner is perfectly calibrated, first ignition of the burner
(after calibration) can be sub-optimal; the system automatically
regulates ignition until it finds optimal ignition of the said burner.
- Frequent interventions of the safety thermostat function
(delegated to flow probe and system return probe).
It can de-
pend on the lack of water in the boiler, little water circulation in
the system or blocked pump. Check on the pressure gauge that
the system pressure is within established limits. Check that the
radiator valves are not closed and also the functionality of the
pump.
- Drain trap clogged.
This may be caused by dirt or combustion
products deposited inside. Check, by means of the condensate
drain cap, that there are no residues of material blocking the flow
of condensate.
- Heat exchanger blocked.
This may be caused by the drain trap
being blocked. Check, by means of the condensate drain cap, that
there are no residues of material blocking the flow of condensate.
- Noise due to air in the system.
Check opening of the special air
vent valve cap (Part. 20 Fig. 36). Make sure the system pressure
and expansion tank factory-set pressure values are within the
set limits; The factory-set pressure values of the expansion vessel
must be 1.0 bar, the value of system pressure must be between
1 and 1.2 bar.
- Noise due to air inside the condensation module. Use the manual
air vent valve (Part. 20 Fig. 36) to eliminate any air present in the
condensation module. When the operation has been performed,
close the manual air vent valve.
- Poor production of D.H.W. If a drop in performance is detected
during supply of D.H.W., it is possible that the condensation
module or D.H.W. heat exchanger is clogged. In this case, contact
Authorised After-Sales Assistance Service that has procedures
to clean the module or D.H.W. heat exchanger.
3.7 CONVERTING THE BOILER TO OTHER
TYPES OF GAS.
If the device must be adapted to a different type of gas
than what is specified on the plate, you must request
an Immergas kit with frequency and mode compliant
with what is specified in the technical legislation in
force.
The gas conversion operation must be carried out by an
authorised company (e.g. Authorised After-Sales Technical
Assistance Service).
To convert to another type of gas the following operations are
required:
- disconnect power to the appliance;
- replace the nozzle positioned above the gas valve (Part.9Fig.
36) taking care to disconnect the appliance during this oper-
ation;
- re-power the appliance;
- calibrate fan speed (Par. 3.8);
- adjust the correct air/gas ratio (Par. 3.9);
- seal the gas flow rate regulation devices (if settings are mod-
ified);
- after completing the conversion, apply the sticker, contained
in the conversion kit, on the data plate in the area relating to
the type of gas.
These adjustments must be made with reference to the type of
gas used, following that given in the table (Par. 4.2).