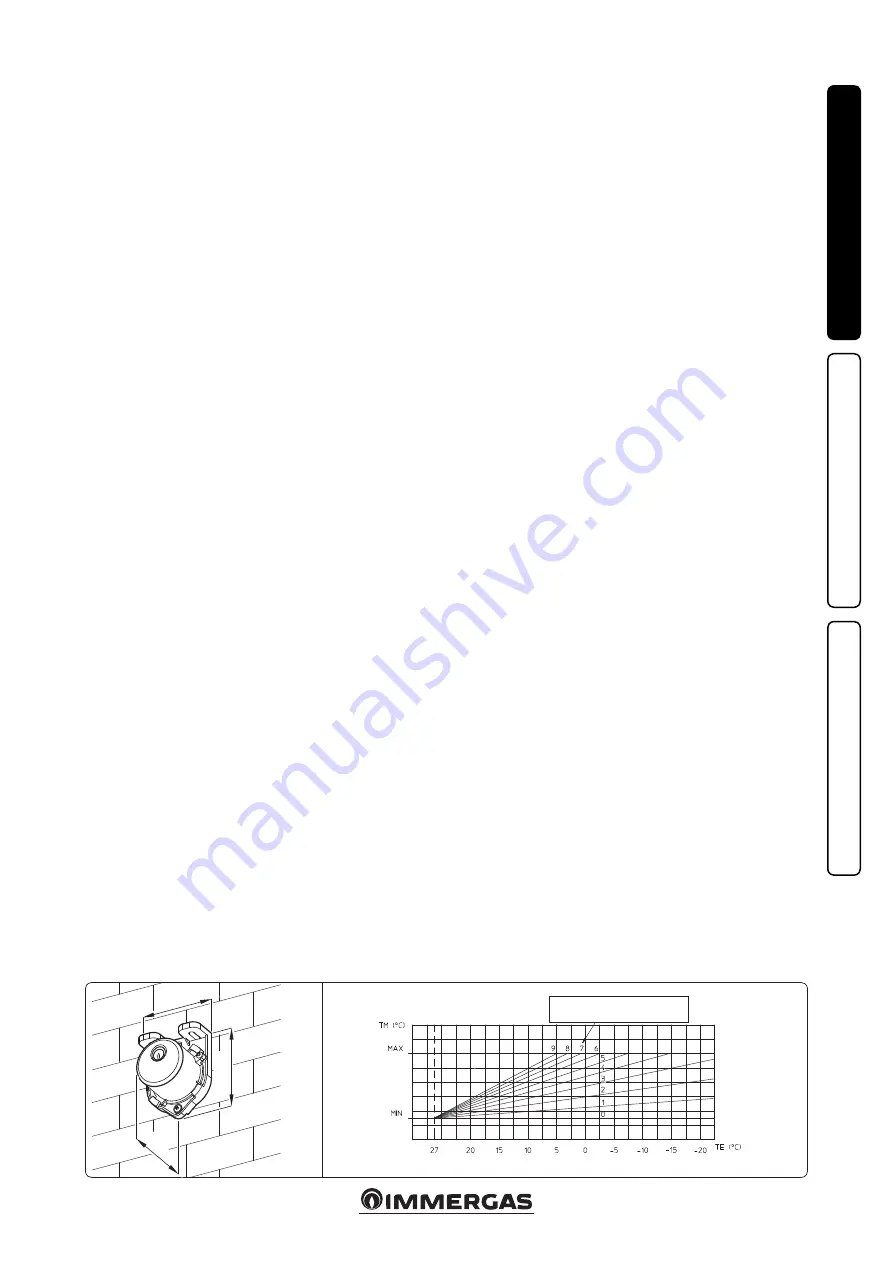
7
45
31
58
INS
TALLER
US
ER
MAINTEN
AN
CE TECHNI
CI
AN
1.5 EXTERNAL PROBE (OPTIONAL).
The boiler is designed for the application of the
Room Thermostat (Fig. 1-5) which is available as
an optional kit. Refer to the relative instruction
sheet for positioning of the external probe.
The probe can be connected directly to the boiler
electrical system and allows the max. system
flow temperature to be automatically decreased
when the external temperature increases, in
order to adjust the heat supplied to the system
according to the change in external temperature.
The external probe always acts when connected
independently from the presence or type of room
thermostat used. The correlation between system
flow temperature and outdoor temperature
is determined by the position of the selector
switch on the boiler control panel according to
the curves shown in the diagram (Fig. 1-6). The
electric connection of the external probe must be
made on clamps 38 and 39 on the boiler P.C.B.
(Fig. 3-2).
1.6 VENTILATION OF THE ROOMS.
In the room in which the boiler is installed it is
necessary that at least as much air flows as that
requested for by normal combustion of the gas
and ventilation of the room. Natural air flow must
take place directly through:
- permanent openings in the walls of the room
to be ventilated that lead towards the outside;
- ventilation pipes, individual or branched type.
The air used for ventilation must be withdrawn
directly from outside, in an area away from
sources of pollution. Natural air flow is also
allowed indirectly by air intake from adjoining
rooms. For further information relative to
ventilation of the rooms follow that indicated
by the standards in force and the following
modifications and integrations.
Evacuation of foul air.
In the rooms where
the gas appliances are installed it may also be
necessary, as well as the intake of combustion
agent air, to evacuate foul air, with consequent
intake of a further equal amount of clean air. This
must be realised respecting the provisions of the
technical regulations in force.
1.7 FLUE DUCTS.
The gas appliances with attachment for the flue
gas discharge pipe must have direct connection
to chimneys or safely efficient flues.
The combustion products can be discharged
directly outside only if these are missing, as long
as the standard regulations for the flue terminal
are respected as well as the existing laws.
Connection to chimneys or flues.
The
connection of the appliances to a chimney or
flue takes place by means of flue ducts.
In the event of fittings with pre-existing flues, these
must be perfectly clean because the detachment
of any waste from the walls during functioning,
could block the passage of flue gases, thus causing
extremely dangerous situations for the user.
The flue ducts must be connected to the chimney
or flue in the same room in which the appliance
is installed or, at most, in the adjoining room and
must comply with the requirements indicated by
the regulation.
1.8 FLUES/CHIMNEYS.
For the appliances with natural draught
individual chimneys and branched flues can
be used.
Individual chimneys.
The individual flues must
be dimensioned with respect to the standard
in force.
Branched flues.
In buildings with lots of floors,
branched flues can be used for the natural
draught evacuation of combustion products. New
flues must be designed following the calculation
method and provisions of the regulation.
Chimney caps.
The chimney cap is a device
positioned on the top of an individual chimney
or branched collective flue. This device promotes
the dispersion of combustion products, even in
adverse weather conditions, and prevents the
deposit of foreign bodies.
It must satisfy the requisites set forth in the
relative regulation.
The outlet quota, corresponding to the top of the
chimney/flue, independently of any caps, must
be out of the “backflow area”, in order to prevent
the formation of counter-pressures that impede
the free discharge of the combustion products
into the atmosphere. It is therefore necessary
to use the minimum heights indicated in the
figures stated in the regulation, depending on
the slope of the roof.
Direct exhaust outside.
The natural draught
appliances, envisioned to be connected to a
chimney or a flue, can discharge the combustion
products directly to the outside, through a
pipe passing through the perimeter walls of
the building. In this case discharge takes place
through an exhaust flue, which is connected to
a draught terminal at the outside.
Exhaust flue.
The exhaust flue must be in
compliance with the same requisites listed for
the flue ducts, with further provisions stated in
the regulation in force.
Positioning the draught terminals.
The draught
terminals must:
- be installed on external perimeter walls of the
building;
- be positioned according to the minimum
distances specified in current technical
standards.
Fume exhaust of forced draught appliances
in closed open-top environments.
In spaces
closed on all sides with open tops (ventilation
pits, courtyards etc.), direct flue gas exhaust
is allowed for natural or forced draught gas
appliances with a heating power range from 4 to
35 kW, provided the conditions as per the current
technical standards are respected.
Important:
it is prohibited to put the fumes
exhaust control device out of order voluntarily.
Every piece of this device must be replaced using
original spare parts if they have deteriorated. In
the case of repeated interventions of the fumes
exhaust control device, check the fumes exhaust
flue and the ventilation of the room in which the
boiler is located.
Fig. 1-5
Fig. 1-6
Position of the central heating
temperature user adjustment
Summary of Contents for 3.018921
Page 1: ...NIKE MINI 28 KW SPECIAL Instruction and warning booklet 1 040845ENG...
Page 21: ......
Page 22: ......
Page 23: ......