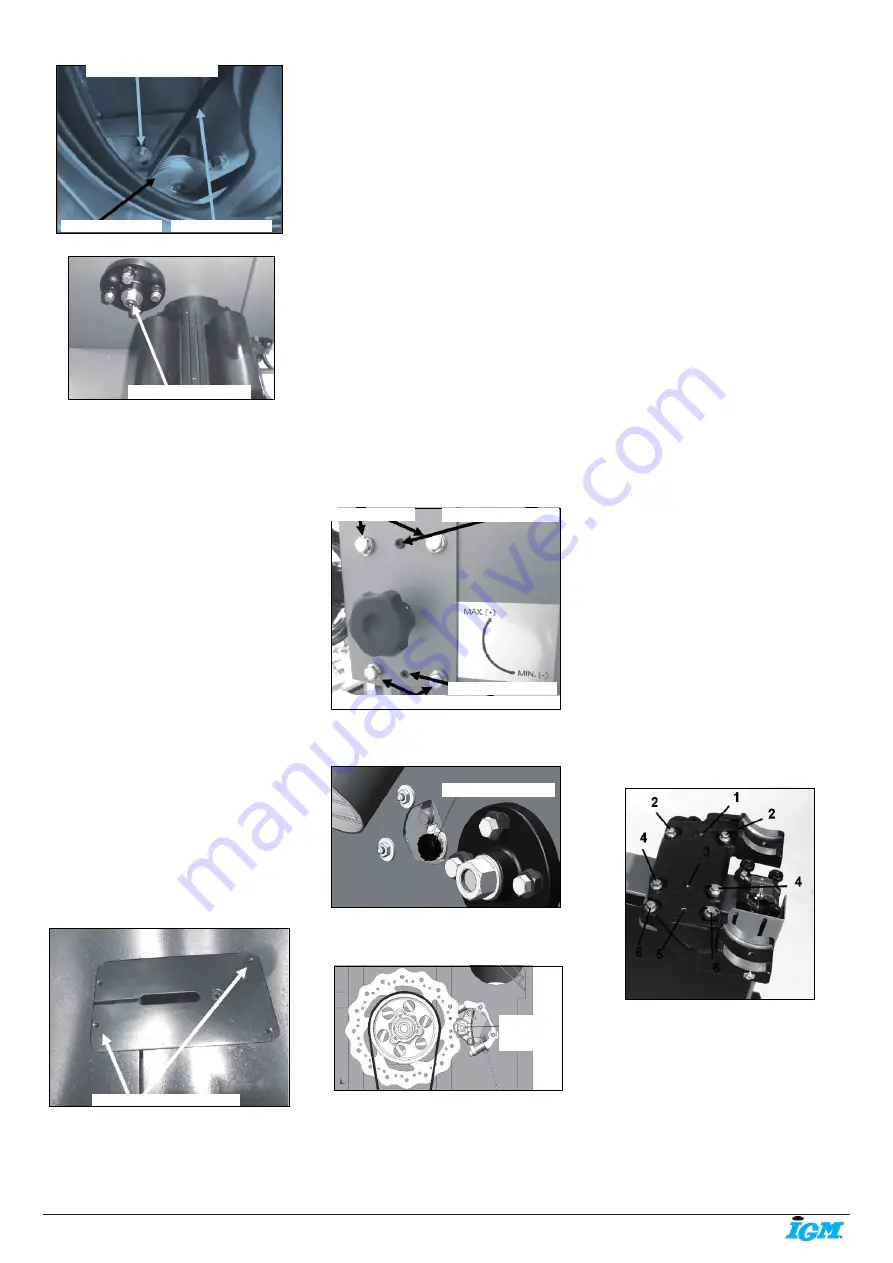
-16-
www.igmtools.com
Replacing the drive belt
Pic. 72
Pic. 73
To replace the belts you will have to remove the
lower flywheel.
1. Loosen the motor clamp bolts and move the
motor so that the tension is completely
removed from the drive belt. Remove the blade.
Loosen the two hex nuts that hold the brake
to the bandsaw frame and slide it out of the way
of the disc.
2. Remove the flywheel shaft nut that clamps
the wheel axle (back of the bandsaw).
3. Pull the lower flywheel off the bandsaw. You
may have to use a gear puller to remove the
lower wheel.
4. Replace the drive belt.
5. Refit the lower wheel and re-clamp with the
flywheel shaft nut.
6. Tension the drive belt and tighten the motor
clamping bolts.
Note.
It is better to replace the drive belt early
than to have a breakdown during an
important job.
Note.
Take great care not to damage the
bearings when taking the flywheel off and
reassembling.
Table Insert.
The table insert (throat plate) is made of
aluminium and is designed to reduce damage
to the blade should they come in contact. If
the blade slot becomes too wide or the insert
becomes damaged by the blade, it should be
replaced. The replacement insert will have to
be fitted to the table hole. The insert is provided
with four jacking screws that can be adjusted so
that the insert is level with the top of the table.
Pic. 74
Bearings
All bearings are sealed for life and do not
require any maintenance. If a bearing becomes
faulty, replace it.
Rust
The bandsaw is made from steel and cast
iron. All non-painted surfaces will rust if not
protected. It is recommended that the table be
protected by coating with wax if the machine is
not in constant use. All moving non-painted
surfaces (guides, rack and pinion, etc.) should
be lubricated/protected with a Teflon-based
lubricant.
Blade guide rack and pinion
The top guide when moved vertically tracks the
blade and comes factory-set. Adjustment
is provided should that mechanism become
misaligned. This is a tricky operation and
should only be attempted if an extreme error
has occurred.
Back guide forward/back adjustment.
1.
Four clamping bolts and two Allen jacking
screws are provided.
2.
Slightly loosen the two clamping bolts A and
tighten the bottom Allen screw B will bring the
guide forward.
3.
Slightly loosen the two clamping bolts C and
tighten the top Allen screw D will bring the guide
back.
4.
Make only very small adjustments. Tighten
the clamping bolts prior to checking the guide
vertical movement.
Note
: The machine comes factory-set, and no
adjustment should be required.
Pic. 75
Adjusting the break
Back break adjustor
Pic. 76
Front break adjustor
Flywheel not shown for clarity
Pic. 77
The back break adjustor moves clockwise to
remove slack in the break pad.
The front break adjustor is rotated clockwise
with an allen key to remove slack in the break
pad.
Adjusting the table square to the bandsaw
blade
Note.
The machine is set in the factory and no
adjustment should be required but during
transportation movement may occur.
To access the adjustment screws, you will
have to tilt the table up to 45 degrees and lock
in position.
The adjustment is made with the jacking
screws 1 & 3 only. Jack screw 5 and clamp
screws 6 are used for support only.
1.
Set the table to 90 degrees and place an
engineer‘s square on the table and check if the
blade is leaning forward or backward. The
blade will be parallel and it is easier to check
the blade at the back.
2.
Tilt the table up to 45 degrees and lock in
position.
3.
Loosen jack screw 5 and clamp screws 6
[only used for support and not adjustment].
4.
If the top of the blade is leaning forward [gap
at the top of the engineers square], the back
of the table will have to be adjusted up. Slightly
loosen set screw 3 and the two hex head
screws 2, when loosening the clamp hex head
screws ensure that they are loosened the
same amount. Then fully tighten set screw 1
and the two hex head screws 4. Only make very
small adjustments as a small movement of the
jack screws makes a large adjustment of the
table. Move the table back to 90 degrees, clamp
in position and check if the blade is square to
the table with the engineers square. Repeat
adjustment if required.
5.
If the top of the blade is leaning back [gap at
the bottom of the engineers square], the front
of the table will have to be adjusted up. Slightly
loosen set screw 3 and the two hex head
screws 2. Then fully tighten set screw 1 and the
two hex head screws 4. Only make very
small adjustments as a small movement of the
jack screws makes a large adjustment of the
table. Move the table back to 90 degrees, clamp
in position and check if the blade is square to
the table with the engineers square. Repeat
adjustment if required
6.
Once adjustments have been completed,
lightly tighten set screw 5 and the two clamp
hex head screws 6. Do not over tighten as this
will bend the steel support plate and may affect
the adjustment that you have
made.
Pic. 78
Adjusting the table square to blade.
1. Check that the stop bolt is in contact with the
tilt-blanking disc.
2. Place an engineers square on the table top
and bring up to the side of the blade.
3. Check if the blade is square to the table.
4. If adjustment is required loosen the lock nut
on the tilt-stop bolt and adjust in the required
direction.
Note.
Only adjust the tilt-stop bolt in very small
steps.
5. Tighten the lock nut and recheck
Clamp bolts C
Allen jacking screw D
Jack bolt B
Clamping bolts A
Rear Adjusting Knob
Front
Adjusting
Screw
Drive belt
Motor drive pulley
Drive belt adjusting bolt
Flywheel shaft nut
Throat plate jacking screws