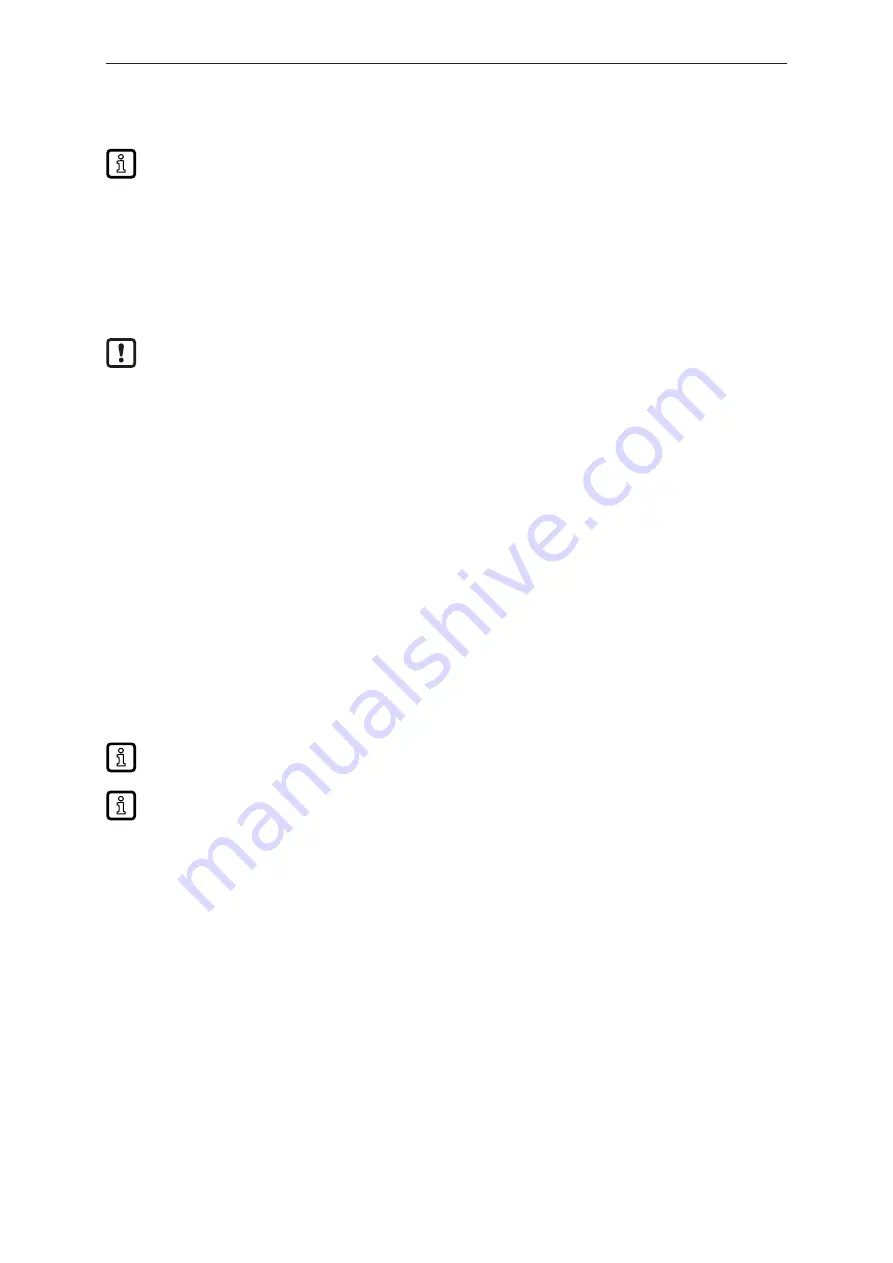
PM11
Electronic pressure sensor
14
7 Parameter setting
The unit can be configured via the IO-Link function.
u
Use the unit description file (IODD) for this purpose:
u
Prepare IO-Link hardware and software for parameter setting.
u
Connect the unit with e.g. an IO-Link interface or programmed memory plug.
u
Set the parameters.
u
Put the unit into operation.
u
The parameters can be set before installation or during operation.
Changing parameters during operation can influence the function of the plant.
u
Make sure that there will be no malfunctions or dangerous operation in your plant.
7.1 Parameter setting via PC
For parameter setting, an IO-Link parameter setting software, an IO-Link master and a suitable device
description file (IODD) are required.
.
u
Prepare computer, parameter setting software and IO-Link master.
u
Connect the device with the IO-Link master.
u
Follow the menu of the IO-Link parameter setting software.
u
Set the parameters.
u
Put the device into operation.
7.2 Parameter setting via the memory plug
A parameter set can be written to the device / can be recorded by the device via a memory plug (ifm
storage module):
.
In order to allow for data to be written from the memory plug to the sensor, the sensor must
have the factory setting.
If the sensor has been configured, the memory plug records the parameter set which can then
be transferred to other sensors of the same type.
u
Load a suitable parameter set (e.g. from a PC or from a sensor of the same type) to the memory
plug.
u
Connect the memory plug between sensor and socket.
w
Sensor with factory setting:
When voltage is supplied, the parameter set is transferred from the memory plug to the sensor.
w
Sensor with changed settings:
When voltage is supplied, the memory plug records the sensor's parameter set.
u
Remove the memory plug.
u
Put the unit into operation.
More information on the memory plug:
Ò
Documentation