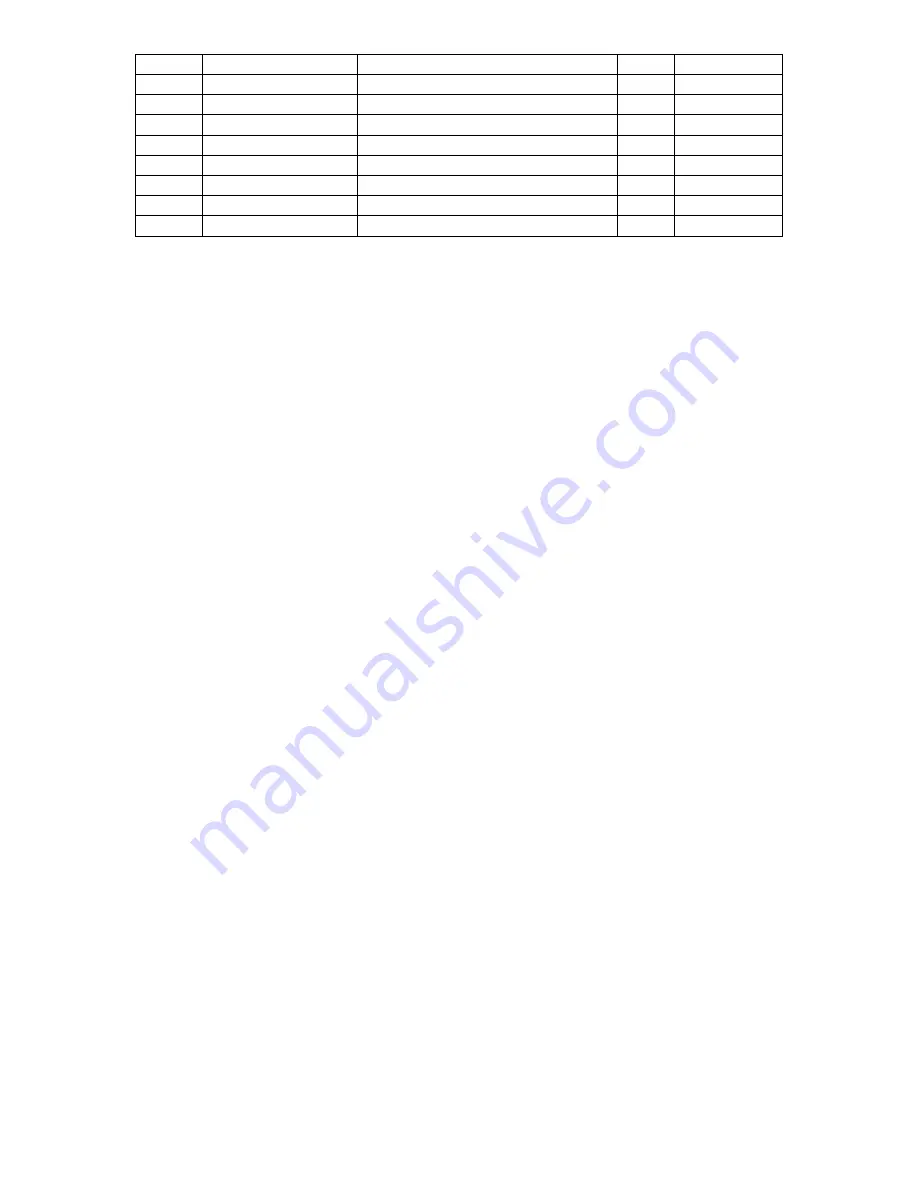
31
TP12KC-DX
Jun 2017
ITEM
CODE
DESCRIPTION
QTY
NOTE
88
5302-00004-000
Flat Washer, D10
10
φ
10
89
SJ13-00054-000
Hose Cover, Upper MS Column
1
90
SJ13-00055-000
Hose Cover, Low MS Column
1
91
SJ13-00056-000
Hose Cover, Offside Column
1
92
5105-08012-000
Screw, M8x12
4
M8*12
93
EG01-00013-000
Rubber Door Guard
2
94
SJ13-00057-000
Hose Cover, Column Extensions
2
95
SJ01-00017-000
Protection Ring
2