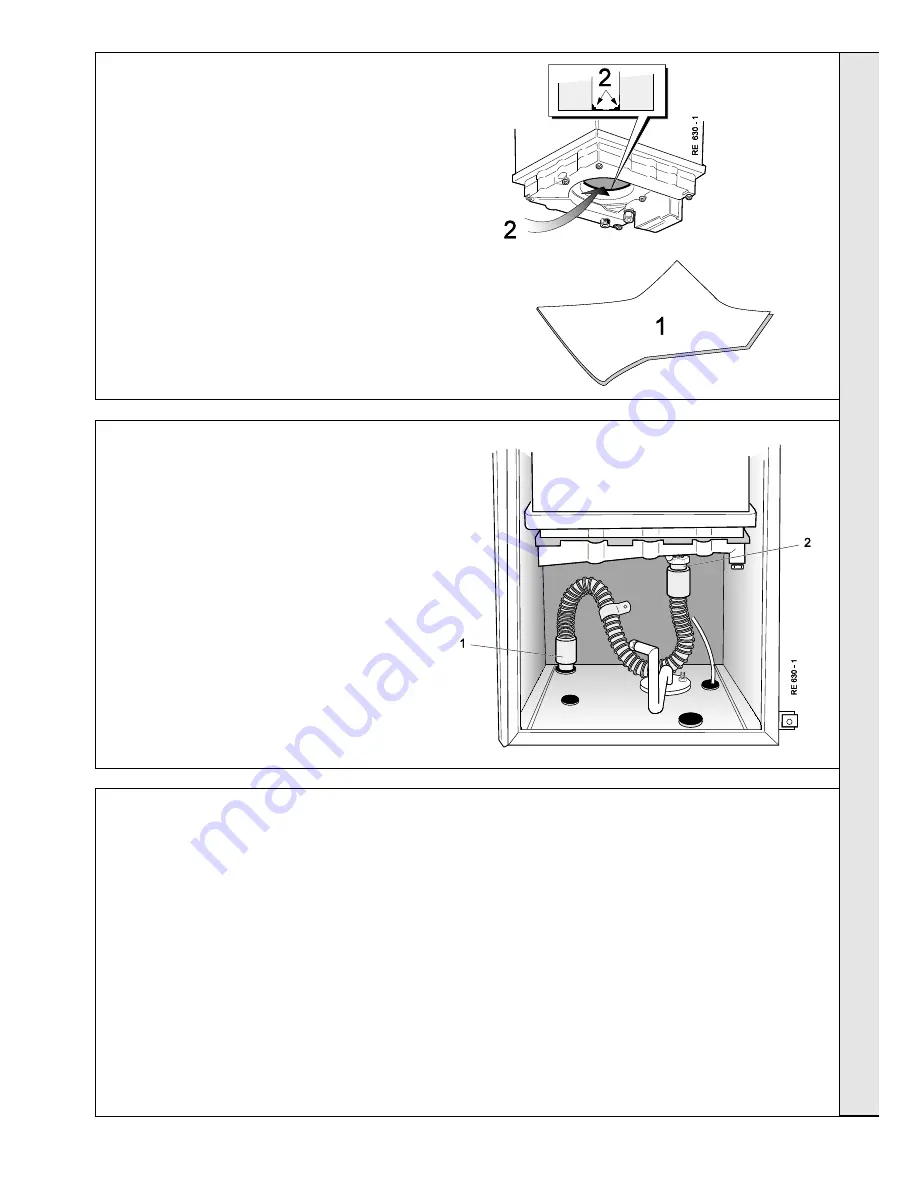
41
Systemiser SE -
Installation
SERVICING
SER
VICING
58 CLEANING THE HEAT EXCHANGER
Re-assemble the boiler in the following order:
1.
Refit the condensate trap.
2.
Refit the burner, renewing any damaged or deteriorating
sealing gaskets.
3.
Reconnect the ignition and detection leads.
4.
Reconnect the fan electrical lead.
5.
Refit the fan, engaging it in the bayonet fixing. Ensure
that the 'O' ring seal is in place.
IMPORTANT
This MUST be done with the heat exchanger and
deposit in a DRY condition.
Prior to cleaning, run the boiler until a flow temperature
of 80
o
C is reached - refer to Frame 52, step 1
(Servicing schedule).
1.
Place a plastic sheet or similar beneath the boiler
and remove all visible loose deposits from the heat
exchanger fins, using a suitable brush.
2.
Take care to clean debris from the ledge inside the
combustion chamber.
1.
Pull off the condensate trap from the bottom
panel and carefully empty the contained water
into a receptacle.
2.
Pull off the trap from the bottom of the boiler.
3.
Withdraw the trap from the boiler.
4.
Thoroughly flush the trap by running high
pressure water through it.
6.
Refit the fan inlet venturi complete with sensing pipe.
7.
Refit the boiler sealing panel.
IMPORTANT.
Ensure that the boiler sealing panel is correctly fitted
and that a good seal is made.
8.
Refit the boiler casing.
9.
Turn on the gas supply at the gas service cock.
10.
Reconnect the electrical supply.
59 CLEANING THE CONDENSATE TRAP
60 RE-ASSEMBLY
Summary of Contents for Systemiser SE
Page 1: ......
Page 31: ...31 Systemiser SE Installation INSTALLATION INSTALLATION 42 PICTORIAL WIRING DIAGRAM...
Page 57: ...57 Systemiser SE Installation SHORTS LIST OF PARTS 86 SHORT PARTS LIST...
Page 60: ...60 Systemiser SE Installation 89 BOILER CASING ASSEMBLY SHORT LIST OF PARTS...
Page 61: ...61 Systemiser SE Installation...