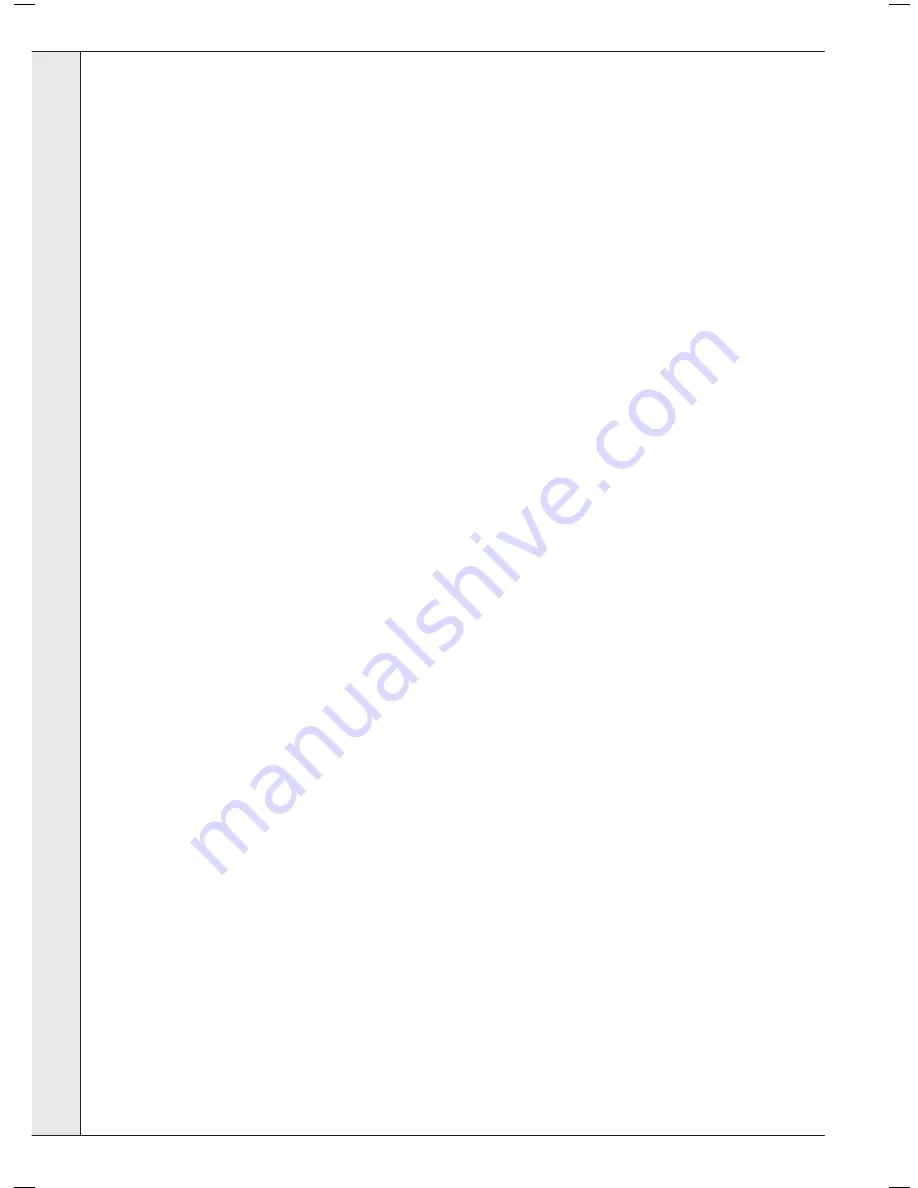
16
Super Plus -
Installation and Servicing
Repeat for the other 3 studs.
Take the round blanking plate supplied and fit it into the central
bottom module opening in the casing. Secure it using the 4 M10
nuts and washers provided. Fit the blank flanges and gaskets to
the return water header connection. Blank off the water flow header
connection using the 2 in. BSP cap and close taper point supplied.
A 1" BSP cap is supplied to seal the gas header connection.
300/3 Alternative Boiler (Refer Fig.11)
The procedure to blank off the bottom RH module and the central
bottom module must be carried out as detailed under 500/5 boiler
and 400/4 Alternative boiler above. In addition the top right hand
module opening in the casing must be blanked off.
First remove one of the four M10 slotted studs and backnut from
the top right hand opening in the casing, and replace by one of the
longer studs in the blanking kit. Screw the M8 threaded portion of
the new stud through the cast support ring and through the hole
in the interior support strut. Fit the M8 nut and washer from the
back and tighten.
Repeat for the other 3 studs.
Take the round blanking plate supplied and fit it into the top right
hand module opening in the casing. Secure it at the bottom and
right hand sides using the M10 nuts and washers.
Secure the water flow header support bracket to the round blanking
plate using the top and LHS fixings. Blank off the water flow header
using the blank flange and the 2 gaskets supplied (flow water
header, gasket, blank flange, gasket & support bracket)
A 1" BSP cap is supplied to seal the gas header connection.
Blank off the return water header connection using the 2" BSP cap
and close the taper nipple supplied.
CONNECTING BOILERS TO THE FLUE
SYSTEM
Details of the flue design are shown in Figs. 6 and 7.
The boiler socket and flue pipe sizes are given in Table 1.
WATER CONNECTIONS AND PRESSURES
Refer to 'Installation Requirements'
All service pipework, linking the flow and return headers, should
be adequately supported, taking care that no strain is imposed
upon them.
Allowance must be made for any additional service pipework
expansion.
Provision for draining the boiler should be made at the lowest
point in the system.
A safety valve MUST be fitted.
The valve should be set at 0.7 bar (10 lb/ in
2
) ABOVE the available
static head of water over the boiler or design operating pressure
of the system, whichever applies, with a maximum value of 6.7
bar (95 lb/in
2
)
If isolating valves are fitted in the flow and return pipes to the
boiler, they must NOT isolate the boiler from the open vent, safety
valve or cold feed.
The maximum safety valve setting is 0.7 bar (10 lb/in
2
) above the
maximum design operating head, or pressure of the boiler - 6.0
bar (85 lb/in
2
)
ELECTRICAL CONNECTIONS
Refer to Fig.14
The mains input to the boiler must be wired into the 3 way terminal
block on the lower of the 3 wiring centres (PCB No. 11) on the left
hand side of the boiler.
Terminals S1, S2 & S3 allow safety devices to be wired directly into
the boiler. Thus the water flow switch should be wired between S1
& S2 and other devices wired between S2 & S3 (e.g., a fan diluted
flue switch). Terminal S2 is voltage free.
If all safety devices are wired in series with the isolation mains
supply then terminals S1 & S3 must be linked.
The length of the conductors between the cord anchorage and the
terminals must be such that the current carrying conductors become
taut before the earthing conductor, if the cable or cord slips out of
the cord anchorage.
The live and neutral conductors for each module are disconnected
and insulated within the wiring centre for safety purposes on leaving
the works. These wires must be connected to the appropriate L
and N terminal strip connections on printed circuit boards 10 and
11 within the wiring centre (see Fig.8 to 12 and Fig. 14) for each
module.
If a 300/3 Alternative or 400/4 Alternative boiler is fitted, the unused
module wiring must be left disconnected to ensure the module
multipin plug remains electrically safe.
COMMISSIONING AND TESTING
The
Super Plus
boiler must be commissioned and tested by a
competent person. In the case of installations covered by the
Current Gas Safety (Installation and Use) Regulations or Rules
in Force, the engineer shall be Gas Safe registered.
Upon request, Ideal Boilers, will provide a quote for commissioning
or recommissioning after servicing.
FILLING THE BOILER WITH WATER
Fill the system by admitting water at the lowest point This will ensure
air is forced from the tubes of the heat exchangers.
WATER CIRCULATION
Switch on the pump motor and check that water is circulating and
the pump is vented.
Check the operation of the water flow switch. It should switch off
the electrical supply to the modules when the water flow falls to
NO MORE THAN one third of the design water flow-rate (given
in Table 1).
HEADER GAS TIGHTNESS & PURGING THE
GAS LINE
Turn the module gas service cock that is furthest from the gas inlet.
Connect the manometer to the tapping point at the end of the gas
header (PTP No.1, Fig.19)
Slacken the nut on the 1" union, connecting the module to the gas
header, and purge the gas header by turning the mains inlet gas
tap on until gas is smelled. Retighten the union connection (see
also IM/2). Turn off the module gas service cock and ensure that
all other module gas service cocks are in the OFF position.
Take note of the manometer reading and turn off the mains inlet gas
cock. A subsequent fall in pressure, after allowing for temperature
stabilizing, indicates a leak between the mains inlet gas and
individual module gas service which MUST be made good. The
mains inlet gas can then be turned on again.
In all gas soundness checks, wait for 1 minute for temperature
stabilisation and then check for pressure drop during the next 2
minutes.
INSTALLATION
INST
ALLA
TION