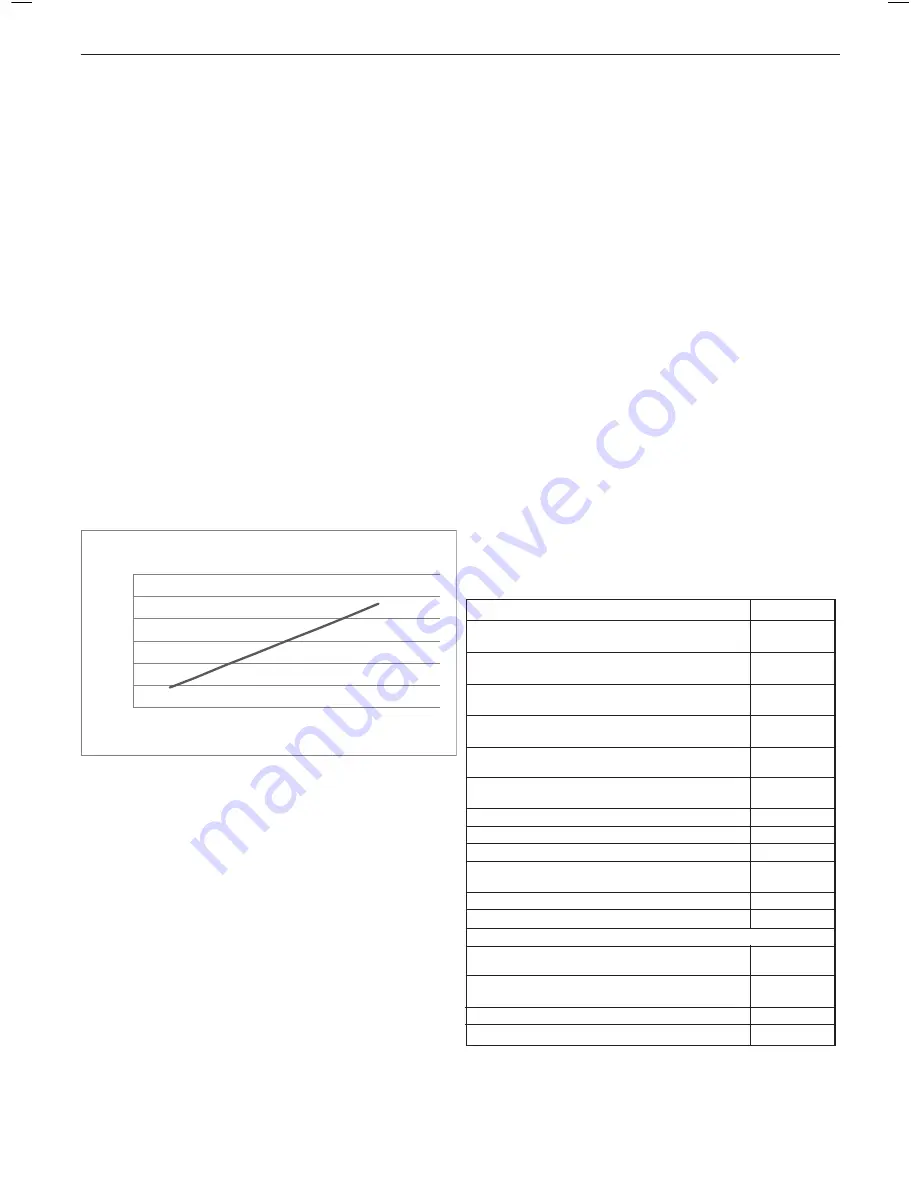
8
Ideal Logic Heat -
Installation and Servicing
general
gas sUppLy
The local gas supplier should be consulted, at the installation
planning stage, in order to establish the availability of an adequate
supply of gas. An existing service pipe must NOT be used without
prior consultation with the local gas supplier.
The boiler MUST be installed on a gas supply with a governed
meter only.
A gas meter can only be connected by the local gas supplier or
by a Gas Safe Registered Engineer. In IE by a Registered Gas
Installer (RGII).
An existing meter should be checked, preferably by the gas
supplier, to ensure that the meter is adequate to deal with the rate
of gas supply required.
It is the responsibility of the Gas Installer to size the gas
Installer to size the gas installation pipework in accordance with
BS6891:2005. Whilst the principle of the 1:1 gas valve ensures
the Logic range is able to deliver it’s full output at inlet pressures
as low as 14mb, other gas appliances in the property may not be
as tolerant. When operating pressures are found to be below the
minimum meter outlet of 19mb these should be checked to ensure
this is adequate for correct and safe operation.
Allowing for the acceptable pressure loss of 1mb across the
installation pipework, it can be assumed that a minimum permitted
operating pressure of 18mb will be delivered to the inlet of
the appliance. (Reference BS 6400-1 Clause 6.2 Pressure
Absorption).
The external gas cock could further reduce the operating pressure
when measured at its test point. The pressure drop is relative to
the heat input to the boiler (kW), refer to graph below.
0
0.5
1
1.5
2
2.5
3
0
10
20
30
40
50
Pre
ss
ure
d
ro
p
(mb
ar
)
Heat Input to Boiler (kW)
Gas Cock Pressure Drop
IMpORTaNT.
Installation pipes must be fitted in accordance with BS.6891. In IE
refer to IS.813:2002.
The complete installation MUST be tested for gas tightness and
purged as described in the above code.
FLUE INsTaLLaTION
Pluming will occur at the terminal so terminal positions where this
could cause a nuisance should be avoided.
The flue must be installed in accordance with the
recommendations of BS. 5440-1: 2008.
In IE refer to I.S. 813:2002.
The following notes are intended for general guidance:
1.
The boiler MUST be installed so that the terminal is exposed
to external air.
2.
It is important that the position of the terminal allows the free
passage of air across it at all times.
3.
Minimum acceptable spacing from the terminal to obstructions
and ventilation openings are specified in
Table 3.
* Only one reduction down to 25mm is allowable per installation
otherwise BS5440-1 2008 dimensions must be followed.
Flue Terminal positions
Min. spacing*
1.
Directly below, above or alongside an opening
window, air vent or other ventilation opening.
300mm (12”)
2.
Below guttering, drain pipes or soil pipes.
25mm ( 1”)*
BS5440-1 2008
75mm (3”)
3.
Below eaves.
25mm (1”)*
BS5440-1 2008
200mm (8”)
4.
Below balconies or a car port roof.
25mm (1”)*
BS5440-1 2008
200mm (8”)
5.
From vertical drain pipes or soil pipes.
25mm (1”)*
BS5440-1 2008
150mm (6”)
6.
From an internal or external corner or to a
25mm (1”)*
boundary along side the terminal.
BS5440-1 2008 300mm (12”)
7.
Above adjacent ground, roof or balcony level.
300mm (12”)
8.
From a surface or a boundary facing the terminal.
600mm (24”)
9.
From a terminal facing a terminal.
1,200mm (48”)
10.
From an opening in a car port
(e.g. door or window) into dwelling.
1,200mm (48”)
11.
Vertically from a terminal on the same wall.
1,500mm (60”)
12.
Horizontally from a terminal on the wall.
300mm (12”)
Vertical Terminals
13.
Above the roof pitch with roof slope of all angles.
300mm (12”)
Above flat roof.
300mm (12”)
14.
From a single wall face.
300mm (12”)
From corner walls.
300mm (12”)
15.
Below velux window
2000mm (79”)
16.
Above or side of velux window
600mm (24”)
Table 3 - Balanced Flue Terminal position
4.
Where the lowest part of the terminal is fitted less than 2m
(6’6”) above a balcony, above ground or above a flat roof
to which people have access then the terminal MUST be
protected by a purpose designed guard.
Terminal guards are available from boiler suppliers. (Ask for
TFC flue guard model no. K6 - round, plastic coated). In case
of difficulty contact:
TFC Group Ltd.
Tel. + 44 (0) 01732 351 680
Tower House, Vale Rise
Fax. + 44 (0) 01732 354 445
Tonbridge. Kent TN9 1TB
www.tfc-group.co.uk
Ensure that the guard is fitted centrally.
5.
The flue assembly shall be so placed or shielded as to prevent
ignition or damage to any part of any building.
6.
The air inlet/products outlet duct and the terminal of the boiler
MUST NOT be closer than 25mm (1”) to combustible material.
Detailed recommendations on the protection of combustible
material are given in BS. 5440-1:2008.
IMpORTaNT
. It is essential to ensure, in practice, that products
of combustion discharging from the terminal cannot re-enter the
building or buildings through any openings into the building such
as ventilators, windows, doors, or other sources of natural air
infiltration, such as forced ventilation openings etc.
If products of combustion re-entry is identified or suspected this
should be immediately investigated and corrected following the
guidance provided in the current Gas Industry Unsafe Situation
Procedure.
Summary of Contents for Logic HEAT 12
Page 2: ...2 Ideal Logic Heat Installation and Servicing...
Page 51: ...51 SERVICING Ideal Logic Heat Installation and Servicing...
Page 58: ...58 SPARE parts Ideal Logic Heat Installation and Servicing...
Page 64: ...64 Notes Ideal Logic Heat Installation and Servicing...
Page 65: ...65 Notes Ideal Logic Heat Installation and Servicing...