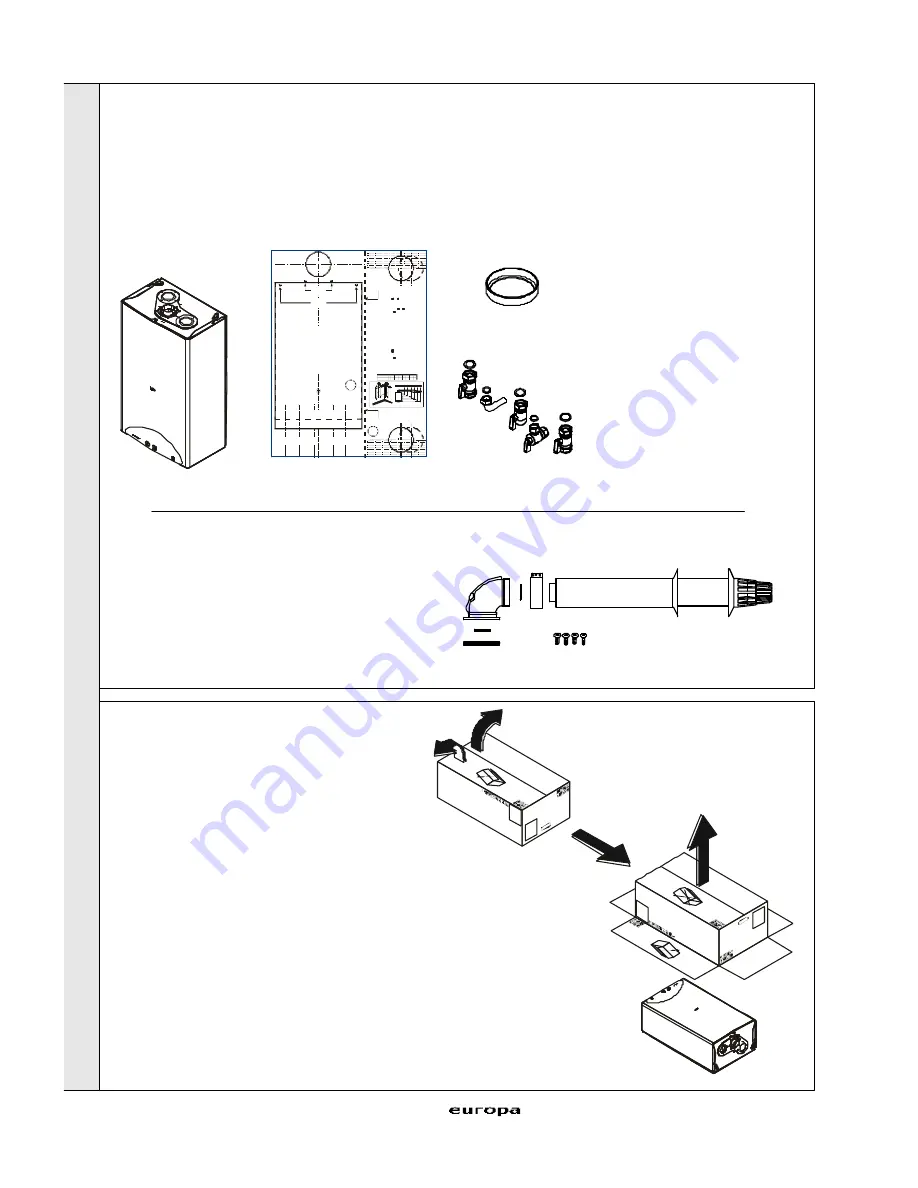
12
INSTALLATION
combination boiler -
Installation and Servicing
9
UNPACKING
The boiler is supplied fully assembled in one Pack A, together
with a standard flue assembly for lengths up to 720 mm, rear
or side flue outlet, in Pack B.
Optional extras, if ordered, are available in separate boxes.
Unpack and check the contents.
Hardware Pack
?
Wall plugs with hook screw - 2 off.
?
Wall mounting template - 1 off.
?
CH Flow and Return isolating valve
- 2 off.
?
CW inlet isolating valve - 1 off.
?
HW outlet pipe - 1 off.
?
Gas isolating valve - 1 off.
?
3/4” gaskets - 3 off.
?
1/2” gaskets - 2 off.
?
Smoke outlet diaphragm - 1 off.
?
Instructions for mounting flue
restrictor
Pack A Contents
Also contained in Pack A:
?
Hardware Pack (listed below).
?
These Installation & Servicing Instructions.
?
The User's Instructions.
?
Benchmark book.
1.
Ensure the boiler is positioned correctly as marked
on the carton (reverse position).
2.
Remove the band and staples.
3.
Fold back the top flaps and the plastic bag to get
access to the boiler.
4.
Reverse the carton on the side where top flap has
been folded to 270° (The other top flaps can be
folded to 180° only).
5.
Lift the card board box.
6.
Dispose of packaging.
7.
Remove the plastic bag and collect instructions and
read them thoroughly before installing the boiler.
1 0 PACKAGING REMOVAL
Pack B Contents
1- Flue turret.
2- Flue terminal.
3- External rubber ring.
4- Internal rubber ring.
5- Gasket for turret flange.
6- Gasket for inner pipe - 2 off.
7- Self tapping screws - 4 off.
8- Sleeve with clamp for ext. pipe - 1 off.
Instructions.
1
2
3
Complete boiler
Piping kit
Wall mounting template
Flue restrictor
1
2
3
4
5
6
6 8
7
L
L
MIN. INSTALLED TOP CLEARANCE 165 mm
TOP OF BOILER
PLEASE NOTE THE FOLLOWING POINTS
THIS TEMPLATE ( A AND B ) SHOWS THE POSITION FOR THE
FIXING HOLES AND FLUE HOLE CENTRE FOR STANDARD
INSTALLATION AND FOR USING THE OPTIONAL STAND-OFF KIT.
1. SEPARATE TEMPLATES A AND B ALONG THE DOTTED LINE.
2. TAPE TEMPLATE A INTO SELECTED POSITION.
3. ENSURE SQUARENESS BY HANGING A PLUMBLINE. IF FITTING
A SIDE EXIT FLUE THEN REFER TO SIDE EXIT INSTRUCTIONS
BELOW.
4. MARK ON THE WALL THE FOLLOWING:
a. THE TWO MOUNTING PLATE SCREW POSITIONS .
b.
THE POSITION OF THE FLUE DUCT HOLE. MARKING ON THE
CENTRE OF THE HOLE AS WELL AS THE CIRCUMFERENCE.
5. REMOVE TEMPLATE FROM THE WALL.
1. FOLLOW POINTS 1 - 3 ABOVE:
2. EXTEND FLUE CENTRE LINE HORIZONTALLY ACROSS SIDE
WALL THEN HORIZONTALLY FORWARD, AS SHOWN.
3. FOR HEIGHT OF FLUE HOLE, LOWER HORIZONTAL CENTRELINE
OF TEMPLATE B DOWN BY AN AMOUNT DEPENDING ON
THE SIDE CLEARANCE BETWEEN BOILER AND SIDE WALL, AS
SHOWN IN TABLE BELOW.
4. TAPE TEMPLATE B INTO SELECTED POSITION.
5. MARK ON THE CENTRE OF THE FLUE HOLE AS WELL AS THE
CIRCUMFERENCE.
6. IF USING THE OPTIONAL STAND-OFF KIT FOR UPWARD
PIPING MARK ON THE HOLE CENTRE AND CIRCUMFERENCE
OF THE DASHED CIRCLE.
7. PROCEED TO POINT 4 ABOVE:
TEMPLATE INSTRUCTIONS
INSTRUCTIONS FOR RH & LH SIDE EXIT FLUE
For mounting
Stand-off kit
WITHOUT
MIN. INSTALLED CLEARANCE FOR ACCESS
TO LOWER CONTROLS - 150 mm
OF 28 kW BOILER
BOTTOM
SI
D
E
O
F
BO
IL
ER
(
MIN
. S
IDE
CL
EA
R
AN
CE
1
5 m
m)
S
ID
E
O
F
BO
IL
ER
(
MI
N.
SID
E C
LE
A
RA
NC
E
15
m
m)
L
L
L
c
c
c
c
c
OFFSET AT 15 mm MIN CLEARANCE
OF
F SE
T
A T 1
5
mm
M
I N
C
L EA
RAN
CE
OFFSET FOR 0.5 m FLUE
OFF
SET
F
OR
0.
5
m F
L UE
OFFSET FOR 1 m FLUE
OFF
SET
F
OR
1
m F
L UE
OFFSET FOR 1.5 m FLUE
OFF
SET
F
OR
1.
5
m F
L UE
OFFSET FOR 2 m FLUE
OFF
SET
F
OR
2
m F
L UE
OFFSET FOR 2.5 m FLUE
OFF
SET
F
OR
2.
5
m F
L UE
OFFSET FOR 3 m FLUE
OFF
SET
F
OR
3
m F
L UE
R.H. FLUE OUTLET
WALL MOUNTING TEMPLATE
L.H
. F
LU
E O
U TL
ET
W AL
L
M OU
N TIN
G TE
M PL
ATE
C
UT
AL
O
NG
D
OT
TE
D
LIN
E
CORNER OF WALL
FOR R.H. OUTLET
C OR
N ER
O
F W
ALL
FO
R L.
H . O
U TL
ET
A
B
For mounting
Stand-off kit
WITH
FLUE DUCT DOWNWARD
OFFSET DIMENSIONS
1 3 m m 26 mm
3 9 m m 5 2 m m
6 5 m m
7
8
m
m
5 mm
BOILER TO SIDE
WALL CLEARANCE
0.5 m
1.0 m
1.5 m
2 m 2.5 m
3 m
15 mm
12
7 m
m D
I A.
C
I RC
LE
(
5 ”)
CENTRAL
HEATING
FLOW
DHW
(HOT)
OUTLET
GAS
INLET
DHW
(COLD)
INLET
CENTRAL
HEATING
R E T U R N
127 mm DIA. CIRCLE (5”)
00331388
1 .
2 .
3 .
4 .
5 .
6 .
WALL MOUNTING TEMPLATE
ATTENTION !
THIS BOILER HAS A COPPER HEAT EXCHANGER.
APPROPRIATE WATER TREATMENT MUST BE USED
THE FLUE TERMINAL POSITION IS IN THE CENTRE OF THE
BOILER. USE SHOULD BE MADE OF THIS TEMPLATE & DUE
NOTE TAKEN OF THE POSITION OF THE TERMINAL ON THE
OUTSIDE WALL. FOR VERTICAL AND TWIN FLUE APPLICATIONS
REFER TO THE INSTALLATION INSTRUCTIONS.
THE BOILER SETTING PRESSURE IS PRE-SET DURING
MANIFACTURE. IN CASE OF DIFFICULTY, PLEASE ENSURE
ADEQUATE INLET PRESSURE OF 20 mbar NATURAL GAS.
THE GAS SUPPLY PIPEWORK TO THE BOILER SHOULD
BE A MINIMUM 22 mm DIAMETER COPPER.
FOR CORRECT OPERATION OF THE BOILER IGN ITION
SEQUENCE, ELECTRICAL POLARITY MUST BE CORRECT.
REFER TO INSTALLATION INSTRUCTIONS FOR ELECTRICAL
CONNECTIONS AND SYSTEM WIRING DIAGRAM.
THE BOILER IS SUITABLE FOR PUMPED CIRCUITS ONLY.
GRAVITY CIRCUITS MUST NOT BE USED. USE 22 mm
PIPEWORK FOR ON FLOW AND RETURN CONNECTIONS
IF THE BOILER IS TO BE LEFT SWITCHED OFF AFTER
COMMISSIONING DUE CARE MUST BE TAKEN TO AVOID
FREEZING.
PLEASE NOTE THE POINTS BELOW AND RIGHT
MIN. INSTALLED CLEARANCE FOR ACCESS
TO LOWER CONTROLS - 150 mm
OF 24 kW BOILER
BOTTOM
127 mm DIA. CIRCLE (5”)
Flue duct hole
o f f s e t V ( m m )
1 3
0.
5
2 6
3 9
5 2
6 5
See wall mounting plate
7 8
1
1.5
2
2.5
3
Distance in metres from side of boiler wall H (m)
H
V
INSTALLATION