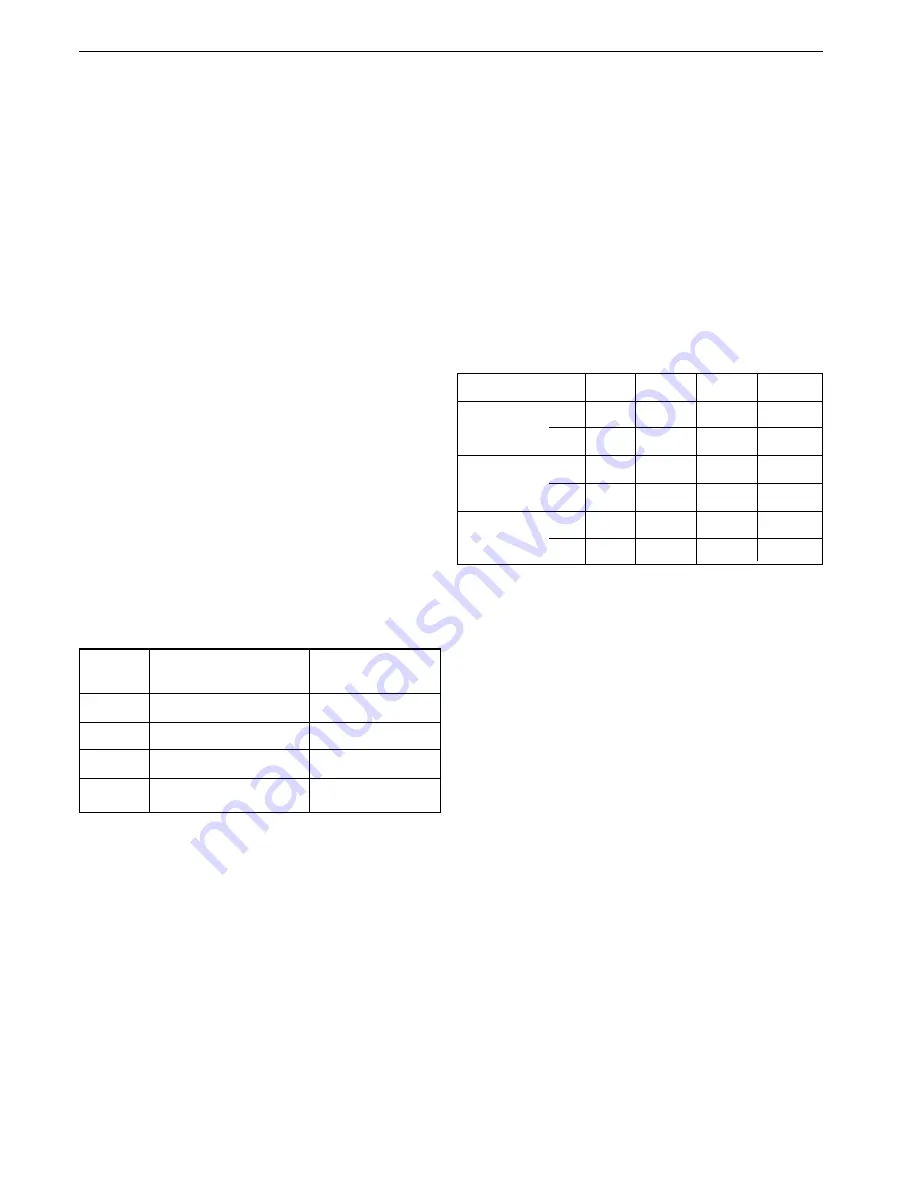
8
Classic LX, RS -
Installation
GENERAL
IMPORTANT.
It is absolutely ESSENTIAL to ensure, in practice,
that products of combustion discharging from the terminal
cannot re-enter the building or any other adjacent building
through ventilators, windows, doors, other sources of natural air
infiltration or forced ventilation/air conditioning.
If this should occur, the appliance MUST be turned OFF,
labelled 'unsafe' and corrective action taken.
TERMINAL
The terminal assembly can be adapted to accommodate various
wall thicknesses. Refer to Frame 4 - Unpacking.
AIR SUPPLY
Detailed recommendations for air supply are given in
BS.5440:2. The following notes are for general guidance:
1.
It is NOT necessary to have a purpose provided air vent in
the room or internal space in which the boiler is installed.
2.
If the boiler is to be installed in a cupboard or compartment,
permanent air vents are required (for cooling purposes) in
the cupboard/compartment, at both high and low levels. The
air vents must either communicate with room/internal space,
or be direct to outside air. The minimum effective areas of
the permanent air vents, required in the cupboard/
compartment, are specified as follows and are related to
maximum rated heat input.
3.
Both air vents MUST communicate with the same room or
internal space or MUST be on the same wall to outside air.
4.
In siting the air vents care must be taken to avoid the
freezing of pipework.
Table 4 - High and low vent areas
WATER CIRCULATION SYSTEM
The boiler must NOT be used for direct hot water supply. For
the types of system and correct piping procedure refer to
'Introduction' and Frame 1.
The central heating system should be in accordance with
BS. 6798 and, in addition, for smallbore and microbore
systems, BS. 5449.
The domestic hot water system, if applicable, should be in
accordance with the relevant recommendations of BS. 5546.
Copper tubing to BS. 2871:1 is recommended for water carrying
pipework.
The hot water storage cylinder MUST be of the indirect type
and should preferably be manufactured of copper.
Single feed, indirect cylinders are not recommended and MUST
NOT be used on sealed systems.
THERMOSTATIC RADIATOR VALVES
Caradon Plumbing Limited
recommend that heating systems
utilising full thermostatic radiator valve control of temperature in
individual rooms should also be fitted with a room thermostat
controlling the temperature in a space served by radiators not
fitted with such a valve, as stated in BS. 5449.
When thermostatic radiator valves are used, the space heating
temperature control over a living / dining area or hallway having
a heating requirement of at least 10% of the boiler heat output
should be achieved using a room thermostat, whilst other rooms
are individually controlled by thermostatic radiator valves.
However, if the system employs thermostatic radiator valves on
all radiators, or two port valves without end switches then a
bypass must be fitted in order to ensure a flow of water should
all the valves be in the closed position.
ELECTRICAL SUPPLY
Wiring external to the appliance MUST be in accordance with
the current I.E.E. (BS. 7671) Wiring Regulations and any local
regulations which apply.
The point of connection to the mains should be readily
accessible and adjacent to the boiler, except for bathroom
installations; the point of connection to the mains MUST be
situated outside of the bathroom.
Note.
Where a room sealed appliance is installed in a room containing
a bath or shower then the appliance and any electrical switch or
appliance control utilising mains electricity should be so situated
that it cannot be touched by a person using the bath or shower.
The hot water cylinder and ancillary pipework not forming part of
the useful heating surface should be lagged to prevent heat loss
and any possible freezing - particularly where pipes run through
roof spaces and ventilated underfloor spaces.
IMPORTANT.
The boiler must be vented
(not on sealed systems.)
Draining taps MUST be located in accessible positions, which
permit the draining of the whole system - including the boiler and
hot water storage vessel. They should be at least 1/2" BSP
nominal size and be in accordance with BS. 2879.
The boiler is fitted with a special drain plug (provided) to drain
the BOILER ONLY, in the event of the system drain plug being
unable to do so. The hydraulic resistance of the boilers, at
MAXIMUM OUTPUT with an 11
0
C (20
0
F) temperature
differential, are shown in Table 5.
Table 5 - Water flow rate and pressure loss
Boiler Size
RS230
RS240
RS250
RS260
Boiler
kW
8.8
11.7
14.7
17.6
Output
Btu/h 30 000
40 000
50 000
60 000
Water flow
l/min
11.4
15.2
19.0
22.8
Rate
gal/h
150
200
250
300
Pressure
mbar
24.0
22.0
34.0
45.0
Loss
in wg
9.6
9.0
13.6
18.0
Boiler
Air from room/internal
Air direct
Space cm
2
(in.
2
)
Outside cm
2
(in.
2
)
RS230
102 (16)
51 (8)
RS240
135 (21)
68 (11)
RS250
170 (26)
83 (13)
RS260
198 (31)
102 (16)
Summary of Contents for Classic LXRS 230
Page 1: ......