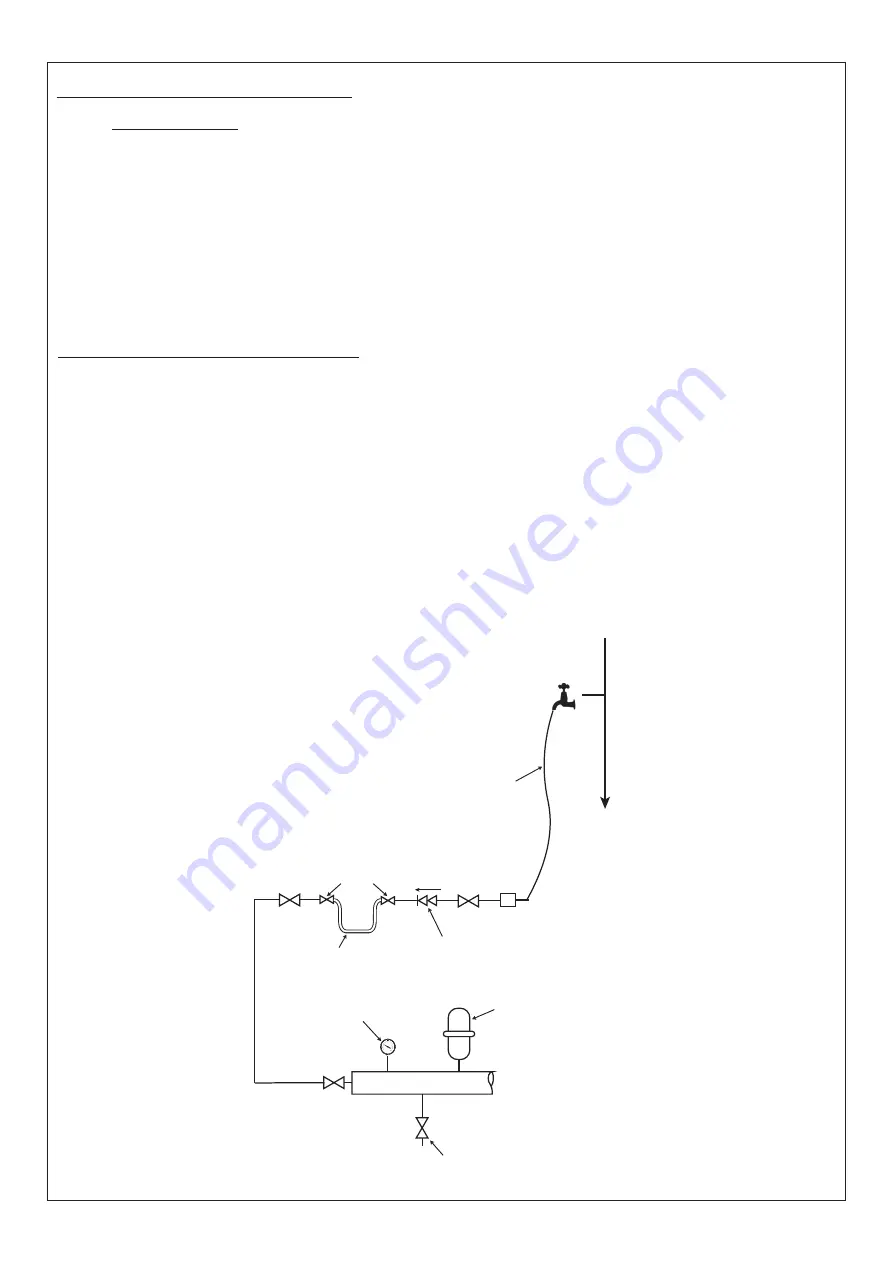
7
Plate Heat Exchanger Package
Section 4 - Installation Requirements
4.1 INSTALLATION AREA AND
DIMENSIONS
Ensure adequate access for boiler and package installation.
Ensure at least 450 mm clearance from the front of the
appliance to allow servicing.
The condensate drain must have a 1 in 20 fall away from the
appliance.
Adequate room above the boilers must allow the installation
and serving of the boiler flue system. Further information
concerning flue and condensate drain connection can be
found in the boiler installation manual.
4.2 SYSTEM REQUIREMENTS
1.
Ancillary components can be connected to the system via
the G3/4” isolation valve on the boiler return pipework.
See diagram below for guidance (diagram for illustration
purposes only).
2.
The method of filling, refilling, topping up or flushing
sealed primary circuits from the mains via a temporary
hose connection is only allowed if acceptable to the local
water authority.
3.
The filling device must be connected to comply with the
water regulations, as shown below. This may involve fitting
an a suitable WRAS approved isolator valve to the mains
supply and appropriate backflow prevention device.
Pressure relief valve (Supplied with the package)
Pressure Gauge
Expansion Vessel
Drain Cock
Return
Double check valve or
RPZ assembly
(note direction of flow)
Additional
stop valve
Hosepipe
(disconnect
after filling)
Water
Supply
Temporary Hose
(disconnect
after filling)
Hose unions
G3/4”
Valve
4.
A spring-loaded non-adjustable 3 bar pressure relief valve
complying with the relevant standards of BS6759 Pt1
is fitted close to the boiler with no intervening valve or
restriction.
5.
A manual testing device.
6. The safety valve outlet should be piped to ensure water or
steam discharge cannot create a hazard to personnel or
damage electrical components or wiring.
Pressure gauge (Supplied with the package)
A pressure gauge covering at least 0-6 bar is fitted to the
return pipework, visible from the filling point.
Expansion vessel (Supplied with the package)
7. A diaphragm type expansion vessel complying with BS.
EN 13831 must be fitted, with a valve in the normally open
positioned protected using a lockshield from unauthorised
closure.
8. The vessel capacity must be adequate to accept the
expansion of system water when heated to 85 °C.
9. The charge pressure must not be less than the static
water head above the vessel. The pressure attained in the
system when heated to 85 °C should be at least 0.35 bar
less than the lift pressure of the pressure relief valve.
The 4L expansion vessel supplied is suitable for all
appliances.
System drain cock (Supplied with the package)
A drain cock is fitted to the lowest section of the return
pipework. A second drain cock is fitted above the NRV after
the boiler pump.