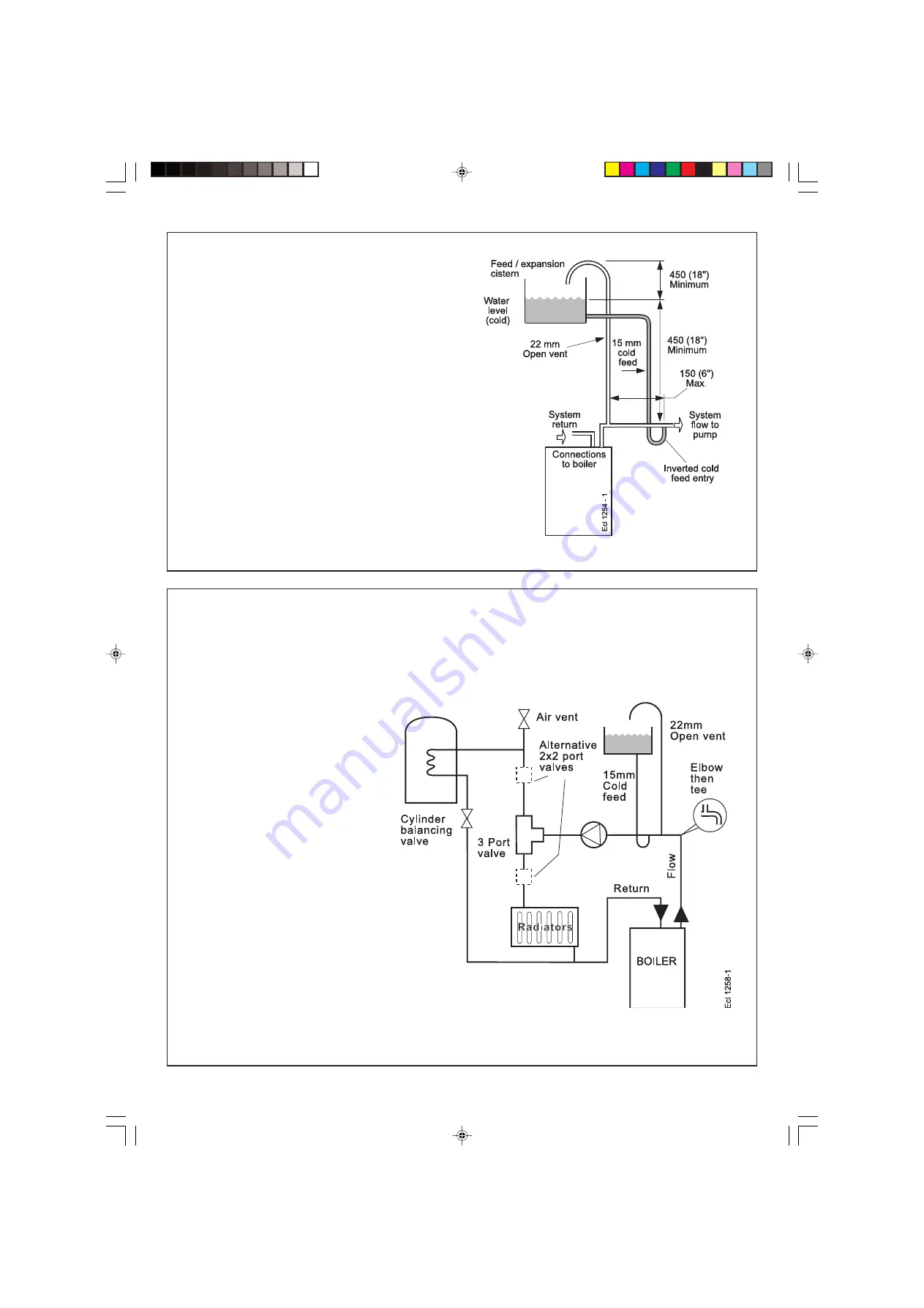
10
icos
-
Installation & Servicing
GENERAL
3
OPEN VENT SYSTEM REQUIREMENTS
4
SCHEMATIC PIPEWORK AND SYSTEM BALANCING
The boiler does not normally need a bypass but at least some
radiators on the heating circuit, of load at least 10% of the
minimum boiler output, must be provided with twin lockshield
valves so that this minimum heating load is always available
(see footnote re. thermostatic radiator valves).
Return & flow
connections
load 30 - 60 = 22 mm
load 70 - 80 = 28 mm
Balancing
1.
Set the programmer to ON for both CH
and HW. Turn the cylinder thermostat
down. Close the manual or thermostatic
valves on all radiators, leaving the twin
lockshield valves (on the radiators
referred to above) in the open position.
Turn up the room thermostat and adjust
these lockshield valves to give boiler flow
and return temperatures not more than
20
o
C apart. These valves should now be
left as set.
2.
Open all manual or thermostatic radiator
valves and adjust the lockshield valves
on remaining radiators to give around
11
o
C temperature drop at each radiator.
3.
Turn up the cylinder thermostat and
adjust the cylinder balancing valve so
that the cylinder achieves a maximum
flow consistent with adequate flow to the
radiators. Check that with only the
domestic hot water loop in circuit a
differential temperature of 20
o
C across
the boiler is not exceeded.
4.
Adjust room and cylinder thermostats
and programmer to NORMAL settings.
The system should be vented directly off the boiler flow pipe, as
close to the boiler as possible. The cold feed entry should be
inverted and MUST be positioned between the pump and the vent,
and not more than 150mm (6") away from the vent connection.
Note.
Combined feed and vent pipes may also be fitted.
There should be a minimum height 450mm (18") of open vent
above the cistern water level. If this is not possible refer to
Frame 5
.
The vertical distance between the highest point of the
system and the feed/expansion cistern water level MUST not be
less than 450 mm (18"). The pump must be fitted on the flow side of
the boiler.
A suitable pump is a domestic circulator capable of providing a
maximum 11
o
C (20
o
F) temperature differential across the boiler with the
whole of the heating circuit open (e.g. Grundfos UPS 15/50, 15/60 or
equivalent). With the minimum flow circuit allowed by the controls the
differential must not exceed 25
o
C. (18
o
C for the HE15)
The vertical distance between the pump and feed/expansion cistern
MUST comply with the pump manufacturer's minimum requirements, to
avoid cavitation. Should these conditions not apply either lower the
pump position or raise the cistern above the minimum requirement
specified by
Caradon Ideal Limited.
The isolation valves should be
fitted as close to the pump as possible.
200212-10.pmd
9/5/2005, 8:58 AM
10