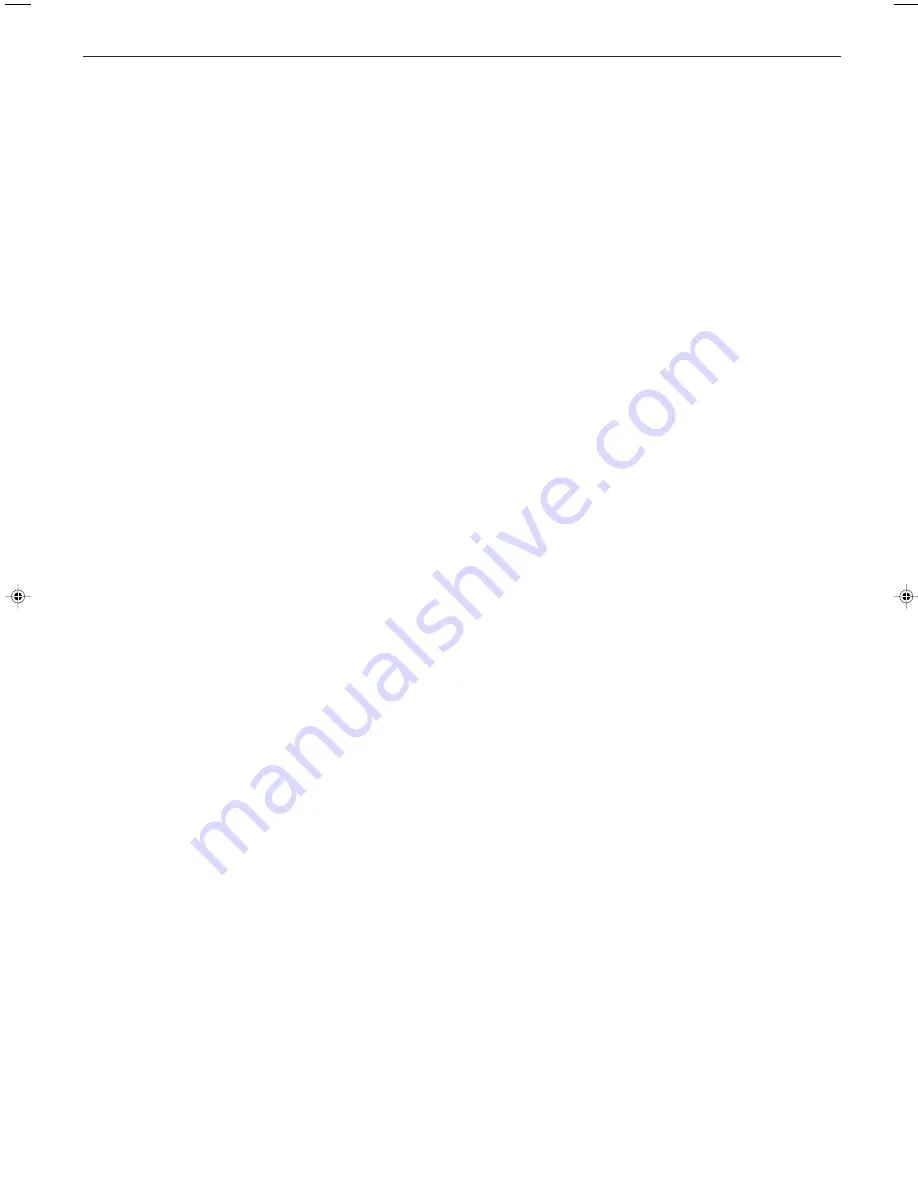
GENERAL
4
Mexico Super CF495 - CF4140
-
Installation & Servicing
Operatives should be knowledgeable in handling techniques
when performing these tasks and the following precautions
should be considered:
•
Split the boiler down to reduce the weight, e.g. remove casing
and hardware pack. Refer to Frame 9.
•
Be physically capable.
•
Use PPE as appropriate, e.g. gloves, safety footwear.
During all manoeuvres and handling actions, every attempt
should be made to ensure the following unless unavoidable
and/or the weight is light.
•
Keep back straight.
•
Avoid twisting at the waist.
•
Avoid upper body/top heavy bending.
•
Always grip with the palm of the hand.
•
Use designated hand holds.
•
Keep load as close to the body as possible.
•
Always use assistance if required.
OPTIONAL EXTRA KITS
Programmer Kit
Fits neatly within the casing. Separate fitting
instructions are included with this kit.
Overheat
Is available to allow the boiler to be used
Thermostat Kit
on sealed water systems.
CURRENT GAS SAFETY (INSTALLATION AND USE)
REGULATIONS OR RULES IN FORCE.
The appliance is suitable only for installation in GB and IE and
should be installed in accordance with the rules in force.
In GB, the installation must be carried out by a CORGI
Registered Installer. It must be carried out in accordance with
the relevant requirements of the:
•
Gas Safety (Installation and Use) Regulations
•
The appropriate Building Regulations either The Building
Regulations, The Building Regulations (Scotland), Building
Regulations (northern Ireland).
•
The Water Fittings Regulations or Water byelaws in Scotland.
•
The Current I.E.E. Wiring Regulations.
Where no specific instructions are given, reference should be
made to the relevant British Standard Code of Practice.
In IE, the installation must be carried out by a Competent Person
and installed in accordance with the current edition of I.S.813
"Domestic Gas Installations", the current Building Regulations
and reference should be made to the current ETCI rules for
electrical installation.
Detailed recommendations are contained in the following British
Standard Codes of Practice:
BS. 6891
Low pressure installation pipes.
BS. 6798
Installation of gas fired hot water boilers of rated
input not exceeding 60 kW.
BS. 5449:1
Forced circulation hot water systems (small bore
and microbore domestic central heating systems).
BS. 5546
Installation of gas hot water supplies for domestic
purposes (2nd Family Gases).
BS. 5440: 1
Flues for gas appliances of rated input not
exceeding 60 kW.
BS. 5440: 2
Ventilation for gas appliances of rated input not
exceeding 60 kW.
BS 7593
Treatment of water in Domestic Hot Water Central
Heating Systems.
Health and Safety Document No. 635.
The Electricity at Work Regulations, 1989.
Manufacturer’s notes must NOT be taken in any way as
overriding statutory obligations.
IMPORTANT.
These appliances are certificated by the British
Standards Institution for safety and performance. It is
important, therefore, that no external control devices, e.g. flue
dampers, economisers etc., are directly connected to these
appliances unless covered by these Installation and Servicing
Instructions or otherwise recommended by
Caradon Ideal
Limited
in writing. If in doubt please enquire.
Any direct connection of a control device not approved by
Caradon Ideal Limited
could invalidate the BSI Certification
and the normal appliance warranty. It could also infringe the
Gas Safety Regulations and the above regulations or other
statutory requirements.
SAFE HANDLING OF SUBSTANCES
Care should be taken when handling the boiler insulation
panels, which can cause irritation to the skin. No asbestos,
mercury or CFCs are included in any part of the boiler.
LOCATION OF BOILER
The boiler must be installed on a flat and level floor, capable of
adequately supporting the weight of the boiler and any ancillary
equipment.
The boiler may be fitted on a combustible floor.
Insulation is not necessary, unless required by the local authority.
The boiler must not be fitted outside.
The boiler must not be installed in a bedroom or in a room
containing a bath or shower.
Timber Framed Buildings
If the boiler is to be fitted in a timber framed building it should
be fitted in accordance with the Institute of Gas Engineering
document IGE/UP/7:1998.
Compartment Installations
A compartment used to enclose the boiler MUST be designed
and constructed specially for this purpose.
An existing cupboard or compartment may be used, providing it
is modified for the purpose.
Details of essential features of cupboard/compartment design,
including airing cupboard installation, are to conform to the
following:
!
!
!
!
!
BS. 6798.
!
!
!
!
!
The position selected for installation MUST allow
adequate space for servicing in front of the boiler
and for air circulation around the boiler.
!
This position MUST also permit the provision of a
satisfactory flue and an adequate air supply.
!
For the minimum clearances required for safety and
subsequent service see Frame 2.
GAS SUPPLY
The local gas supplier should be consulted, at the installation
planning stage, in order to establish the availability of an
adequate supply of gas. An existing service pipe must NOT be
used without prior consultation with the local gas supplier.
The boiler is to be installed only on a gas supply with a
governed meter.
A gas meter can only be connected by the local gas supplier or
by a local regional contractor.
Check that the appliance is suitable for the proposed gas
supply. An existing meter should be checked, preferably by the
gas supplier, to ensure that the meter is adequate to deal with
the rate of gas supply required. A
minimum
gas pressure of
20mbar MUST be available at the boiler inlet, with the boiler
operating.
Installation pipes MUST be fitted in accordance with BS. 6891.
In IE refer to I.S. 813:2002. Pipework from the meter to the boiler
MUST be of an adequate size.
200944-1.p65
3/8/2004, 3:41 PM
4