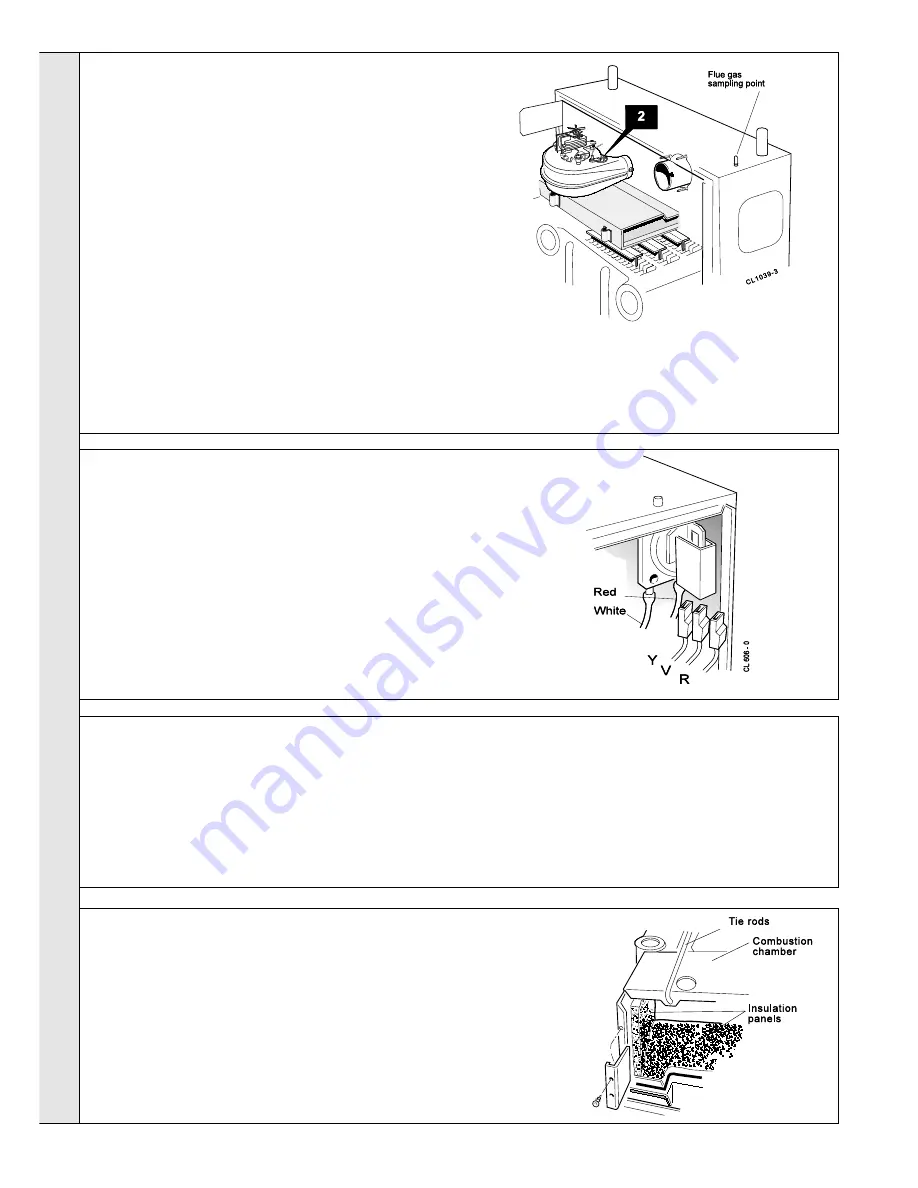
32
Classic FF -
Propane Installation
SERVICING
67 COMBUSTION CHAMBER INSULATION REPLACEMENT
66 PRINTED CIRCUIT BOARD (PCB) REPLACEMENT
65 AIR PRESSURE SWITCH (APS) REPLACEMENT
64 FAN REPLACEMENT
1.
Refer to Frame 56.
2.
Remove the burner and air box assembly.
Refer to Frame 51.
3.
Remove the 4 tie rods.
4.
Remove the combustion chamber.
5.
Remove the 2 side panel retaining brackets.
6.
Remove the side insulation panels.
7.
Remove the front and rear
insulation panels.
8.
Fit the new front and rear
insulation panels.
9.
Fit the new side panels and
retain with the brackets and
screws previously removed.
10.
Re-assemble in reverse order.
1.
Refer to Frame 56.
2.
Remove the 2 silicon rubber tubes from the fan sensing points.
3.
Disconnect the fan leads.
4a. Rear flue.
Slacken the M4 screw securing the flue connector to the
fan. Disconnect the connector from the fan and slide into the flue.
4b. Side or top flue.
Slacken off two M4 screws securing the flue elbow
and flue connector. Disconnect the flue connector from the elbow and
slide into the flue. Remove the flue elbow.
5.
Disconnect the silicon rubber tube from the rear of the collector hood.
6.
Slacken the two M5 nuts on the front tie rods, releasing the tie rods
from the combustion chamber.
7.
Remove the M5 central fixing screw at the rear of the collector hood
and remove collector hood / fan assembly.
8.
Remove the three M4 screws retaining the fan to the collector hood.
9.
Fit the new fan and re-assemble in reverse order, ensuring the fan
leads, and 3 sensing tubes are reconnected.
10.
Check the operation of the boiler.
5.
Disengage the PCB from the mounting posts and withdraw
from the control box.
6.
Fit the new PCB and re-assemble in reverse order.
7.
Check the operation of the boiler.
Fuse.
To change the fuse, prise it out of the holder and disengage
the fuse. Refer to Frame 72 for fuse location.
Note.
Refer to Frame 72 of 'Exploded Views' for
illustration of the procedure detailed below.
1.
Refer to Frame 56.
2.
Remove the fixing screws and swing the control box down
into the servicing position.
3.
Disconnect the detection lead from the PCB.
4.
Unplug all the Molex connectors from the PCB.
1.
Refer to Frame 56.
2.
Remove the APS fixing screw.
3.
Remove both sensing tubes from the APS.
4.
Remove the 3 electrical connections from the APS.
5.
Fit the new APS and reassemble in reverse order.
6.
Check the operation of the boiler.
SER
VICING