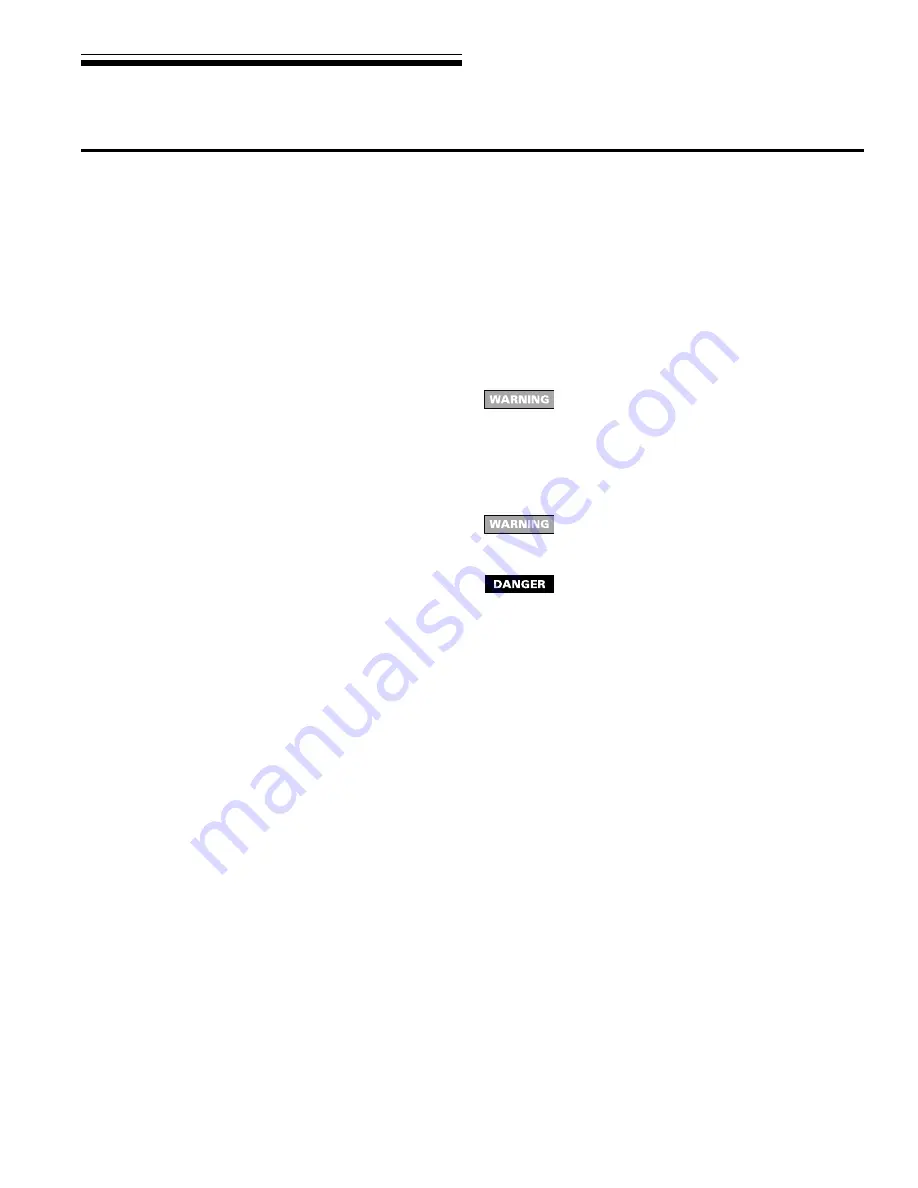
GWA
Gas-Fired Water Boilers –
Boiler Manual
7
Part Number 670 01 1001 00
Perform hydrostatic pressure test
Pressure test boiler before attaching water or gas piping or electrical
supply (except as noted below).
Prepare boiler for test
1. Remove the shipping nipple (from GWA supply tapping) and
remove the boiler relief valve. Temporarily plug the relief valve
tapping with a ¾" NPT pipe plug.
2. Remove 1¼" nipple, reducing tee and drain valve from
accessory bag. Install in boiler return connection as shown on
in Figure 19, item 3, page 32. Install circulator on either the
return or supply.
3. Remove 1¼" nipple, 1¼" tee, bushing and pressure/temperature
gauge from accessory bag. Pipe to boiler supply connection as
shown in Figure 19, item 2, page 32. (Use pipe dope sparingly.)
4. Connect a hose to boiler drain valve, the other end connected
to a fresh water supply. Make sure hose can also be used to
drain boiler after test.
5. Connect a nipple and shutoff valve to system supply connection
on the 1¼" tee. This valve will be used to bleed air during the fill.
(Valve and nipple are not included with boiler.)
6. Connect a nipple and shutoff valve to system return connection
(at circulator flange if circulator installed on return). This valve
will be used to bleed air during the fill. (Valve and nipple are not
included with boiler.)
7. Temporarily plug the air elimination tapping (next to supply
tapping).
2
Prepare boiler
continued
Pressure test
Fill and pressure test
1. Open the shutoff valves you installed on supply and return
connections.
2. Slowly open boiler drain valve and fresh water supply to fill
boiler with water.
3. When water flows from shutoff valves, close boiler drain valve.
4. Close shutoff valves.
5. Slowly reopen boiler drain valve until test pressure of not more
than 45 psi is reached on the pressure/temperature gauge.
6. Test at no more than 45 psi for no more than 10 minutes.
Do not leave boiler unattended. A cold water fill could
expand and cause excessive pressure, resulting in
severe personal injury, death or substantial property
damage.
7. Make sure constant gauge pressure has been maintained
throughout test. Check for leaks. Repair if found.
Leaks must be repaired at once. Failure to do so can
damage boiler, resulting in substantial property
damage.
Do not use petroleum-based cleaning or sealing
compounds in boiler system. Severe damage to boiler
will occur, resulting in substantial property damage.
Drain and remove fittings
1. Disconnect fill water hose from water source.
2. Drain boiler at drain valve or out hose, whichever provides best
access to drain. Remove hose after draining if used to drain
boiler.
3. Remove nipples, valves and plus unless they will remain for
use in the system piping.
4. Remove plug from relief valve tapping. See Section 3, page 10,
to replace relief valve.
GWA
Gas-Fired Water Boilers –
Boiler Manual
30
Part Number 670 01 1001 00
Figure 17
Base assembly, manifold, orifices and burners
12 Replacement parts
continued
It em
number
D esc ript ion
Int ernat ional
C omf ort
P roduc t s
part number
Base assembly kit
GWA052 & GWA070
GWA105
GWA140
GWA175
GWA210
GWA245
381354200WT
381354201WT
381354202WT
381354203WT
381354204WT
381354205WT
1
Base side panel (in Base assembly)
2
Base front cross-tie assembly (in Base assembly)
3
Base back cross-tie assembly (in Base assembly)
4
Base access panel (in Base assembly)
5
Base pan angle, left side (in Base assembly)
6
Base pan angle, right side (in Base assembly)
7
Base pan (in Base assembly)
8
Burner rest (in Base assembly)
9
Base insulation kit
(includes insulation for
all base parts above
plus gasket material
needed between block
assembly and base)
GWA052 to GWA140
GWA175 to GWA245
381354210WT
381354211WT
10
Boiler leg kit
590424252WT
11
Manifold
GWA052
GWA070
GWA105
GWA140
GWA175
GWA210
GWA245
591126615WT
591126616WT
591126617WT
591126618WT
591126619WT
591126556WT
591126557WT
12
Main burner orifice, sea level
560528997WT
13
Burner, stainless steel
512200077WT
14
Burner with pilot
bracket
(not shown)
Standing pilot
512200079WT
Spark-ignited pilot
512200078WT
15
Screw, 10-32 x
3
/
8
STP type D hx, washer head
slot ZP
available at
local supply
house
16
Rollout thermal fuse element
512050230WT