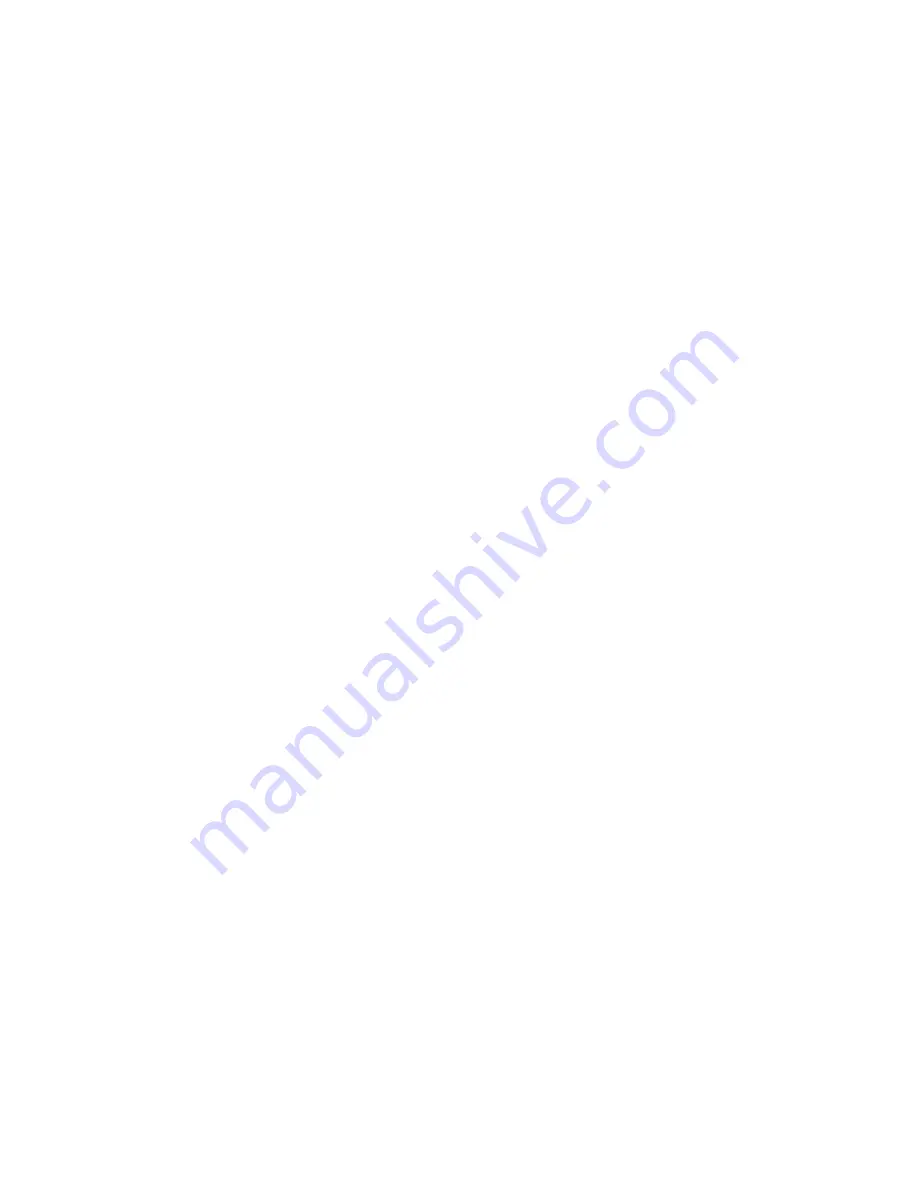
GWA
Gas-Fired Water Boilers –
Boiler Manual
10
Part Number 670 01 1001 00
Table 4
Water pipe size (based on 20 °F rise)
General
If installation is to comply with ASME or Canadian requirements,
an additional high temperature limit is needed. Install control in supply
piping between boiler and isolation valve. Set second control to
minimum 20 °F above setpoint of first control. Maximum allowable
setpoint is 240 °F. See page 19 for wiring.
A low water cutoff device is required when boiler is installed above
radiation level or by certain state or local codes or insurance
companies. Use low water cutoff designed for water installations.
Electrode probe-type is recommended. Purchase and install in tee
supply piping above boiler.
Use backflow check valve in cold water supply if required by local
codes.
See Table 4 and Figure 5 (diaphragm-type or bladder-type expansion
tank) or Figure 6 (closed-type expansion tank) on page 11 for near-
boiler piping for systems designed for return water at least 130 °F.
See page 12 (Figures 8 and 9) for near-boiler piping for low-
temperature or high-volume systems.
See page 11 (Figure 7) for boilers used with refrigeration systems.
Near-boiler piping
3
Install water piping
Relief valve
Install relief valve vertically in ¾" tapping on side of boiler. See the
tag attached to the relief valve for manufacturer’s instructions.
To avoid water damage or scalding due to valve
operation, discharge line must be connected to relief
valve outlet and run to a safe place of disposal.
Terminate the discharge line to eliminate possibility
of severe burns should the valve discharge.
• Discharge line must be as short as possible and be
the same size as the valve discharge connection
throughout its entire length.
• Discharge line must pitch downward from the valve
and terminate at least 6" above the floor drain where
any discharge will be clearly visible.
• The discharge line shall terminate plain, not threaded,
with a material serviceable for temperatures of 375 °F
or greater.
• Do not pipe the discharge to any place where freezing
could occur.
• No shutoff valve shall be installed between the relief
valve and boiler, or in the discharge line. Do not plug
or place any obstruction in the discharge line.
• Failure to comply with the above guidelines could
result in failure of the relief valve to operate, resulting
in possibility of severe personal injury, death or
substantial property damage.
• Test the operation of the valve after filling and
pressurizing system by lifting the lever. Make sure
the valve discharges freely. If the valve fails to operate
correctly, replace it with a new relief valve.
Water piping — multiple zone systems
Install system piping using either circulator zoning or zone valve
zoning. Install expansion tank on suction side of system circulator.
Always connect fill line only at the expansion tank — never at
another point in the system.
Circulator
The circulator is shipped loose (wiring pre-attached to boiler) to
allow you to locate it either in the return or supply piping, as desired.
See page 11 for a typical installation. Pipe the expansion tank to
the suction side of the circulator whenever possible. Install an air
separator in the supply piping. Connect the expansion tank to the
air separator only if the separator is on the suction side of the
circulator. Always install the system fill connection at the same point
as the expansion tank connection to the system. Figures 5 and 6
show typical near-boiler piping connections.
Expansion tank
Diaphragm-type or bladder-type expansion tank —
Figure 5
1. Ensure expansion tank size will handle boiler and system water
volume and temperature. Tank must be located in boiler return
piping as close to boiler as possible, before inlet side of circulator.
See tank manufacturer’s instructions for details.
2. Install an automatic air vent as shown.
Closed-type expansion tank — Figure 6
1. Ensure expansion tank size will handle boiler and system water
volume and temperature. See tank manufacturer’s instructions
for details.
2. Connect tank to ½" NPT tapping located behind supply outlet,
using ½" NPT piping. Pitch any horizontal piping up towards
tank 1 inch per 5 feet of piping.
Undersized expansion tanks cause system water to
be lost from relief valve and makeup water to be
added through fill valve. Eventual section failure can
result.
Near-boiler piping
continued
Boiler model
number
To
system
From
system
GWA052
¾"
¾"
GWA070
1"
1"
GWA105
1"
1"
GWA140
1"
1"
GWA175
1¼"
1¼"
GWA210
1¼"
1¼"
GWA245
1½"
1½"
GWA
Gas-Fired Water Boilers –
Boiler Manual
27
Part Number 670 01 1001 00
11 Troubleshooting
Verify proper operation after servicing. • See vent
damper manufacturer’s instructions packed with vent
damper for additional information. Failure to comply
could result in severe personal injury, death or
substantial property damage.
Figure 15
Manually opening vent damper
Label all wires prior to disconnection when servicing
controls. Wiring errors can cause improper and
dangerous operation.
Never jumper (bypass) rollout thermal fuse element
or any other device except for momentary testing as
outlined in “Chart 1”, page 28. Severe personal injury,
death or substantial property damage can result.
Burner access panel must be in position during boiler
operation to prevent momentary flame rollout on
ignition of main flame. Severe personal injury or
substantial property damage will result.
Before troubleshooting:
1. Have the following items:
a. Voltmeter that can check 120 VAC and 24 VAC.
b.
Microammeter with a scale range of 0-10.
c. Continuity checker.
d. U-tube manometer.
2. Check for 120 VAC (minimum 102 VAC to maximum 132 VAC)
to boiler.
3. Make sure thermostat is calling for heat and contacts (including
appropriate zone controls) are closed. Check for 24 VAC
between thermostat wire nuts and ground.
Troubleshooting sequence:
1. Before proceeding, check for:
•
Loose connections, blown fuse or service switch off?
•
High limit switch set below boiler water temperature?
•
Thermostat set below room temperature?
•
Gas not turned on at meter or boiler?
•
Incoming gas pressure less than:
5" w.c. for natural gas? 11" w.c. for propane gas?
2. If all of the above check correctly, check gas pressures:
a. With boiler off
•
13" w.c. maximum natural or propane gas pressure
upstream of gas valve.
b.
With boiler on:
•
5" w.c. minimum natural gas pressure or 11" w.c.
propane gas pressure upstream of gas valve.
•
3.5" w.c. minimum natural gas pressure or 10" w.c.
propane gas pressure downstream tapping on gas
valve — Can be adjusted by regulator on gas valve.
c. If gas pressure is incorrect or gas is not available to boiler,
contact gas supplier to correct before proceeding further.
3. Check pilot operation - Follow “Lighting Instructions”, pages 20
and 21.
•
If gas is available and you cannot obtain a pilot flame, try
purging the gas line and cleaning pilot and pilot gas tubing.
Follow “Lighting Instructions” again. If you still cannot obtain
a flame, replace pilot burner and gas tubing. If this does not
allow you to obtain a pilot flame, replace gas valve.
•
If you obtain a pilot flame, but pilot will not remain on, replace
thermocouple. If this does not correct problem, replace gas
valve and pilot burner.
•
If pilot stays on, but main gas will not come on, proceed to
page 28.
In event of vent damper failure:
Effikal vent damper
If troubleshooting chart recommends replacing actuator and actuator
is not immediately available, damper blade can be fixed in an open
position to allow boiler operation. Manually turning blade can cause
actuator damage. Follow these instructions only in case of no heat
or damper actuator malfunction.
1.
Move damper service switch to Hold Damper Open position.
Apply call for heat to boiler. Damper blade should then rotate to
Open position and boiler will fire.
2. If step 1 does not open damper, manually rotate damper blade
to open position using wrench or pliers on flat shaft between
damper and actuator. Boiler will fire. Verify that damper service
switch is in Hold Damper Open position. (Figure 15)
3. Do not leave vent damper permanently in this position. Replace
actuator immediately. If vent damper is left in Open position,
boiler will not operate at published efficiencies.
Johnson Controls vent damper
If troubleshooting chart recommends replacing actuator and actuator
is not immediately available, damper blade can be fixed in an open
position to allow boiler operation. Follow these instructions only in
case of no heat or damper actuator malfunction. See Figure 15.
1. Turn off power to boiler.
Failure to turn off power to boiler can result in severe
personal injury, death or substantial property damage.
2. See vent damper manufacturer’s instructions for procedure to
fix vent damper in open position.
3. Turn on power to boiler.
4. Using wrench or pliers on flat shaft section, manually rotate
damper blade until green light turns on. Boiler will fire. (Figure 15)
5. Do not leave vent damper permanently in this position. Replace
actuator immediately. If vent damper is left in Open position,
boiler will not operate at published efficiencies.