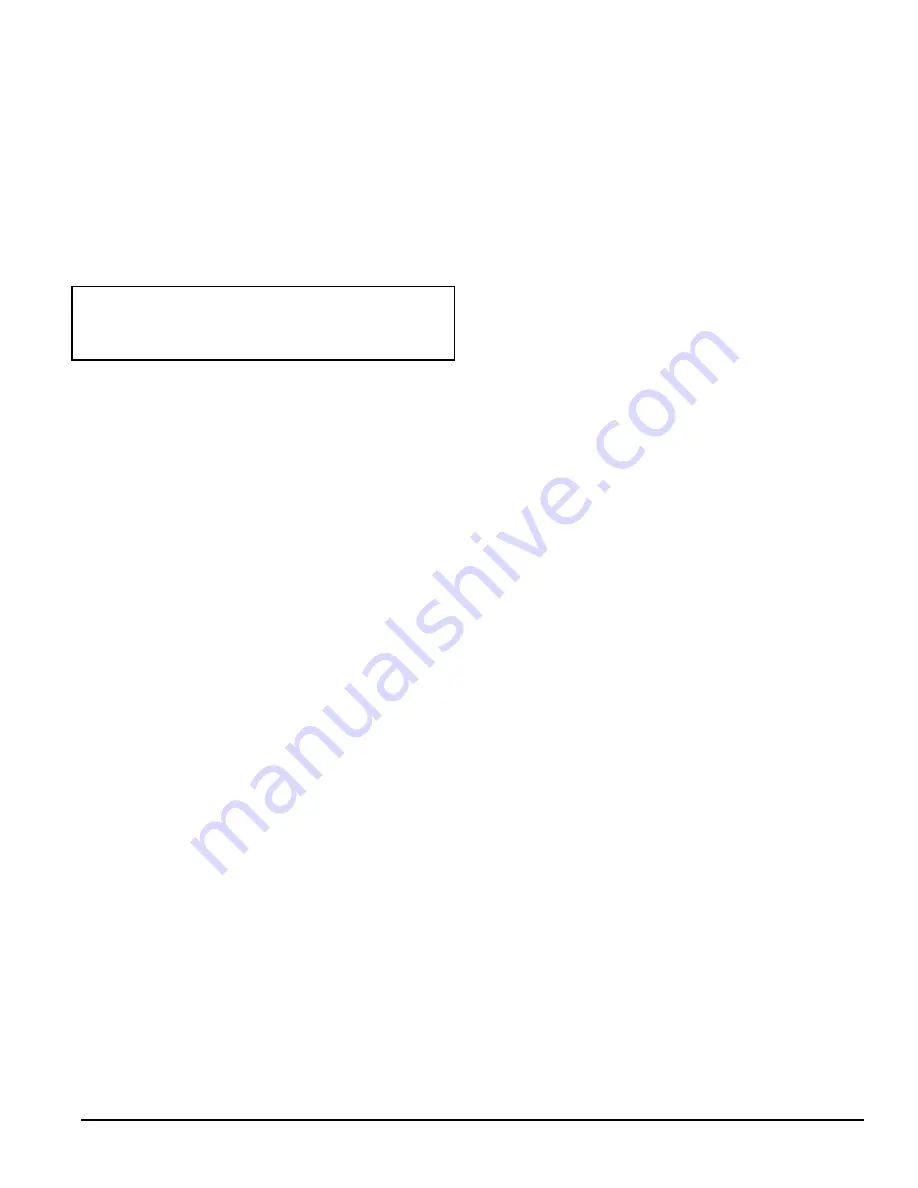
13
3.1.3) BLOCKED VENT SHUT-OFF (BVSO)
CLEANING
For continued safe operation, the Blocked Vent Shut-Off System
(BVSO) is required to be inspected and maintained annually by a
qualified agency.
1.
Disconnect the power to the appliance;
2.
Remove the two screws holding on the BVSO assembly cover;
3.
Remove the cover;
4.
Remove the two screws holding the control box to the heat
transfer tube assembly. Sliding the control box in the appropriate
direction will unlock it from the heat transfer tube assembly;
5.
Carefully remove any build-up from the thermal switch surface;
CAUTION
Do not dent or scratch the surface of the thermal switch.
If the thermal switch is damaged, replacement is
required.
6. Clear and remove any build-up or obstruction inside the heat
transfer tube;
7. Re-mount, lock and fasten the control box with the 2 screws
removed in step 4;
8.
Re-attach the assembly cover with the screws removed in step 2;
9.
Re-establish power to the appliance.
3.1.4) Burner drawer assembly
Remove the drawer assembly. Clean all foreign matter from the
retention head and electrodes. If a Beckett AFG burner was installed,
the burner will have to be removed to check the retention head.
3.1.5) Nozzle
Replace the nozzle with the one specified in Tables 3.1 to 3.4, p. 15 to
18.
3.1.6) Oil
filter
Tank filter
The tank filter should be replaced as required.
Secondary filter
The 10 micron (or less) filter cartridges should be replaced annually.
3.1.7) Air
filters
Air filters are the disposable type. They should be replaced at least
once a year. Dusty conditions, presence of animal hair etc. may
require much more frequent filter changes. Dirty filters will impact
furnace efficiency and increase oil consumption.
3.1.8) Motor
lubrication
Do NOT lubricate the oil burner motor or the direct drive blower motor
as they are permanently lubricated.
3.1.9) CAS-2B combustion air kit (chimney
venting)
If used, check the CAS-2B combustion air kit for proper operation.
Check to see that the inlet screen is not plugged. Block the air inlet
completely and ensure that a zero smoke reading results. If a zero
smoke reading is not obtained, set up the burner as indicated in
Tables 3.1 to 3.4, p. 15 to 18.
Gradually block off the intake. The CO
2
should increase to a maximum
of 0.5 percentage points at the fully blocked condition. If not, check
that the VRV gate is pivoting freely and that the pivot rod is in a
horizontal position. Also, check that the counterweight has been
properly adjusted in accordance with CAS-2B installation instructions.
445 01 4054 06
Summary of Contents for FLO115DABR-C
Page 21: ...22 PARTS LIST Model MBO115DABR D B50040B 445 01 4054 06...
Page 23: ...PARTS LIST Model MBOV115DABR D B50041B 445 01 4054 06...
Page 25: ...26 PARTS LIST Model LBO125DABR13 D B50038C 445 01 4054 06...
Page 27: ...PARTS LIST Models LBO145DABR34 D OLR182A16C B50039F 445 01 4054 06...
Page 29: ...PARTS LIST Model FLO115DABR C OLF140C12C B50042A 445 01 4054 06...