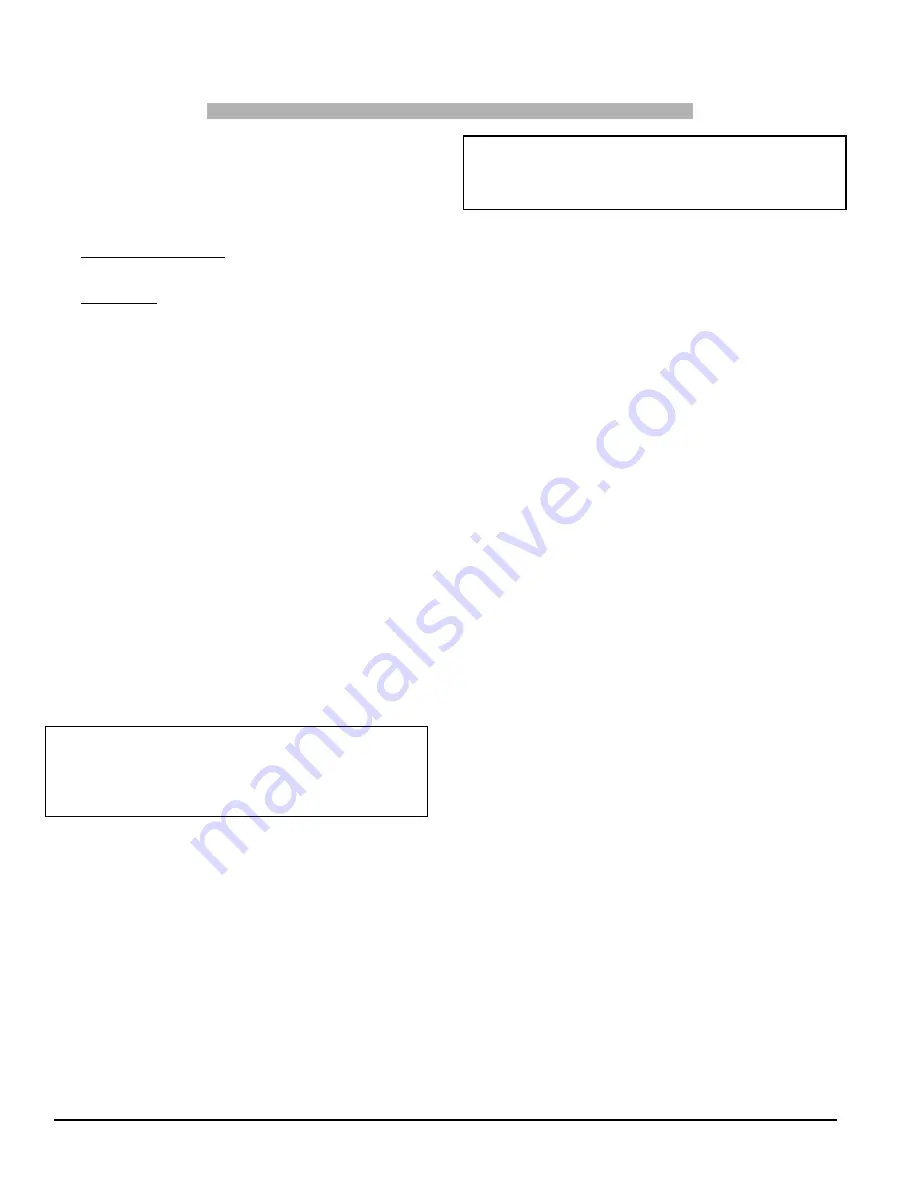
PART 2
OPERATION
2.1) SEQUENCE
OF
OPERATION
10
2.1.1) Sequence
of
operation
Beckett AFG, Riello 40-F and Aero F-FAC
1. Normally open contact (T-T) on primary relay closed when
thermostat calls for heat;
2.
AFG and F-FAC burner: The motor starts and spark is
established. The pump pressure builds and the oil supply
mechanism opens, admitting fuel to the nozzle;
3.
R40-F Burner: The burner motor starts. The burner motor fan
pre-purges the combustion chamber and vent for 10 seconds,
establishing the combustion air pattern. During this time the
solenoid valve holding coil pressure is approximately 100 psig.
The solenoid valve opens, allowing oil to flow through the nozzle.
At the same time, the burner motor ignition coil produces a spark;
4.
Spark ignites oil droplets;
5. Cad cell senses flame and burner continues to fire. Ignition
transformer ceases sparking (Riello R40-F);
6. After Fan-Limit control heats up to the factory set point, the
circulating air blower and electronic air cleaner start;
7. The circulating air blower and burner motor remain on until the
thermostat is satisfied. The ignition transformer continues to
spark (AFG). The solenoid valve remains open (R40-F);
Thermostat is satisfied:
8. Primary relay contacts open, solenoid valve closes (R40-F),
burner fan motor shuts down. The ignition transformer ceases
sparking (AFG);
9.
The Fan-Limit control bi-metal cools down to the factory set point
of 32°C (90°F), the circulating air blower and the electronic air
cleaner turn off.
2.2)
CHECKS AND ADJUSTMENTS
2.2.1) General
After initial installation and subsequent yearly maintenance calls, the
furnace must be thoroughly tested.
IMPORTANT
The burner must be functioning for at least 10 minutes
before any test readings are taken. Adjustments are to
be made according to the Technical Specifications in
this manual.
Open the oil bleed port screw and start the burner. Allow the oil to
drain into a container for at least 10 seconds. Once the oil flows
absolutely free of white streaks or air bubbles to indicate that no air is
being drawn into the suction side of the oil piping and pump, slowly
close and tighten the bleed screw. The burner should now fire. Adjust
the oil pressure as indicated in the Technical Specification Tables 3.1
to 3.4, p. 15 to 18.
2.2.2) Restart after burner failure
1.
Set thermostat lower than the room temperature;
2.
Press the reset button on the burner primary control (relay);
3.
Set thermostat higher than the room temperature;
4. If the burner motor does not start or ignition fails, turn off the
disconnect switch and CALL A QUALIFIED SERVICE
TECHNICIAN.
CAUTION
Do not attempt to start the burner when excess oil has
accumulated, when the furnace is full of vapour, or
when the combustion chamber is very hot.
2.2.3) BVSO
Performance
Test
The purpose of the following test is to check that the electrical outlet
on the furnace, designated to the BVSO, is functional.
1.
Start up the burner;
2. Remove the three-pole plug from the BVSO outlet on the
furnace;
3.
The burner must shut-off immediately, while the blower continues
to run to the end of the cool-down cycle.
If the test is not in line with the above,
CALL A QUALIFIED SERVICE
TECHNICIAN.
2.2.4) Combustion
chamber
curing
Some moisture and binders remain in the ceramic combustion
chamber after manufacture. It is important to clear the chamber of this
residue before testing. If you smoke test before curing, the instrument
may become damaged. To cure the chamber, run the unit for 3
consecutive cycles, with 3 minutes of elapsed time in between each
cycle. Each burn cycle should least 3 minutes. The exhaust will have a
pungent odour and produce a white cloud of steam.
2.2.5) Smoke / CO
2
test
1. Pierce a test hole in the smoke pipe near the furnace breech.
Insert the smoke test instrument probe into the open hole;
2. Starting with a zero smoke reading, gradually reduce the burner
air setting until just a trace of smoke results (#1 on Bacharach
Scale);
3. Take a CO
2
sample at the same test location where the smoke
sample was taken. Note the CO
2
reading associated with the #1
smoke condition;
4. Adjust the burner air setting to obtain a CO
2
reading 1% lower
than the reading associated with the #1 smoke;
5. This method of adjusting the CO
2
will allow adequate excess air
to ensure that the burner will burn clean for the entire heating
season.
2.2.6) Supply air temperature rise test
1.
Operate the burner for at least 10 minutes;
2.
Measure the air temperature in the return air plenum;
3. Measure the air temperature in the largest trunk coming off the
supply air plenum, just outside the range of radiant heat coming
off the heat exchanger; 0.3 m (12") from the plenum on the main
take-off usually sufficient;
4. The temperature rise is calculated by subtracting the return air
temperature from the supply air temperature;
5. If the temperature rise exceeds the temperature specified in
Tables 3.1 to 3.4, p. 15 to 18, change to the next higher blower
speed tap until the temperature rise falls to this temperature or
below. If the excessive temperature rise cannot be reduced by
increasing fan speed, investigate for ductwork restriction(s), dirty
or improper air filter, overfiring caused by excessive pump
pressure, or improper nozzle sizing.
445 01 4054 06
Summary of Contents for FLO115DABR-C
Page 21: ...22 PARTS LIST Model MBO115DABR D B50040B 445 01 4054 06...
Page 23: ...PARTS LIST Model MBOV115DABR D B50041B 445 01 4054 06...
Page 25: ...26 PARTS LIST Model LBO125DABR13 D B50038C 445 01 4054 06...
Page 27: ...PARTS LIST Models LBO145DABR34 D OLR182A16C B50039F 445 01 4054 06...
Page 29: ...PARTS LIST Model FLO115DABR C OLF140C12C B50042A 445 01 4054 06...