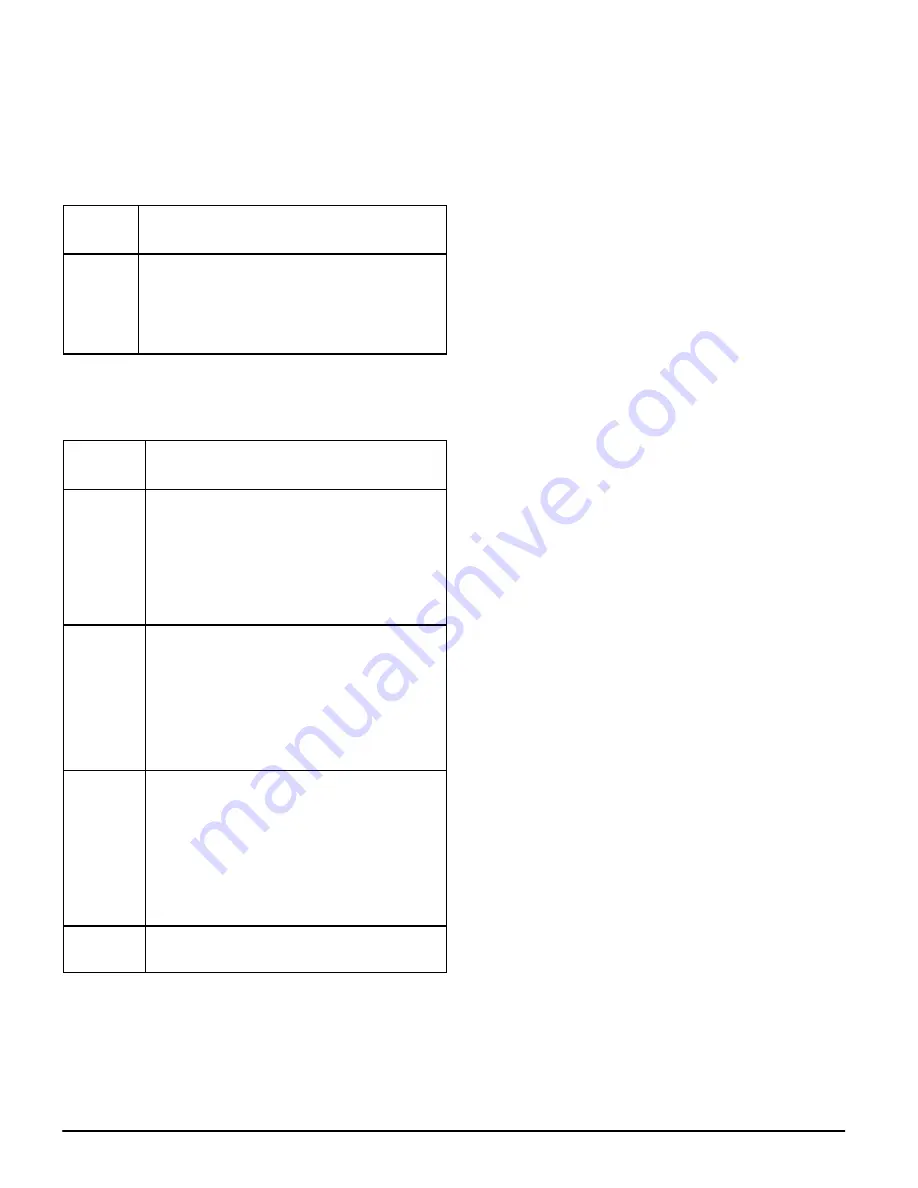
441 01 2314 06
Specifications are subject to change without notice.
13
Exterior Masonry Chimney,
FAN+NAT Installations with
Type
−
B Double
−
Wall Vent Connectors
NFPA & AGA
Table A-
Combined Appliance
Maximum Input Rating in
Thousands of Btu per Hr
VENT
HEIGHT
FT(m)
INTERNAL AREA OF CHIMNEY
SQ IN.(mm)
12(77.4)
19(122.6)
28(180.6)
38(245.2)
6(1.8)
74
119
178
257
8(2.4)
80
130
193
279
10(3)
84
138
207
299
15(4.6)
NR
152
233
334
20(6.1)
NR
NR
250
368
30(9.1)
NR
NR
NR
404
Table B-
Minimum Allowable Input Rating of
Space-Heating Appliance in
Thousands of Btu per Hr
VENT
HEIGHT
FT(m)
INTERNAL AREA OF CHIMNEY
sq. in(mm)
12(77.4)
19(122.6)
28(180.6)
38(245.2)
17 to 26
F (
−
8 to
−
3
C)
Local 99% Winter Design Temperature:
17 to 26
°
F (
−
8 to
−
3
°
C)*
6(1.8)
0
55
99
141
8(2.4)
52
74
111
154
10(3)
NR
90
125
169
15(4.6)
NR
NR
167
212
20(6.11)
NR
NR
212
258
30(9.1)
NR
NR
NR
362
5 t o 16
F (
−
15 to
−
9
C)
Local 99% Winter Design Temperature:
5 to 16
°
F (
−
15 to
−
9
°
C)*
6(1.8)
NR
78
121
166
8(2.4)
NR
94
135
182
10(3)
NR
111
149
198
15(4.6)
NR
NR
193
247
20(6.11)
NR
NR
NR
293
30(9.1)
NR
NR
NR
377
−
10 to 4
F (
−
23 to
−
16
C)
Local 99% Winter Design Temperature:
−
10 to 4
°
F (
−
23 to
−
16
°
C)*
6(1.8)
NR
NR
145
196
8(2.4)
NR
NR
159
213
10(3)
NR
NR
175
231
15(4.6)
NR
NR
NR
283
20(6.11)
NR
NR
NR
333
30(9.1)
NR
NR
NR
NR
−
11
°
F
(
−
24
°
C)
or lower
Local 99% Winter Design Temperature:
−
11
°
F (
−
24
°
C) or lower*
Not recommended for any vent configuration
* The 99% Winter Design Dry
−
Bulb (db) temperatures are
found in the 2005 ASHRAE Fundamentals Handbook CD
and Chapter 28.
Inspections before the sale and at the time of installation will deter-
mine the acceptability of the chimney or the need for repair and/or
(re)lining. Refer to the Chimney Inspection Chart to perform a
chimney inspection.
If the inspection of a previously used tile
−
lined chimney:
a. Shows
signs of vent gas condensation, the chimney should
be relined in accordance with local codes and the authority
having jurisdiction. The chimney should be relined with a
listed metal liner or Type
−
B vent to reduce condensation. If
a condensate drain is required by local code, refer to the
NFGC, Section 12.10 for additional information on conden-
sate drains.
b. Indicates the chimney exceeds the maximum permissible
size in the tables, the chimney should be rebuilt or relined to
conform to the requirements of the equipment being
installed and the authority having jurisdiction.
A chimney without a clay tile liner, which is otherwise in good con-
dition, shall be rebuilt to conform to ANSI/NFPA 211 or be lined with
a UL listed (ULC listed in Canada) metal liner or UL listed Type
−
B
vent. Relining with a listed metal liner or Type
−
B vent is consid-
ered to be a vent
−
in
−
a
−
chase.
If a metal liner or Type
−
B vent is used to line a chimney, no other
appliance shall be vented into the annular space between the
chimney and the metal liner.
APPLIANCE APPLICATION REQUIREMENTS
Appliance operation has a significant impact on the performance
of the venting system. If the appliances are sized, installed, ad-
justed, and operated properly, the venting system and/or the ap-
pliances should not suffer from condensation and corrosion. The
venting system and all appliances shall be installed in accordance
with applicable listings, standards, and codes.
The furnace should be sized to provide 100 percent of the design
heating load requirement plus any margin that occurs because of
furnace model size capacity increments. Heating load estimates
can be made using approved methods available from Air Condi-
tioning Contractors of America (Manual J); American Society of
Heating, Refrigerating, and Air
−
Conditioning Engineers; or other
approved engineering methods. Excessive oversizing of the fur-
nace could cause the furnace and/or vent to fail prematurely.
When a metal vent or metal liner is used, the vent or liner must be in
good condition and be installed in accordance with the vent or liner
manufacturer’s instructions.
To prevent condensation in the furnace and vent system, the fol-
lowing precautions must be observed:
1. The
return
−
air temperature must be at least 60
°
F(16
°
C) db
except for brief periods of time during warm
−
up from set-
back at no lower than 55
°
F(13
°
C) db or during initial start
−
up from a standby condition.
2. Adjust the gas input rate per the installation instructions.
Low gas input rate causes low vent gas temperatures, caus-
ing condensation and corrosion in the furnace and/or vent-
ing system. Derating is permitted only for altitudes above
2000
′
(610m).
3. Adjust the air temperature rise to the midpoint of the rise
range or slightly above. Low air temperature rise can cause
low vent gas temperature and potential for condensation
problems.
4. Set the thermostat heat anticipator or cycle rate to reduce
short cycling.
Air for combustion must not be contaminated by halogen com-
pounds which include chlorides, fluorides, bromides, and iodides.
These compounds are found in many common home products
such as detergent, paint, glue, aerosol spray, bleach, cleaning sol-
vent, salt, and air freshener, and can cause corrosion of furnaces
and vents. Avoid using such products in the combustion
−
air sup-
ply. Furnace use during construction of the building could cause
the furnace to be exposed to halogen compounds, causing prema-
ture failure of the furnace or venting system due to corrosion.
Vent dampers on any appliance connected to the common vent
can cause condensation and corrosion in the venting system. Do
not use vent dampers on appliances common vented with this fur-
nace.