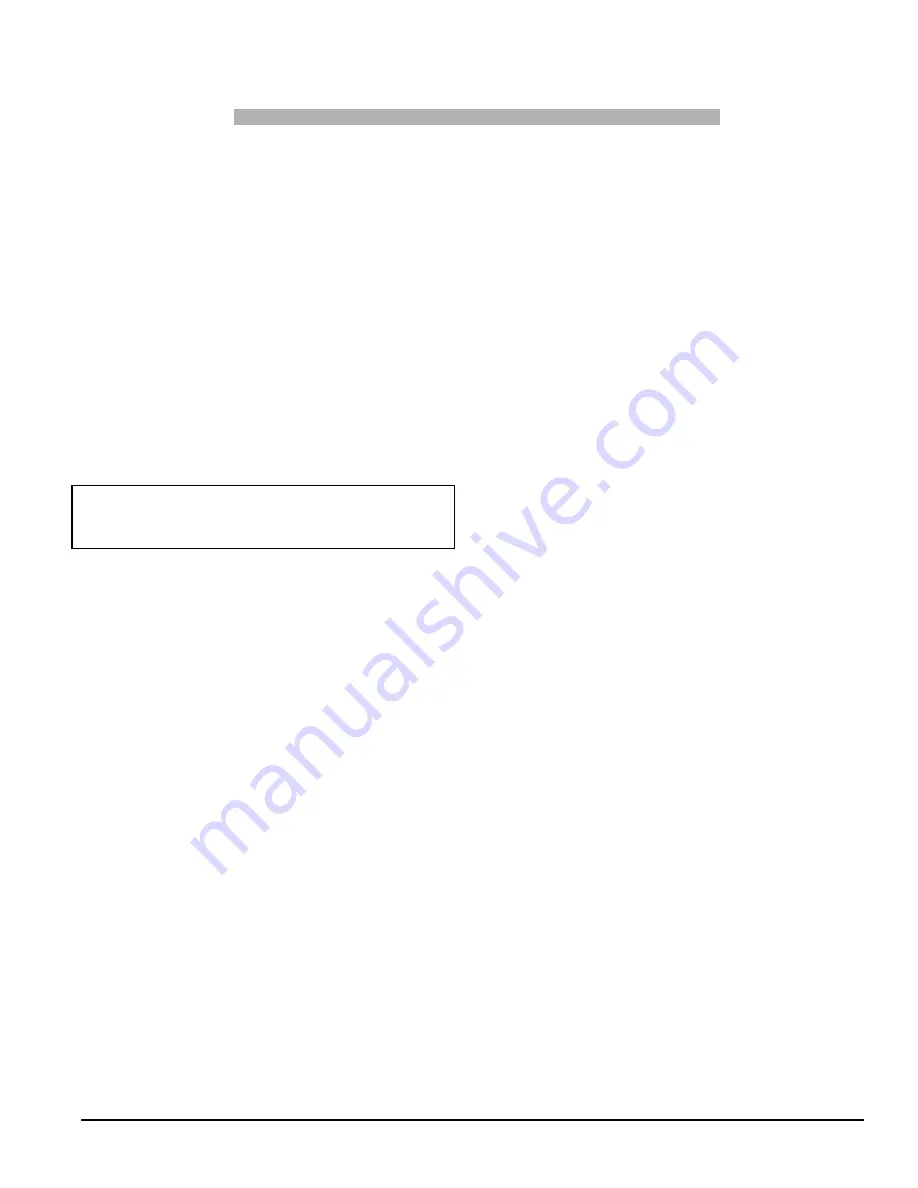
11
PART 2
START-UP
2.1) OPERATIONAL
CHECKLIST
1=>
Has the blower wheel support been removed?
2=>
Has the electrical wiring been completed
according to Figures 12.1 to 12.8?
3=>
Has the access blower door been secured in
place?
4=>
Is the valve on the oil line open?
5=>
Has the ‘’RESET BUTTON’’ on the Primary
Control been pushed?
6=>
Is the flame observation door and the two clean-
out access doors located at the front of the unit
closed?
7=>
Is the room thermostat in the heating mode and
set above room temperature?
8=>
Set the main electrical switch to the ‘’ON’’
position and the burner should start
.
CAUTION
Do not tamper with the unit or its controls. Call a
qualified service technician.
2.2) COMBUSTION
CHECK
In order to obtain optimum performance from the oil burner,
the following set-up procedures must be followed by referring
to the Technical Specifications (Table 3) in this manual:
1. A test kit to measure the smoke, flue draft and over-fire
draft should be used in order to obtain the proper air
band setting. Although all of the above measurements
are required for optimum set up and efficiency, the most
important reading that must be taken is the smoke
number in the flue pipe or at the smoke test port on the
breech plate (SCS);
2. The proper smoke number, as established by way of
engineering tests, is between 0 and 1. This degree of
smoke emission is commonly referred to as a “trace”. It
is recommended that a Bacharach True Spot Smoke
Test kit or equivalent be used;
3. On chimney installations only, a barometric draft
regulator (supplied with the furnace) must be installed as
closely to the breech of the furnace as possible, in order
to ensure proper draft through the furnace. The
barometric damper must be mounted with the hinge pins
in a horizontal position and the face of the damper
vertical for proper functioning, (see instructions included
with damper). After the furnace has been firing for at
least five minutes, the draft regulator should be set to
between -0.025
"
W.C. and -0.035
"
W.C.;
4. For flue pipe pressure on sidewall installations (SCS),
refer to the Technical Specifications in this manual;
5. The overfire draft, which is taken through the
observation door located in the centre of the front panel
above the burner, is a measurement that is necessary to
determine if there is a blockage in the heat exchanger or
the flue pipe. Refer to the Technical Specifications in
this manual for overfire pressure values. A high
pressure condition may be caused by excessive
combustion air due to the air band being too wide open
or a lack of flue draft (chimney effect) or some other
blockage, such as soot in the secondary section of the
heat exchanger or the use of an oversize nozzle input or
high pressure pump;
6. CO
2
and flue temperature instruments will enable you to
obtain the data that are required to determine the true
efficiency of the furnace. Although this information is
nice to have, it is not essential in the basic set up of the
furnace. The proper procedure for performing this
operation is as follows:
a. Start the appliance and from the test port provided
on the BREECH PLATE (SCS) or on the flue pipe
just before the draft regulator (chimney application),
proceed with the smoke test and adjust the burner
to a setting of between a “trace” and #1 smoke after
5 to 10 minutes of operation;
b. Take a CO
2
reading and mark it down;
c. Open the burner air shutter to get 1.5% CO
2
less
than the previous reading noted in b. above and
take a smoke test on this condition;
d. The new smoke reading should give you a ZERO
smoke reading.
7. A 10-micron (or less) oil filter should be installed as
closely to the burner as possible with all oil burners, but
it is essential for burners with a low firing rate. We
recommend the use of a low pressure drop oil filter with
a capacity greater than that of the fuel pump;
8. On a new installation, the air trapped in the oil line
leading from the tank to the nozzle must be thoroughly
purged in order to prevent excessive after drip. The oil
pump is equipped with a special fitting that facilitates the
purging of any air between it and the tank. The proper
procedure for performing this operation is as follows:
a. Place a piece of 1/4” dia. clear plastic tubing over
the purge fitting on the oil pump;
b. Start the oil burner, then open the purge fitting and
allow the burner to run until the purge tube is
completely free of air bubbles;
c.
At this point tighten the purge fitting, which will allow
the oil to run to the nozzle and fire the burner. If the
purging takes longer than 15 seconds and no flame
has been established the burner will stop. Push the
reset button on top of the Primary Control to restart
the burner.
For detailed information on the operation of the Primary
Control refer to the instructions included with the furnace
or the burner.
Summary of Contents for AMP105-IE2
Page 20: ...FIGURE 12 1 Diagramme lectrique AMP LBM BMF 075 090 et 105 br leur Beckett 21...
Page 21: ...FIGURE 12 2 Diagramme lectrique AMP LBM BMF 120 140 et 155 br leur Beckett 22...
Page 22: ...FIGURE 12 3 Diagramme lectrique AMP LBM BMF 075 090 et 105 br leur Riello 23...
Page 23: ...FIGURE 12 4 Diagramme lectrique AMP LBM BMF 120 140 et 155 br leur Riello 24...
Page 26: ...FIGURE 12 7 Diagramme lectrique AMP LBM BMF 075 090 et 105 br leur B SCS 27...
Page 27: ...FIGURE 12 8 Diagramme lectrique AMP LBM BMF 120 140 et 155 br leur B SCS 28...
Page 28: ...29 COMPOSANTES ET PI CES DE REMPLACEMENT...
Page 29: ...LISTE DE PI CES Code de fabrication AMP LBM BMF 075 090 105 30 B50058A...
Page 31: ...LISTE DE PI CES Code de fabrication AMP LBM BMF 120 140 155 32 50062A...
Page 51: ...19 FIGURE 12 1 Wiring diagram AMP LBM BMF 075 090 105 Beckett burner...
Page 52: ...20 FIGURE 12 2 Wiring diagram AMP LBM BMF 120 140 155 Beckett burner...
Page 53: ...21 FIGURE 12 3 Wiring diagram AMP LBM BMF 075 090 105 Riello burner...
Page 54: ...22 FIGURE 12 4 Wiring diagram AMP LBM BMF 120 140 155 Riello burner...
Page 57: ...FIGURE 12 7 Wiring diagram AMP LBM BMF 075 090 105 B SCS burner 25...
Page 58: ...FIGURE 12 8 Wiring diagram AMP LBM BMF 120 140 155 B SCS burner 26...
Page 59: ...27 COMPONENTS AND REPLACEMENT PARTS...
Page 60: ...PARTS LIST Model AMP LBM BMF 075 090 105 28 B50058A...
Page 62: ...PARTS LIST Model AMP LBM BMF 120 140 155 30 B50062A...