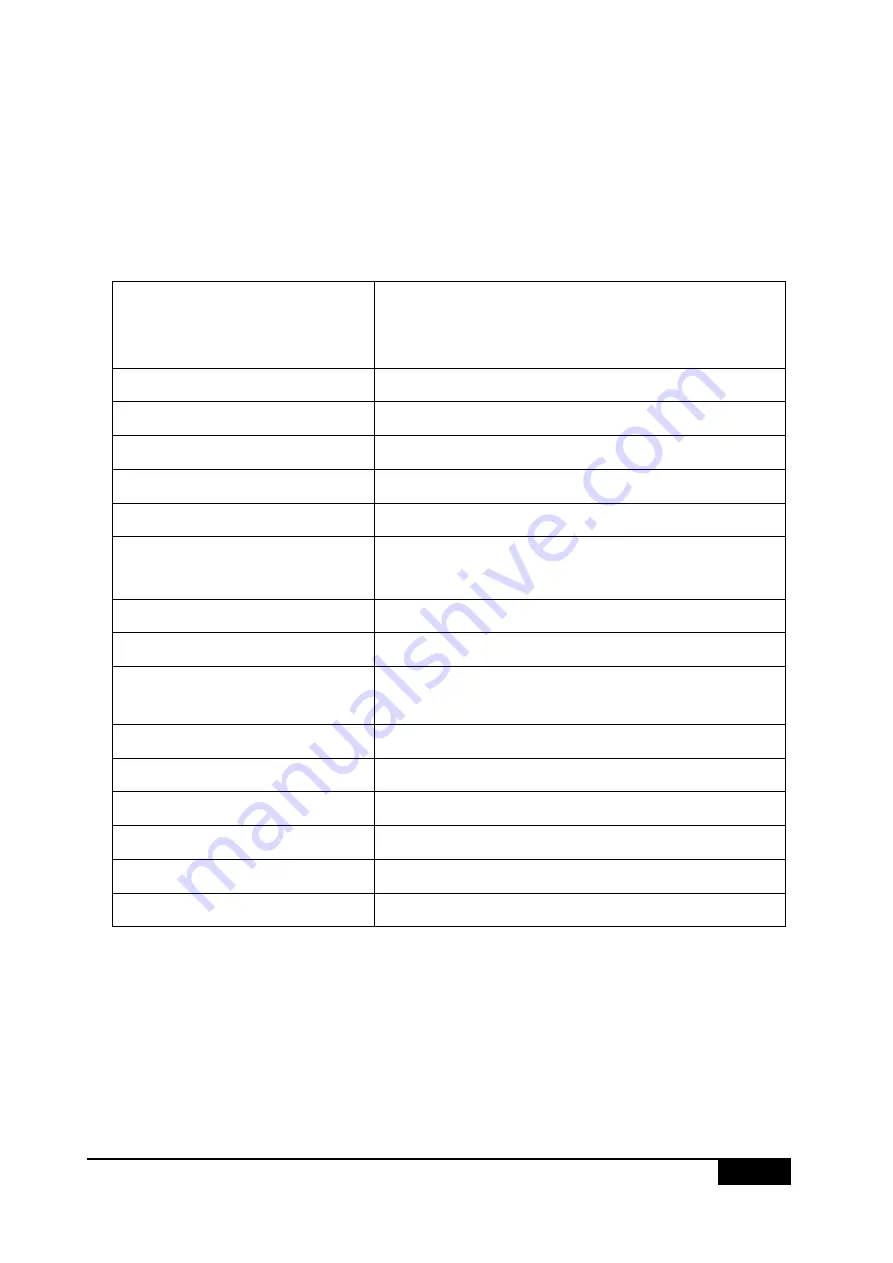
I-8014W API User Manual, v 1.0.1, September 2011 E-mail: [email protected]
Copyright © 2011 ICP DAS Co., Ltd. All Rights Reserved.
6
Hardware
Specifications
Input Range
+/- 10 V, +/- 5 V, +/- 2.5 V, +/- 1.25 V
-20 mA ~ +20 mA (Requires Optional External
125 Ohm Resistor)
Resolution
16 bits
Sampling Rate
Single Channel, Polling Mode :250K S/s
FIFO
4k sample (8 k bytes)
Accuracy
0.05 % of FSR +/- 1 LSB
Input Mode
Polling, Pacer (Magic Scan)
Magic Scan Mode
Mode1: standard mode
Mode2: virtual sample and hold
Overvoltage Protection
+60 V ~ -45 V
Input Impedance
20 k, 200 k, 20 M (Jumper Select)
Intra-module Isolation, Field
to Logic
2500 Vrms
LED Power Indicator
Yes
Power Consumption
2.5 W Max
Operating Temperature
-25 ~ +75 °C
Storage Temperature
-30 ~ +85 °C
Humidity
5 to 95 % RH, Non-condensing
Dimensions (W x L x H)
30 mm x 102 mm x 115 mm