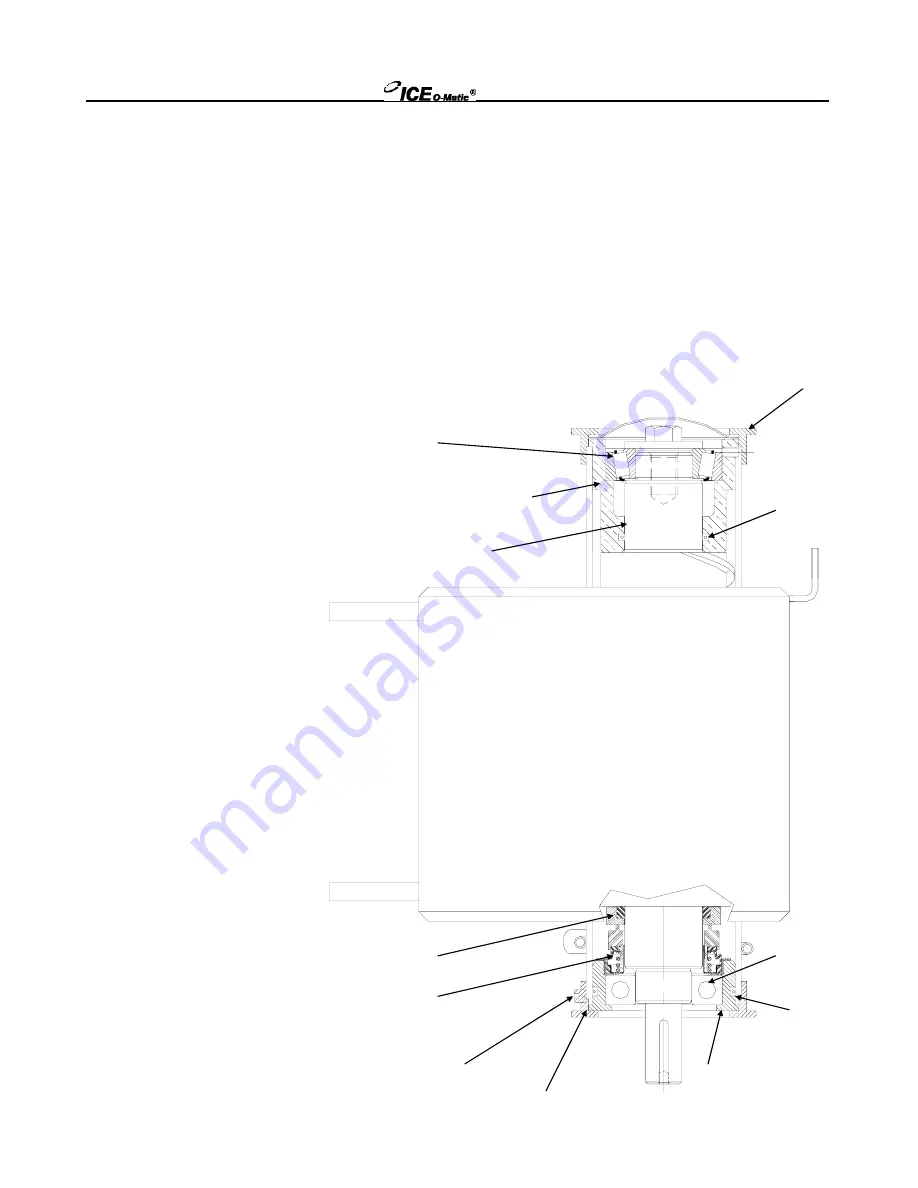
Flake Ice Machines
Drive System
Page
E4
Remove the upper evaporator retaining nut by using a chain wrench (wrap chain around the
upper part of the nut) to loosen the nut.
Setscrews are not used on the upper nut
. (Right
Hand Thread)
Caution: Do not use a hammer and chisel to loosen the nut, as damage will result.
Remove the auger and upper bearing housing assembly by tapping upward on the auger
shaft with a rubber mallet, or place a block of hardwood against the auger shaft and tap
upwards on the block with a hammer. Remove the upper bearing housing from the auger by
removing the mounting bolt and washer.
Caution: Do not hit the auger shaft with a metal hammer, as damage to the auger shaft
will result.
Upper Nut
Right Hand Thread
Remove the seal face from the auger by prying it off with a screwdriver.
Remove the lower
evaporator retaining nut
by first using an 1/8 inch
Allen wrench to remove
the two (2) ¼ inch set
screws
from the lower
nut. Remove the lower
evaporator retaining nut
by using a chain wrench
(wrap chain around the
lower part of the nut) to
loosen the nut. (Right
Hand Thread)
Caution: If the two (2)
sets screws are not
removed, damage to
the evaporator threads
will result.
Remove the lower
bearing housing
assembly from the
evaporator barrel by
placing a dowel,
approximately 18 inches
long, against the lower
bearing and tapping
lightly on the dowel until
the bearing housing is
removed from the
evaporator.
Remove 2 setscrews
Upper Housing Assembly
O-Ring
O-Ring
Bearing
Auger
Seal Face
Lower Seal
Lower Nut
Right Hand Thread
Bearing
Lower Housing Assembly
Summary of Contents for EF Series
Page 2: ......
Page 6: ......
Page 9: ...Flake Ice Machines General Information Page A7 EF Series ...
Page 10: ...Flake Ice Machines General Information Page A8 EMF Series ...
Page 11: ...Flake Ice Machines General Information Page A9 EMF Series 48 Inch Wide ...
Page 20: ...Flake Ice Machines Troubleshooting Trees Page C2 Machine Runs Does Not Make Ice ...
Page 21: ...Flake Ice Machines Troubleshooting Trees Page C3 Machine Runs Does Not Make Ice ...
Page 22: ...Flake Ice Machines Troubleshooting Trees Page C4 Machine Does Not Run ...
Page 23: ...Flake Ice Machines Troubleshooting Trees Page C5 Slow Production ...
Page 24: ...Flake Ice Machines Troubleshooting Trees Page C6 Low Production ...
Page 25: ...Flake Ice Machines Troubleshooting Trees Page C7 High Suction Pressure ...
Page 26: ...Flake Ice Machines Troubleshooting Trees Page C8 Machine Freezes Up Auger Seizes ...
Page 27: ...Flake Ice Machines Troubleshooting Trees Page C9 Auger Motor Amp Draw Fluctuates ...
Page 28: ...Flake Ice Machines Troubleshooting Trees Page C10 Water Leaking From Bottom of Evaporator ...
Page 29: ...Flake Ice Machines Troubleshooting Trees Page C11 Machine Produces Wet Ice ...
Page 31: ...Flake Ice Machines Troubleshooting Trees Page C13 Noise Coming from Evaporator ...
Page 41: ...Flake Ice Machines Drive System Page E8 Exploded View of the Evaporator ...
Page 43: ......
Page 46: ......
Page 61: ...Flake Ice Machines Electrical System Page G6 9071694 01 EF250 255 405 EF450A W ...
Page 62: ...Flake Ice Machines Electrical System Page G7 9071963 01 EF800A W ...
Page 63: ...Flake Ice Machines Electrical System Page G8 EMF450 405A W 9071958 01 ...
Page 64: ...Flake Ice Machines Electrical System G9 Page 9071954 01 EMF800A W ...
Page 65: ...Flake Ice Machines Electrical System Page G10 9071956 01 EMF705 1005 1006A W ...
Page 66: ...Flake Ice Machines Electrical System Page G11 9071962 01 EMF1106R ...
Page 67: ...Flake Ice Machines Electrical System Page G12 9071955 01 EMF2306A W ...
Page 68: ...Flake Ice Machines Electrical System Page G13 9071960 01 EMF2306R ...
Page 69: ...Flake Ice Machines Electrical System Page G14 9071959 01 EMF2305L ...
Page 70: ......
Page 71: ......
Page 72: ......