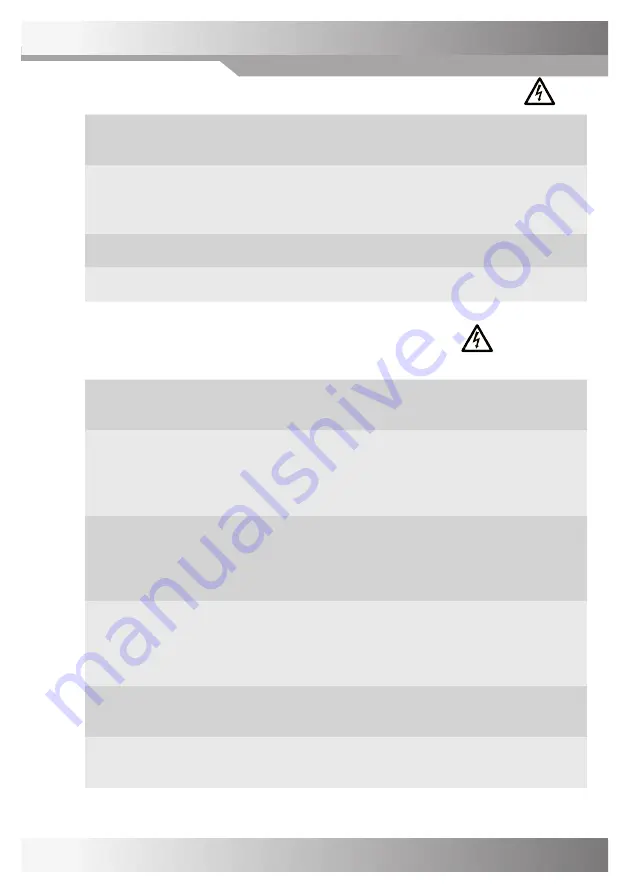
Check that
the control unit is connected as per instructions on page 10.
Connection voltage 230-240 V +/-15%, 50/60 Hz.
Check that
the motor is wired for 3x230 V. If there is an operating switch between the
motor and the control unit, the motor thermal contact should be
connected via the auxiliary terminal in the operating switch.
Check that
the input signal is 0-10 V
.
Check that
the cleaning function and rotation monitor DIP switch are set to ON.
PUTTING THE EQUIPMENT INTO OPERATION
Should be done in sequence.
Check that
the motor rotates in the right direction in relation to the rotor's direction
of rotation. In the event of a fault, switch two phases to the motor.
Adjustment of
maximum rpm
Set the “High Speed” DIP switch to the ON position.
Adjust "Max. rpm" so that the rotor rotates at 10-12 rpm
(or as per directions from rotor manufacturer).
After a test run, set the DIP switch to OFF.
Checking
minimum rpm
Set the “Low Speed” DIP switch to ON.
Check that the rotor starts.
The minimum rpm is preset.
After a test run, set the DIP switch to OFF.
Checking the
cleaning function
Switch off the voltage.
Make sure the “Cleaning function” DIP switch is set to ON and the input
signal is disconnected. When power is switched on, the rotor will rotate at
minimum rpm for 10 seconds.
Checking the
rotation monitor
The yellow “Rotation” LED will flash when the magnet passes the
magnetic sensor, regardless of DIP switch position.
Finish by
having the control unit drive the rotor at maximum and minimum
rpm and checking that the rotor speed is correct.
CHECKS BEFORE POWERING UP THE CONTROL UNIT
11
Summary of Contents for MicroMax750
Page 2: ......
Page 15: ...PERSONAL NOTES 13...