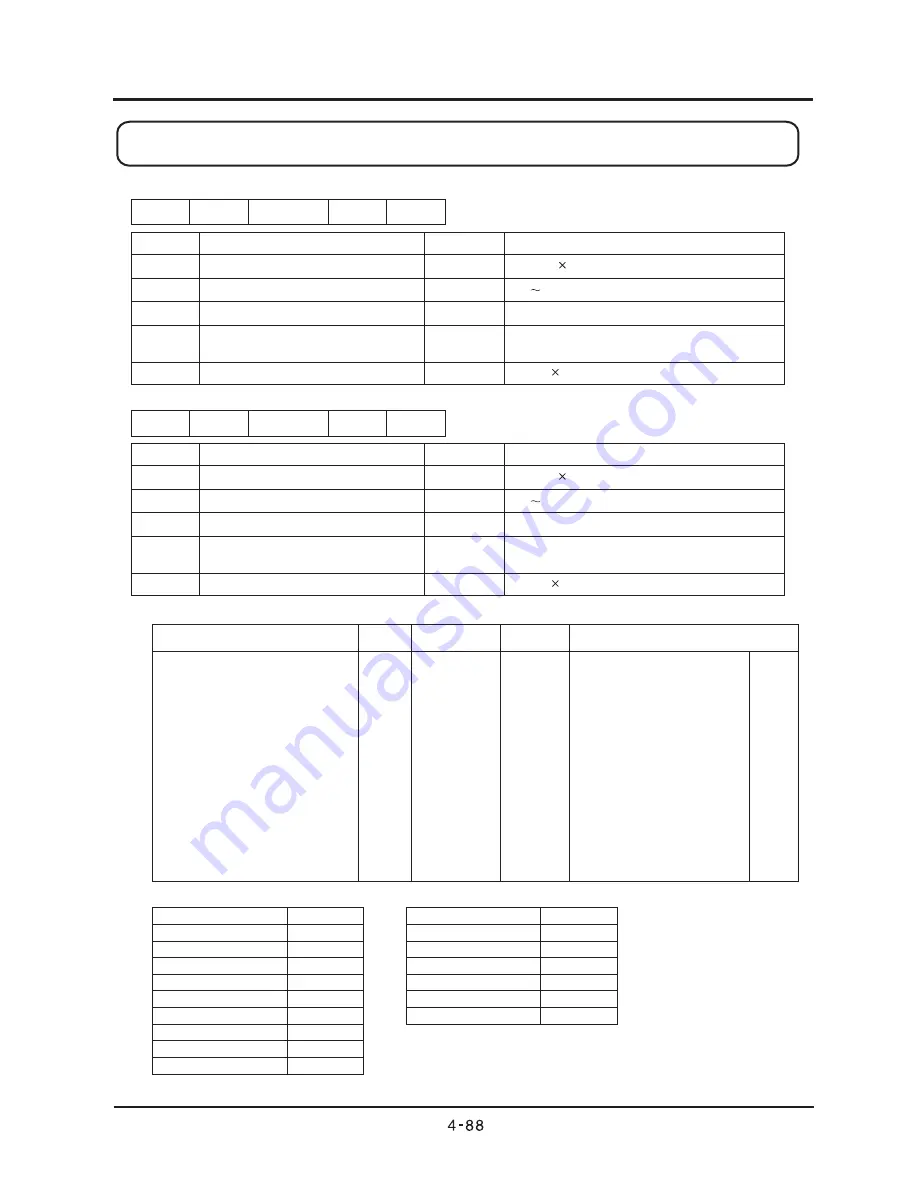
STX
Code
Code
Command
BCC
CR
Explanation
Data size
Value
STX
Command
BCC
CR
Control code(Start of Text)
Station number of inverter
Transmission command
Block check code
Control code(Carriage Return)
1 byte
2 byte
2 byte
1 byte
STX (0 02)
01
32
03
Exclusive OR of Code, Command and Data
(5) Reference
CR (0 0D)
2 byte
Frame format
Frame format
STX
Code
Code
Data
BCC
CR
Explanation
Data size
Value
STX
Data
BCC
CR
Control code(Start of Text)
Station number of inverter
Each monitor data on trip
Block check code
Control code(Carriage Return)
1 byte
2 byte
2 byte
1 byte
STX (0 02)
01
32
(Note 4) reference
Exclusive OR of Code, Command and Data
(5) Reference
CR (0 0D)
104 byte
Monitor item
Output frequency
Output current
Revolution direction
PID feedback monitor
Intelligent input monitor
Intelligent output monitor
Frequency converting monitor
Output torque monitor
Output voltage monitor
Electric power monitor
-
RUN time monitor
ON time monitor
Units
Hz
A
-
%
-
-
-
%
V
kW
-
h
h
x100
x10
-
x100
-
-
x100
x1
x10
x10
-
x1
x1
Competitive rate Data size
8byte
8byte
8byte
8byte
8byte
8byte
8byte
8byte
8byte
8byte
8byte
8byte
8byte
Note
Upper
bite-----------------lower
bite
Tenth ASCII code
Tenth ASCII code
0: stop, 1:forward, 2:backward
Tenth ASCII code
Tenth ASCII code
Tenth ASCII code
(00000000) padding data
Tenth ASCII code
Tenth ASCII code
Note 7 reference
*5) reference
*6) reference
Tenth ASCII code
(Note 4) Each monitor value
(Note 5) Intelligent input terminal monitor
(Note 6) Intelligent output terminal monitor
Item
FW(Forward terminal)
1 (1 terminal)
st
2 (2 terminal)
nd
3 (3 terminal)
rd
4 (4 terminal)
th
5 (5 terminal)
th
6 (6 terminal)
th
7 (7 terminal)
th
8 (8 terminal)
th
Data
00000001
00000002
00000004
00000008
00000010
00000020
00000040
00000080
000000100
Item
AL(Alarm terminal)
11 (1 terminal)
st
12 (2 terminal)
nd
13 (3 terminal)
rd
14 (4 terminal)
th
15 (5 terminal)
th
Data
00000001
00000002
00000004
00000008
00000010
00000020
(v) 04 command : This reads the state of the inverter.
N300 INSTRUCTION MANUAL
Chapter 4 Explanation of function
Summary of Contents for hiRUN N300-055H
Page 163: ...N300 150 220LF HF N300 300LF HF N300 INSTRUCTION MANUAL Chapter 6 Specification ...
Page 164: ...N300 370 450LF HF N300 550HF N300 550LF N300 INSTRUCTION MANUAL Chapter 6 Specification ...
Page 165: ...N300 750 900HF N300 1100HF 1320HF N300 INSTRUCTION MANUAL Chapter 6 Specification ...