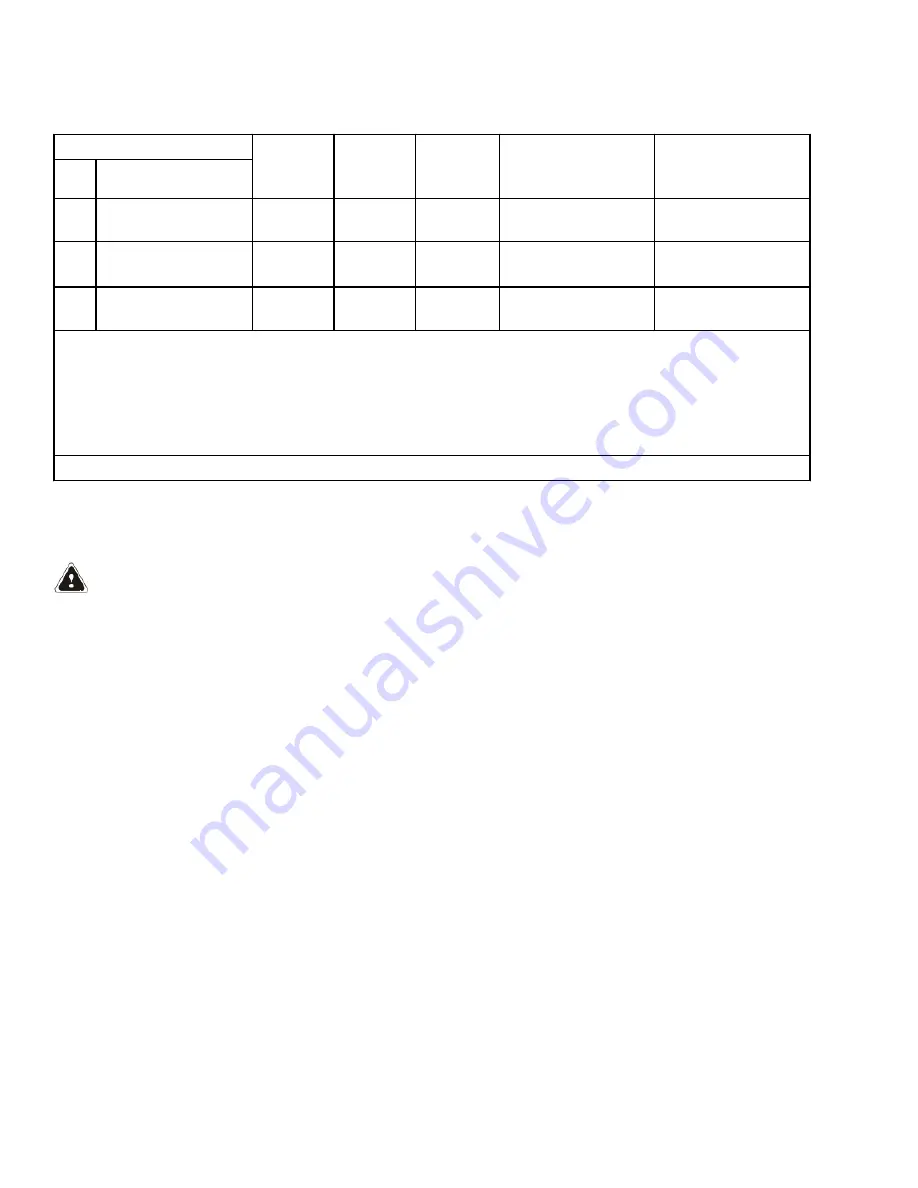
Table 1. Maintenance Schedule (Continued)
Item
8 hr
or 1 day
1
350 hr
or 2
month
1
2000 hr
or 1 year
1
Procedure or
Quantity
Specification
No.
Description
13
Base Arm Capscrews
X
Tighten if Required
Torque to
300 N•m (221 lbf ft)
14
Steering Bearing
L
1 Lube Fitting
Multipurpose
Grease
3
15
Drive Unit Gear Oil
X
C
0.18 liter (6 oz)
SAE 80W-90 Gear
Oil
1
Whichever comes first.
2
Equalization Charge approximately each month but not more than each week.
3
Use Mobilgrease
®
28 synthetic extra-protection grease for standard, freezer, and cold storage
configurations.
4
Use ISO VG 46 antiwear (HCE-140) for standard configurations. Use Exxon Univis
®
HVI 26 (synthetic) for
cold storage and freezer configurations.
X=Check C=Change L=Lubricate A=Adjust
Maintenance Procedures Every 8 Hours or Daily
WARNING
DO NOT operate a lift truck that needs repairs. If a
repair is necessary, put a DO NOT OPERATE tag
in the operator's area. Remove the key from the
key switch.
Disconnect the battery connector before remov-
ing the MDU cover. Personal injury or equipment
and tool damage can occur if the battery is not
disconnected.
The capacitor in the traction motor controller can
hold an electrical charge after the battery is dis-
connected. To prevent electrical shock and injury,
discharge the capacitor before inspecting or re-
pairing any component. See Special Precautions.
Inspect the lift truck every 8 hours or daily before
use. Put the lift truck on a level surface. Lower the
carriage and forks, and turn the key switch to the
OFF position.
CHECKS BEFORE OPERATION
Make the following checks:
• Safety labels in place and legible
• Battery electrolyte level
• Make sure the battery is clean and is the cor-
rect size and weight for the lift truck
• Condition of the wheels and tires
• Condition of the forks, carriage, and mast
• Oil level in the hydraulic reservoir
• Leaks in the hydraulic system
If repair is required, DO NOT operate a lift truck
until the problems are corrected.
Maintenance Procedures Every 8 Hours or Daily
8000 SRM 1379
12