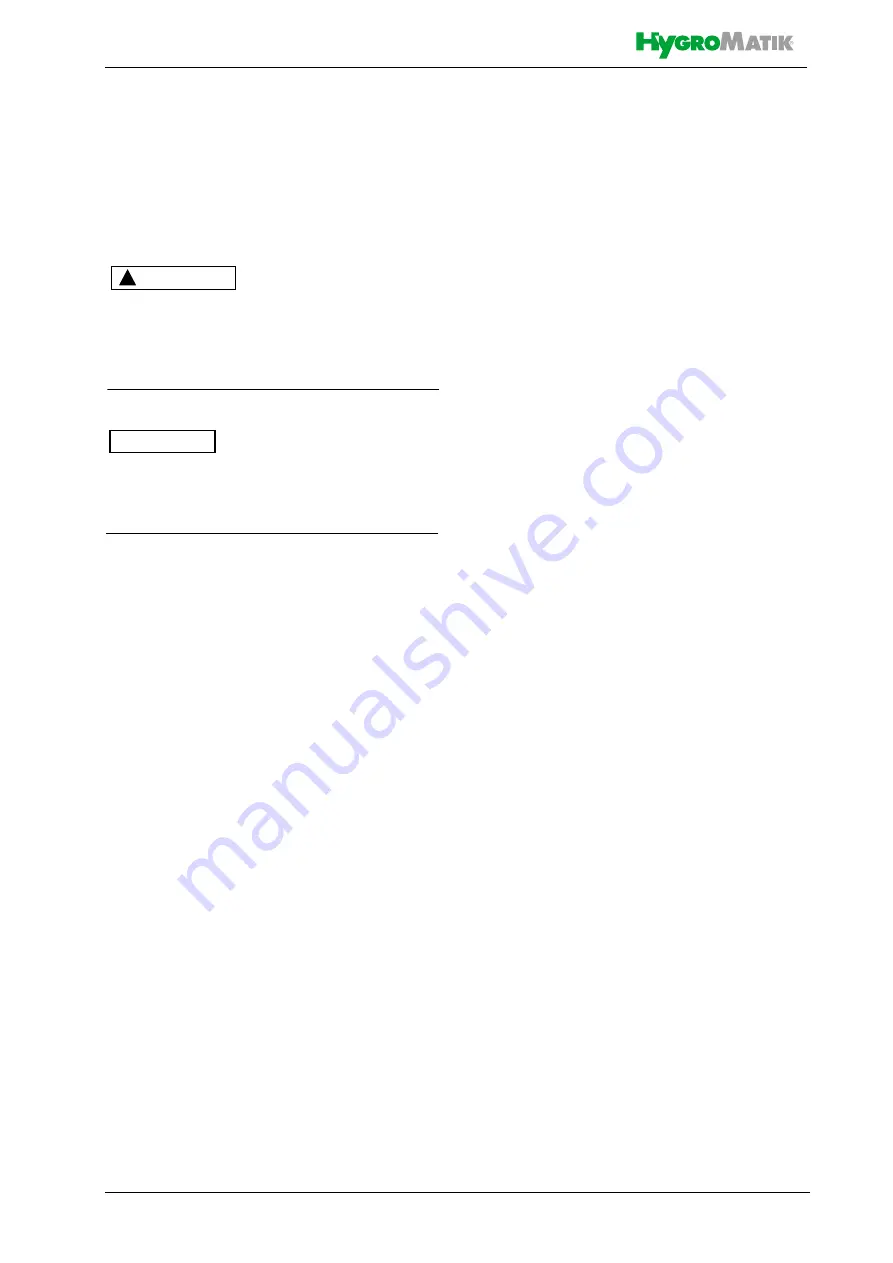
Page 45
10.
Dismantling
Once the steam humidifier will no longer be
used, dismantle (demolish or scrap) it by fol-
lowing the installation procedures in reverse
order.
Warning:
Dismantling of the unit may only be
performed by qualified personnel. Electrical
dismantling may only be performed by
trained electricians.
Obey the safety guidelines in section “Safety
Instructions,” especially the guidelines for
disposal.
:$51,1*
3OHDVHQRWH