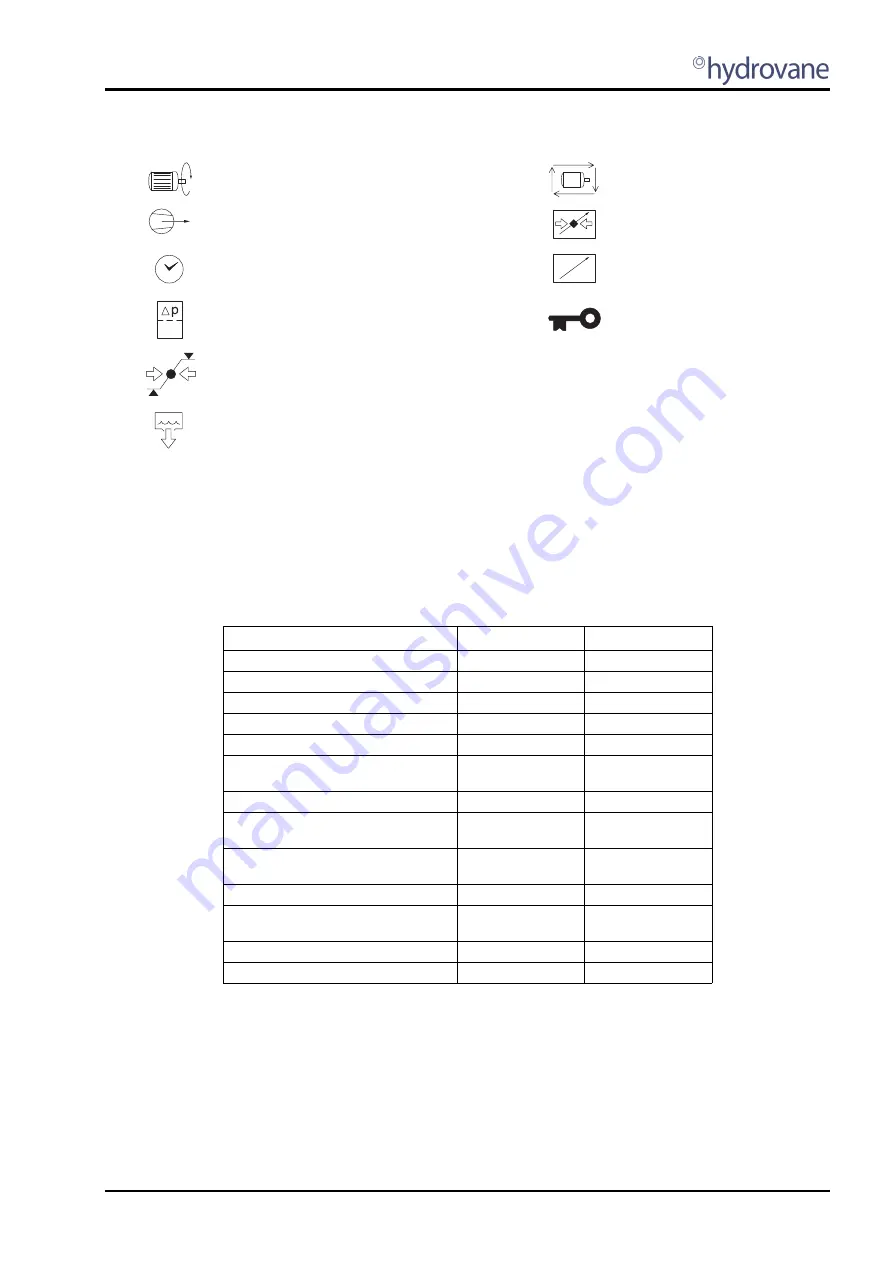
ST16135-00E
19
7
Operating Instructions
7.2
Operational Display Symbols
7.3
LED Indicators (Fig 7.2)
STATUS:
Green
°
FAULT
Red
l
The indicator states are shown in Table 7.1.
Table 7.1 - Compressor Status and LED Indicators
Key:
ON
Illuminated continuously
FF
Fast flash: on/off four times per second
SF
Slow flash: on/off once per second
IF
Intermittent flash: on/off every four seconds
OFF
Extinguished continuously
*
SF for alarm condition
Motor running
Power failure auto-restart (optional
function)
Loaded
Remote load or remote pressure
regulation active
Amount of time, timer
Remote start/stop
Filter, differential pressure
Normal operational mode:
Selected item locked as
temporary default display
Menu mode:
Page item locked
(adjustment inhibited)
Pressure set point indication
(upper & lower set point indicators
displayed independently)
Condensate drain active (optional
function)
Compressor State
LED Status °
LED Fault
l
Shutdown Error
OFF
FF
Startup Init
OFF
OFF *
Start Inhibit Check
OFF
OFF *
Start Inhibit Condition
OFF
SF
Ready to Start
OFF
OFF *
Blowdown (If Load Request)
(Otherwise)
FF
IF
OFF *
OFF *
Standby
IF
OFF *
Start motor in Star/Delta (If Load Request)
(Otherwise)
FF
IF
OFF *
OFF *
Load Delay (If Load Request)
(Otherwise)
FF
IF
OFF *
OFF *
Load
ON
OFF *
Reload Delay (If Load Request)
(Otherwise)
FF
IF
OFF *
OFF *
Standby Run-on-Time
IF
OFF *
Stop Run-on-Time
SF
OFF *