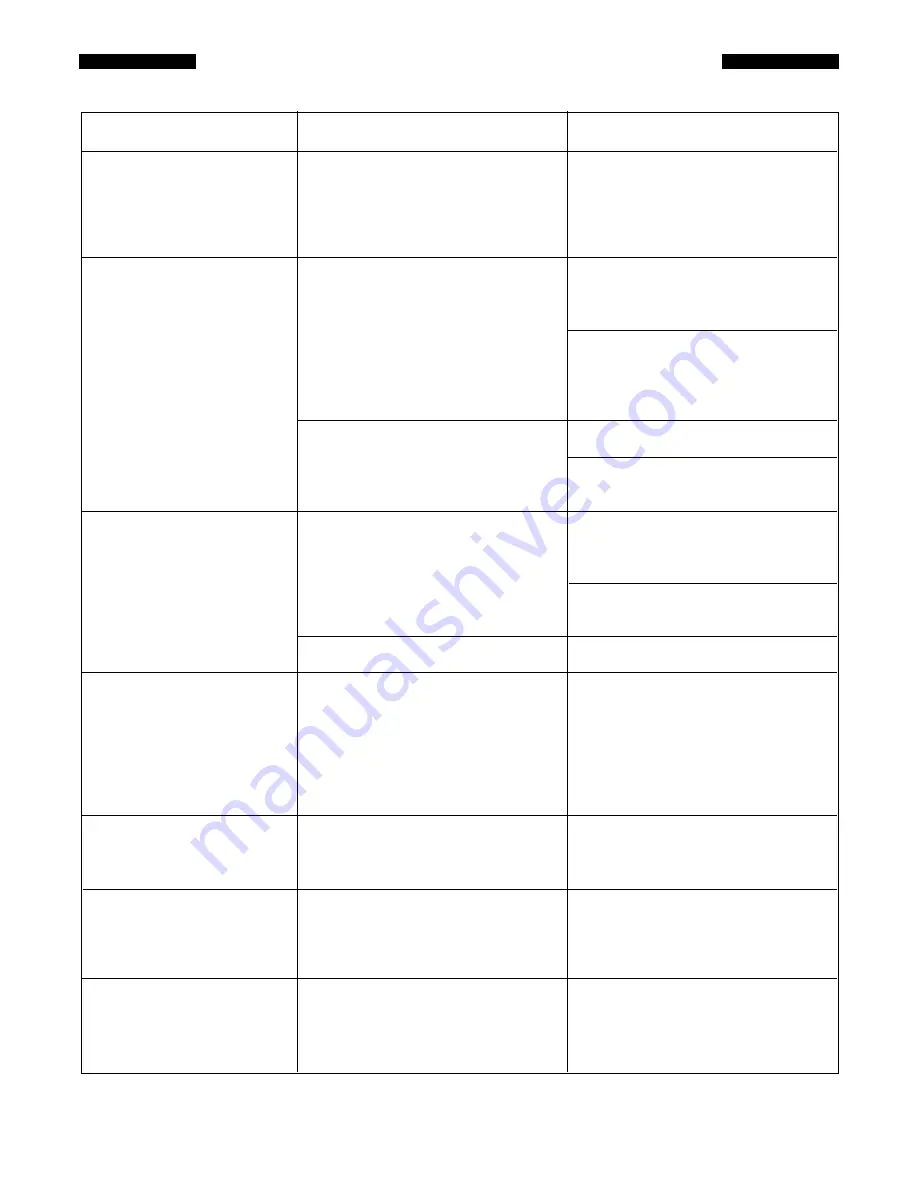
25
CONDITION 5a - PROLONGED “STUTTER” ON START-UP (AM-300)
• An occasional stutter when starting can be expected (i.e. - cold water/initial start-up.)
POSSIBLE CAUSE
VERIFICATION
SOLUTION
Incorrect Gas Supply
Check Gas Supply Pressure and
Adjust Gas Supply Pressure as
Pressure (should be
gas input rate as outlined under
necessary. A supply regulator
between 4.5" to 7.0" W.C.)
“Procedures” section of this manual.
may be required. Supply pressure to
boiler to be 4.5 - 7.0" W.C. running.
Adjust input rate per procedure.
Low Fan Pressure
Turn Rocker Switch & Gas Valve top
If gasket not seated properly -
(less than 1.0"W.C.)
knob to “OFF”. Remove ACC cover.
replace it. Follow “Procedures”
Remove fan from mounting studs &
section in this manual.
check for compression marks on
fan inlet gasket for complete seal to
If gasket is seated properly, proceed
air inlet adapter. Gasket is to fit
with check.
completly (360-degrees) around fan
inlet opening.
Check air inlet terminal for
If restricted - remove restriction.
restriction.
If no restriction proceed with
verification.
Loose or Restricted Air
Check that air inlet orifice (inside air
If air inlet orifice is loose, repair it.
Inlet Orifice
inlet adapter) is intact & not loose
Follow “Disassembling AM-300”
or broken. Drain hole must be clear.
procedure described in this manual.
See “Procedures” section (Fig. 7)
for detail.
If air inlet orifice is broken, replace
air inlet adapter.
Check for restriction in air inlet orifice.
Remove any restriction(s).
Valve Discs
Remove Gas Cushion Chamber
1. If valve discs have torn edges or
(GCC) & check bottom of valve
holes - replace discs.
plate. GCC valve discs must move
2. If foreign particles are between
freely and not bind.
valve plate & valve retaining plate-
remove them.
Reinstall boiler parts when
3. If valve discs are missing, stiff or
completed.
“wrinkled” replace them.
Long Horizontal Vent
Check that all vent piping runs are
Correct pitch of vent piping runs to
Piping with Minimal Pitch
pitched (minimum of 1/4" per foot)
prevent condensate blockage of
from vent terminal back to boiler.
exhaust / inlet piping.
Condensate Trapped in
Check for accumulation of
Eliminate low points in exhaust
Exhaust Vent Piping
condensate in low points of
piping or provide auxiliary
exhaust vent piping.
condensate drain taps.
(1/2" dia. max.)
Improperly Sized Vent
Check that all vent piping is specified
If incorrect, change vent piping.
Piping
Schedule 40; (not Schedule 80) and
maximum number of elbows and
vent length is not exceeded.