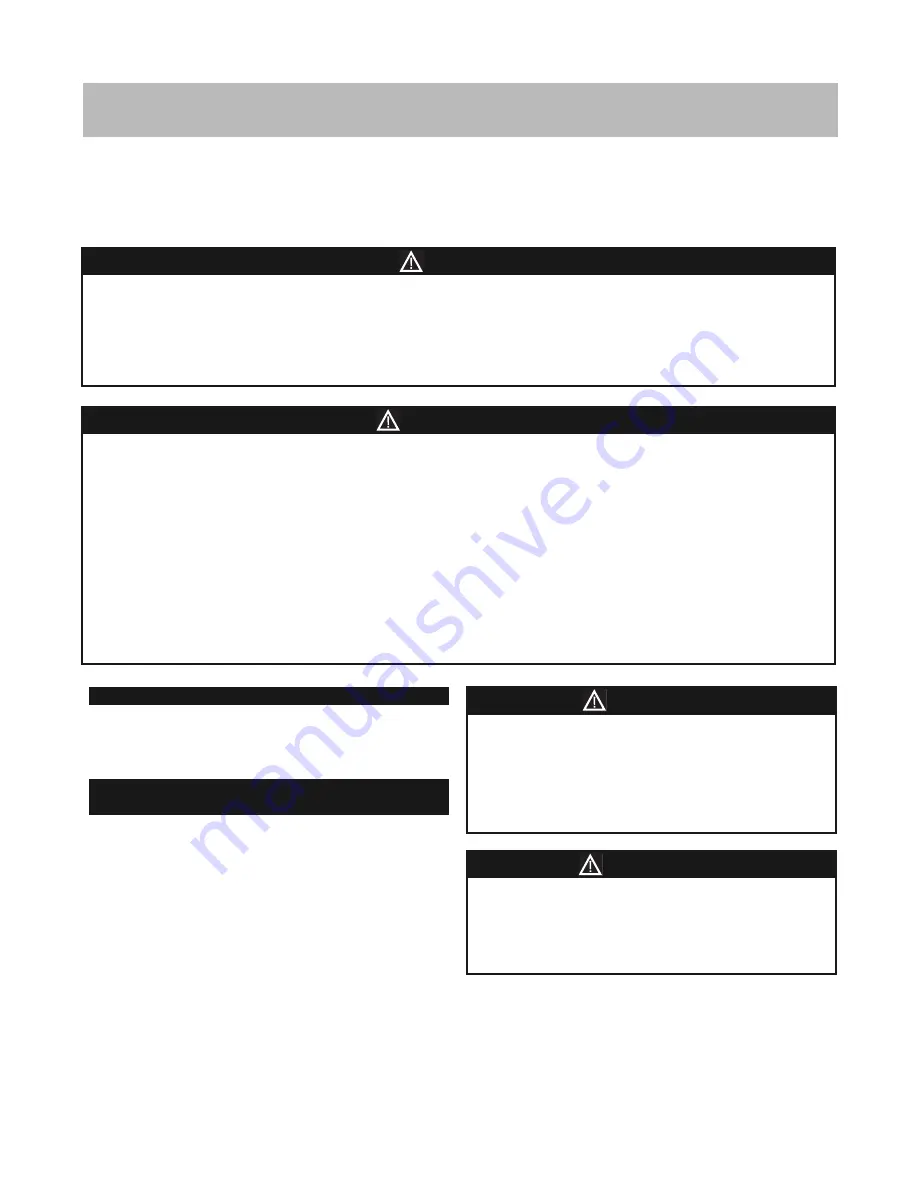
3
INSTALLATION AND OPERATING INSTRUCTIONS
A. ACCESSIBILITY CLEARANCES
Install boiler not less than 24
″
(610 mm) between the left
side, top, and front of the boiler and adjacent wall or
other appliance, when access is required for servicing.
B. CLEARANCE FROM COMBUSTIBLE
CONSTRUCTION
The design of this boiler is certified for alcove installation
with the following clearances:
1. 6
″
(152 mm) between sides and combustible
construction.
2. 24
″
(610 mm) between top of jacket and
combustible construction.
3. 6
″
(152 mm) between draft hood and combustible
construction.
4. 6
″
(152 mm) between vent pipe and combustible
construction.
5. 10
″
(254 mm) between rear of jacket and
combustible construction.
1. PREINSTALLATION
Read carefully, study these instructions before beginning work.
This boiler must be installed by a qualified contractor.
The boiler warranty can be voided if the boiler is not installed, maintained and serviced correctly.
The equipment must be installed in accordance with those installation requirements of the authority having
jurisdiction or, in the absence of such requirements, to the current edition of the
National Fuel Gas Code, ANSI
Z223.1/NFPA 54 and/or CAN/CSA B149.1,
Natural Gas and Propane Installation Code.
Where required by the authority having jurisdiction, the installation must conform to
American Society of
Mechanical Engineers Safety Code for Controls and Safety Devices for Automatically Fired Boilers, ASME CSD-1.
NOTICE
In accordance with Section 325 (f) (3) of the Energy Policy and Conservation Act, this boiler is equipped with a
feature that saves energy by reducing the boiler water temperature as the heating load decreases. This feature is
equipped with an override which is provided primarily to permit the use of an external energy management
system that serves the same function.
THIS OVERRIDE MUST NOT BE USED UNLESS AT LEAST ONE OF THE FOLLOWING CONDITIONS IS TRUE:
• An external energy management system is installed that reduces the boiler water temperature as the
heating load decreases.
• This boiler is not used for any space heating.
• This boiler is part of a modular or multiple boiler system having a total input of 300,000
BTU/hr or greater.
• This boiler is equipped with a tankless coil.
IMPORTANT
Do not install this boiler on carpeting. Boiler
installation on carpeting is a fire hazard. Install this
boiler on non-combustible flooring or use a
combustible floor pan to install this boiler on other
non-carpeted flooring.
WARNING
Do not install this boiler on combustible flooring
unless it is installed on a special combustible floor
pan. Boiler installation on combustible flooring
without the special pan is a fire hazard.
To order combustible floor pan, use the 5-digit stock
codes listed in Table 11.1 of this manual.
WARNING
Summary of Contents for 70-195
Page 21: ...21 INSTALLATION AND OPERATING INSTRUCTIONS Figure 7 3 Operating Instructions...
Page 22: ...22 INSTALLATION AND OPERATING INSTRUCTIONS Figure 7 4 Operating Instructions...
Page 35: ...35 INSTALLATION AND OPERATING INSTRUCTIONS Figure 11 4 Block Draft Hood Figure 11 5 Jacket...
Page 37: ...37 INSTALLATION AND OPERATING INSTRUCTIONS Figure 11 6 Controls Circulator Vent Damper...