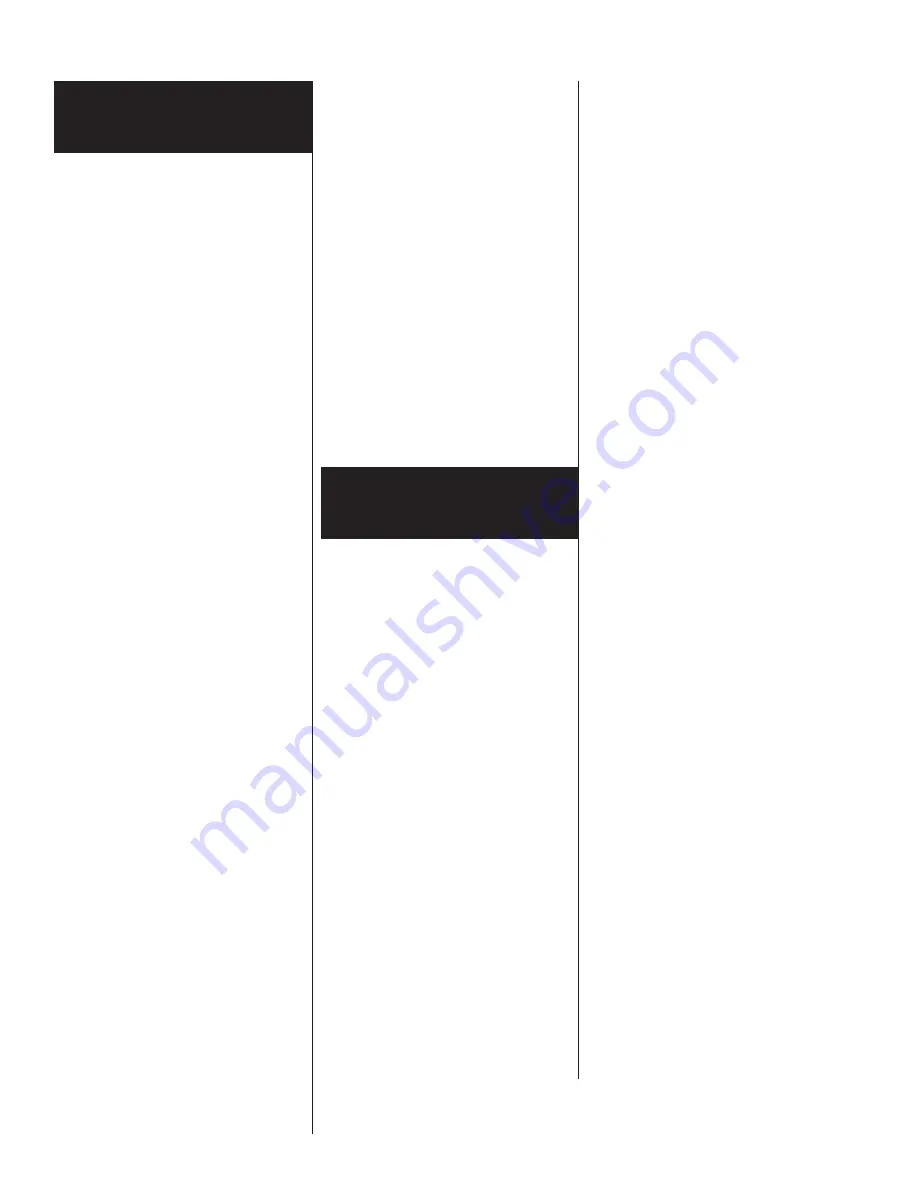
8
impeller, apply force then tap
on end of socket bolt to break
impeller loose from taper
shaft.
6. Remove key and pry on each
side of shoulder of shaft
sleeve to remove. Seal should
come off with sleeve. If sleeve
is not free, leave in place and
push off when seal plate
is removed.
7. To remove seal plate take out
socket head flat screws and
using screws in back-off
holes, pry plate loose. This
will also force seal off if not
already removed.
8. Remove snap ring that holds
upper seal. Pull seal if it is
free. If not free, it can be
forced off when shaft is
removed.
9. Remove 4 bolts that hold
bearing housing in place (on
units built prior to 2/14/78).
Set assembly
in upright
position and bump end of
shaft on hardwood block. This
will push the bearing from the
housing and will force upper
seal from shaft.
10. Use bearing puller to remove
bearings. Replace with new
bear ings. Press only on inner
face
of
bearing
when
replacing. Pressing on outer
face can damage the bearing.
Bearings are standard size
that can be obtained from
any bearing supply house or
can
be
obtained
from
Hydromatic factory.
11.
IMPORTANT: Do not use
any of the old seal parts.
Replace with all new seals.
12. Thoroughly clean all castings
before replacing seals. One
grain of dirt between the seal
faces can cause failure.
13. Examine all O-rings for nicks
before using.
14. Be sure key is in place in
notch of shaft sleeve to
prevent sleeve from turning.
15. Use Locktite
®
on socket head
locking screw in end of shaft.
16. Before refilling chamber with
oil, air test as described above.
17. Refill both chambers with oil
as described above.
18. Always check all leads with
high voltage or with Megger
for grounds before operating
the pump.
Below is a list of common problems
and the probable causes:
WARNINg: Before handling
pumps and controls always
disconnect power first. Do
not smoke or use sparkable
electrical devices or flame in a
septic (gaseous) or possible
septic sump.
Pump will not start.
1. No power to the motor. Check
for blown fuse or open
circuit breaker.
2. Selector switch may be in the
Off position.
3. Control circuit transformer
fuse may be blown.
4. Overload heater on starter may
be tripped. Push to reset.
Pump will not start and
overload heaters trip.
1. Turn off power and check
motor leads with Megger or
ohmmeter for possible ground.
2. Check resistance of motor
windings. All 3 phases should
show the same reading.
3. If no grounds exist and the
motor windings check OK,
remove pump from sump
and check for clogged or
blocked impeller.
Pump operates with selector
switch in Hand position but will
not operate in Auto position.
1. This indicates trouble in the
float level control or the
alternator relay.
2. To check for defective 3900
control, put selector switch in
Auto position and turn off
main power. Put a jump wire
between 2 and 3 on terminal
strip. Turn on power and if
pump starts, trouble is in the
lower 3900 control. Replace
control.
If pump does not start turn off
power, remove jumper from 2
and 3 and put jumper wire
between 1 and 2 terminals.
Turn on power and if pump
starts, trouble is in upper control.
Replace control.
If pump does not start, turn off
power and put jumper between
2 and 3 and 1 and 2 and turn on
power. If pump starts, both
lower and upper controls are
defective. If pump still does not
start, trouble is in the alternating
relay. Replace with new relay.
Pump runs but will not shut off.
1. Pump may be air locked. Turn
pump off and let set for several
minutes, then restart.
Pump
Troubleshooting
Pump
Maintenance
Summary of Contents for S4LRC
Page 15: ......