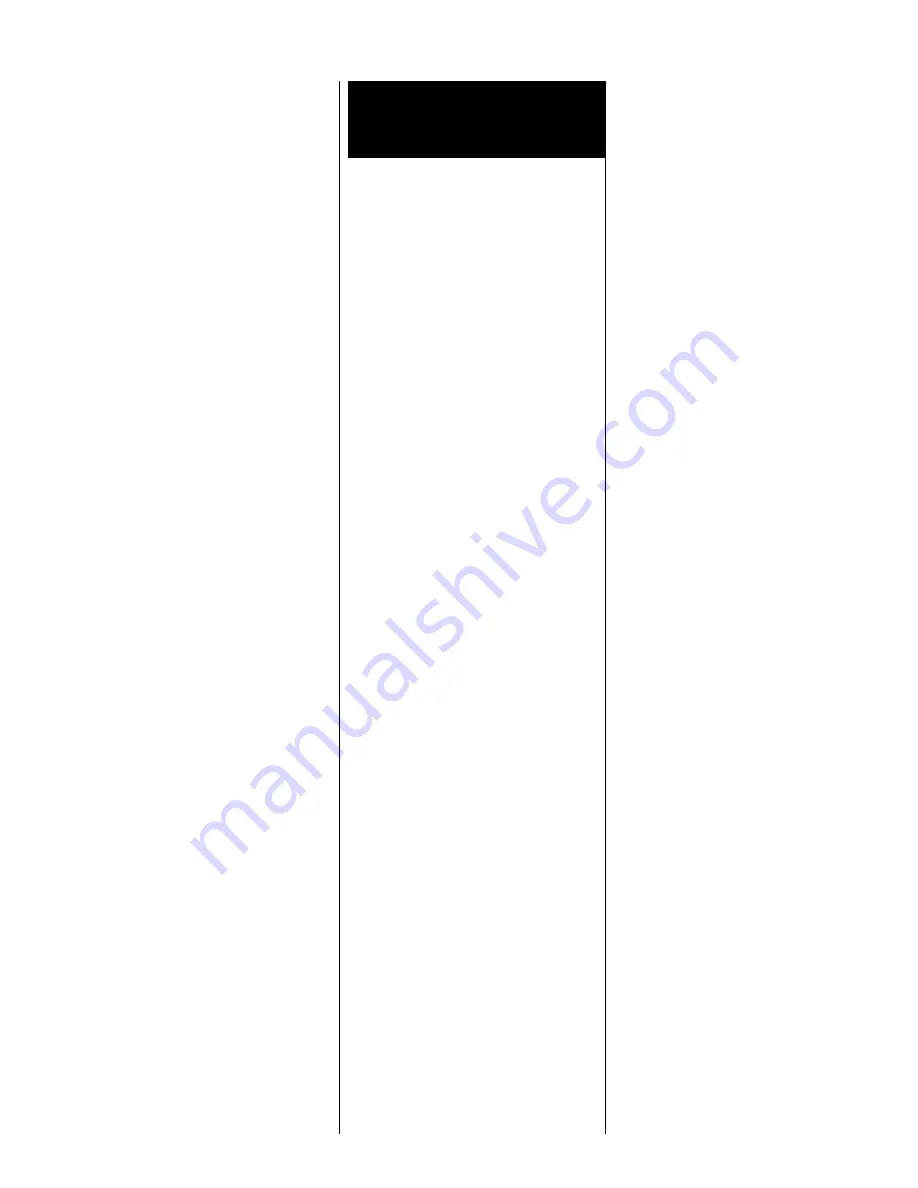
5
one pump starts. Allow pump
to operate until level drops
to turn-off point.
5. Allow sump level to rise to
start oth er pump. Notice run
lights on panel; pumps should
alternate on each suc ces sive
cycle of op er a tion.
6. Turn both H-O-A switch es
to Off po si tion and allow
sump to fill to the over ride
control level.
7. Turn both switches to Auto
po si tion and both pumps should
start and op er ate to geth er until
level drops to turn-off point.
8. Repeat this operation cycle
sev er al times before leav ing job.
9. Check voltage when pumps
are op er at ing and check the
amp draw of each pump. On 3
phase pumps, check amps on
each wire as sometimes a high
leg will exist. One leg can be
some what high er (5 to 10%)
without caus ing trou ble. For
excessive voltage, the power
com pa ny should be consulted.
As the motors are oil filled, no
lu bri ca tion or other main te nance
is required. The pump should be
lifted once every two years and
the oil drained from the motor
chamber to check for water.
generally these pumps give very
re li able service and can be expected
to op er ate for years on normal
sewage pump ing without failure.
Lightning:
In some areas where con sid er able
light ning occurs, it is recommended
that a light ning arrestor be
installed at the con trol panel.
Complete data on lightning
arrestors and cost are avail able
from the factory. Light ning ar res-
tors are good in sur ance against
damage to an ex pen sive motor.
Servicing instructions:
iMPOrTAnT:
read
all
in struc tions be fore replacing
any parts.
WArning: Before han dling
these pumps and controls, always
dis con nect the power first.
Do not smoke or use sparkable
elec trical devices or flames in
a sep tic (gas eous) or possible
septic sump.
Field Service on Motor:
All submersible motors can be
ser viced (out of warranty) in the
field by any reliable motor service
shop. Any pump (in warranty)
must be re turned to the factory
for ser vice or repaired in an
au tho rized Hydromatic ser-
vice center. Charges will not be
al lowed if (in war ran ty) pump
is taken to a mo tor repair
shop that is not an authorized
Hydromatic service cen ter.
When field service is per formed
on a pump, these in struc tions
should be care ful ly followed.
replacing Stator:
If motor winding is burned or
shorted, it can be rewound or
replaced with new fac to ry wound
stator. Refer to sec tion al draw ing
of pump and mo tor and use the
fol low ing steps to re move and
replace sta tor.
1. If stator only is damaged,
it may not be necessary to
completely dis mantle pump as
stator and hous ing can be lift ed
from pump without dis turb ing
seals or bear ings.
2. Drain all oil from upper housing.
If oil is clean and no water is
present, seals can be considered
satisfactory to reuse.
3. After chamber is drained,
remove hold-down bolts and
lift off motor housing. Use
care in lifting.
4. Set assembly on bench and
re move cord cap assembly by
removing bolts. When this is
lift ed off, con nec tion wires to
motor will be exposed. These
wires will prob a bly be burned,
but each wire is tagged with
a metal marker giv ing wire
num ber. Cut the wires.
5. If the leads to the cord cap
as sem bly are burned, the
cord cap assembly must be
re placed.
6. After stator retaining ring is
re moved, turn hous ing upright
and bump on hard wood blocks.
This should jar the stator loose
and al low it to drop out.
Pump
Maintenance
Summary of Contents for S3SD
Page 19: ......