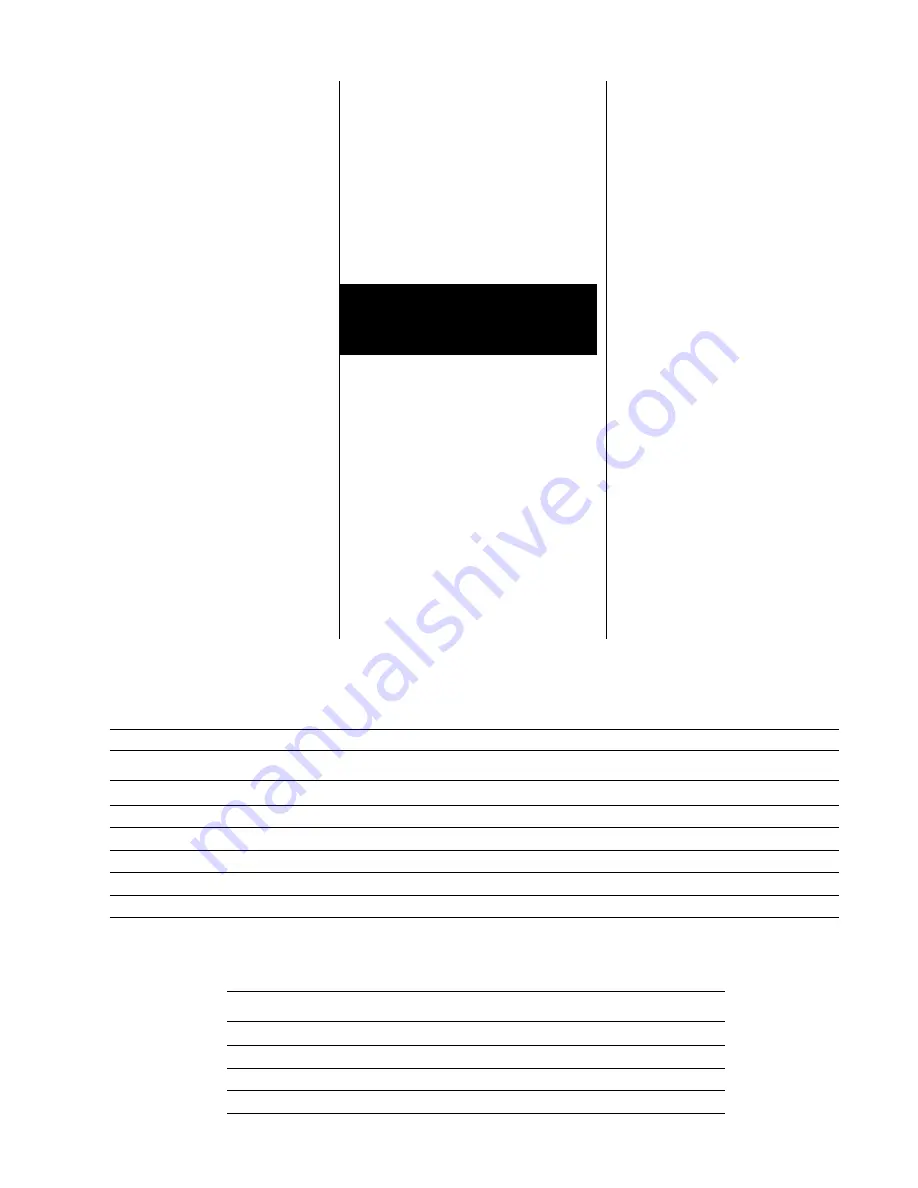
3
Hydromatic electrical equipment
is installed in a weatherproof
en clo sure. Electrical equipment
in cludes a main cir cuit breaker
for each pump, a magnetic start er
with over load pro tec tion for each
pump, an H-O-A switch and run
light for each pump, an electric
alter na tor and a trans form er to
provide ap pro pri ate control for
control circuit and alarms.
Overload Heaters:
If a Hydromatic control pan el is
not used, on three phase pumps all
three phases must have overload
protection. The overload should
be ambient compensated class
10. The heaters full load amps
on the pump should be sized in
accordance with the name plate
amps on the mo tor housing. The
amp draw on these sub mers ible
mo tors is slightly high er than a
cor re spond ing horsepower surface
motor so heaters must be sized by
the name plate full load amp rating.
installing Pump in Sump:
Before installing pump in sump,
lay it on side and turn impeller
with fingers. Im pel ler may be
slightly stuck due to fac to ry test
water so it must be broken loose
with small bar or screwdriver
in edge of vanes. The impeller
should turn freely.
Clean all trash and sticks from
sump and connect pump to piping.
A check valve must be in stalled
on each pump. A gate or plug
valve in each pump discharge
line is also rec om mend ed. This
valve should be in stalled on the
discharge side of the check valve
so if nec es sary to service the
check valve, the line pressure can
be cut off. Single pump sys tems
are sometimes in stalled without a
check valve where it is desirable
to self-drain the dis charge line to
pre vent freez ing. This can be done
only with short dis charge lines.
Oth er wise water will re turn to the
sump and cause short cycling of
the pump.
nEMA 4 Junction Box (Optional):
If electrical control panel is to be
set re mote from the pump sump, a
NEMA 4 junc tion box should be
used to make pow er and control
con nec tions. The Hydromatic
NEMA 4 junc tion box is pro vid-
ed with com pres sion con nec tors
for seal ing all wires. No sealing
com pound is need ed to make
con nec tions waterproof.
NUMBER OF CONDUCTORS REQUIRED BETWEEN CONTROL PANEL
AND NEMA 4 JUNCTION BOX
System
Number of
Number of
Number of
Type
Control Wires
Power Lines
Ground Wires #8
Simplex
3
3
1
Simplex with Alarm
5
3
1
Duplex
5
6
1
Duplex with Alarm
7
6
1
WIRE SIZE TABLE
FOR REMOTE LOCATION OF CONTROL PANEL LENGTHS ARE BASED ON A VOLTAGE DROP OF TWO PER CENT
Maximum length in feet from NEMA 4 junction box to con trol panel. For 3 phase only and for power lines only. All control wires can be = 14–16 or 18 gauge
wire. If power lines are for 460 or 575 volts in su la tion of control wires must be for this voltage if used in con duit with power lines.
Volts 230 460 575 230 460 575 230 460 575 230 460 575 230 460 575 230 460 575 230 460 575 230 460 575 230 460 575
Wire Motor
Size
HP
3
3
3
5
5
5
7
1
⁄
2
7
1
⁄
2
7
1
⁄
2
10 10 10 15 15 15 20 20 20 25 25 25 30 30 30 35 35 35
12
110 450 700 90 370 580
10
180 720 1120 140 550 370 90 360 560 50 220 340
8
270 1100 1650 220 900 1400 175 700 1100 105 420 650 320 500
230 360 180 280
6
400 1600 2500 350 1400 2200 220 900 1400 150 600 930 105 420 650 90 370 570 360 560 320 500 230 360
4
370 1500 2300 230 950 1450 175 700 1100 140 550 850 125 500 800 100 400 620 90 360 560
2
370 1500 230 270 1100 1700 220 900 1400 210 820 1250 200 800 1250 150 600 930
*Special Junction Box re quired for wire sizes larger than #4.
Single phase pumps with capacitor
start circuit must have the
overload protection on the black
pump lead.
nOTE: On single phase pumps
the white, black, and red pump
leads must be connected properly
for the pump to run.
Pump
Installation
Summary of Contents for S3SD
Page 19: ......