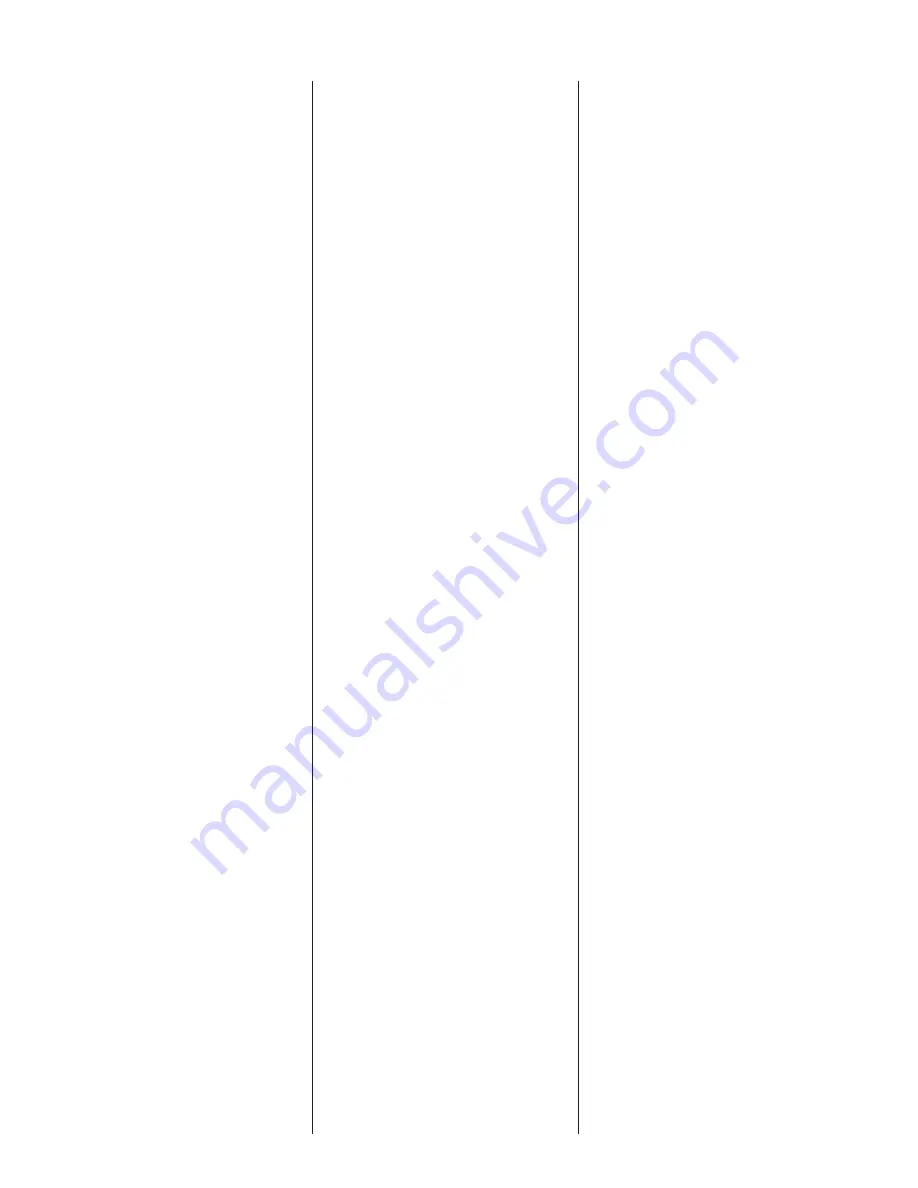
6
This is important as leads must
be tucked behind the windings
by using hands up through
rotor core.
IMPORTANT: Use only butt
connectors on the wires.
Do not tape leads as oil will
de te ri o rate the tape and cause
damage to stator and bearings.
9. Drain oil from seal chamber.
If oil is clean and no water
is present, seals can be
considered sat is fac to ry to
reuse.
10.Check top bearing. If clean and
does not turn rough, bearings
can be reused and it is not
necessary
to
completely
dismantle pump to change
bearings. If bearings are
damaged with dirt or heat,
they must be re placed. See
additional instructions on
replacing seals and bearings.
11.Replace stator housing onto
seal chamber and bolt in place.
Be sure seal failure wire is
connected before housing is
assembled. (See Figs. 2 and 3.)
Be sure back-off screws have
been loosened so that parts can
come metal to metal. Be
sure O-ring seal has been
replaced. If O-ring is nicked or
cut, replace with new ones.
This applies to all O-rings used
in assembly.
12.After all leads are reconnected
in the connection box, make
a high voltage ground test on
each wire. The only wire that
should show ground is the
green power lead and the
ground lead in the auxiliary
control cable.
13.For safety, complete pump
should be air checked under
water for leaks.
If seals were OK, refill seal
chamber with oil. Lay pump
on side for this oil filling
with oil fill hole upright.
Do not completely fill; leave
oil about 1 inch below plug
hole. Use only Hydromatic
submersible
oil
in
this
chamber. Replace plug; use
Permatex on threads. Install air
valve in top plug opening of
motor housing and charge
housing with about 10 psi of
air. Be sure air is dry. Do
not use air line where water
may be trapped in the line.
Submerge complete unit under
water and check for leaks.
14.Refill motor chamber with oil.
Use high grade transformer
oil or Hydromatic special
sub mers ible oil. Fill chamber
until oil covers top of the
windings. Leave air space in
the top for expansion. Use
Permatex on plug threads.
Replacing Seals and Bearings:
1. Drain all oil from motor
chamber and seal chamber
as described.
2. Remove motor housing as
described.
3. Remove bolts that hold seal
chamber to pump housing. Use
back-off screws to break loose.
With hardwood block, tape end
of impeller to loosen from
shaft. When free, remove
impeller from shaft.
4. Lift rotating assembly from
pump case and place on bench.
5. Impeller Removal: Hold rotor
and remove bolt and washer
from impeller end of shaft,
then thread bolt back into
shaft. The impeller is keyed
to the shaft, so by using a
screw driv er on opposite sides
behind the im pel ler, apply
force then tap on the end of the
bolt to break impeller loose
from taper shaft. Remove
impeller.
6. Remove key and pry on each
side of shoulder of shaft sleeve
to remove. Seal should come
off with sleeve. If sleeve is not
free, leave in place and push
off when seal plate is
removed.
7. To remove seal plate take
out socket head flat screws
and using screws in back-off
holes pry plate loose. This will
also force seal off if not
already re moved.
8. Remove snap ring that holds
upper seal. Pull seal if it is
free. If not free, it can be
forced off when shaft is
removed.
9. Set seal housing assembly in
upright position and bump end
of shaft on hardwood block.
This will push the bearing
from the housing and will
force upper seal from shaft.
10.Use bearing puller to remove
bearings. Replace with new
bearings. Press only on
inner face of bearing when
replacing. Pressing on outer
face can damage the bearing.
Bear ings are standard size that
can be obtained from any
bearing supply house or can
be obtained from Hydromatic
factory.
11.IMPORTANT—Do not use
any of the old seal parts.
Replace with all new seals.
12.Thoroughly clean all castings
before replacing seals. One
grain of dirt between the seal
faces can cause failure.
13.Examine all O-Rings for nicks
before reusing.
14.Be sure key is in place in
notch of shaft sleeve to
prevent sleeve from turning.
Summary of Contents for S12L Series
Page 8: ...8 Motor End Components ...
Page 9: ...9 S4T S8L S8LA S12L Wet End Components ...
Page 15: ......