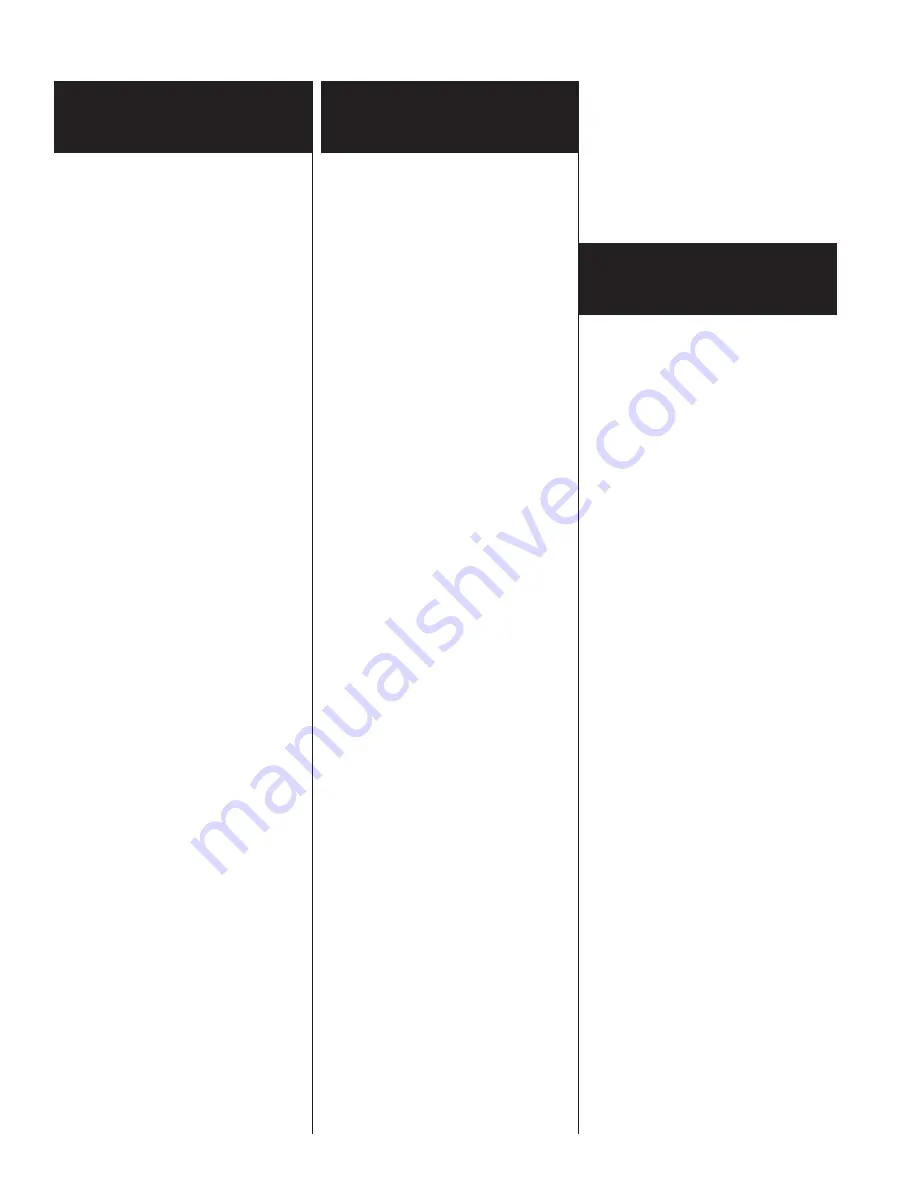
2
Thank you for purchasing your
Hydromatic
®
pump. To help
ensure years of trouble-free
operation, please read the
following manual carefully.
Before Operation:
Read the following instructions
carefully. Reasonable care and
safe methods should be practiced.
Check local codes and
requirements before installation.
Attention:
This manual contains important
information for the safe use of
this product. Read this manual
completely before using this
product and refer to it often for
continued safe product use.
DO NOT THROW AWAY OR
LOSE THIS MANUAL. Keep it
in a safe place so that you may
refer to it often.
Unpacking Pump:
Remove pump from carton. When
unpacking unit, check for
concealed damage. Claims for
damage must be made at the
receiving end through the delivery
carrier. Damage cannot be
processed from the factory.
WARNING: Before handling
these pumps and controls,
always disconnect the power
first. Do not smoke or use
sparkable electrical devices or
flames in a septic (gaseous) or
possible septic sump.
Pump Description:
The Hydromatic pumps covered
by these instructions are
submersible grinder pumps.
The cutter blades are on the
suction side of the centrifugal
pump impeller and discharge
directly into the inlet of the
impeller. The integral stainless
steel pump-motor shaft is sealed
by two mechanical seals with
an oil chamber between the seals
to provide lubrication for both
seal faces.
A radial sleeve bearing, lubricated
by the oil in the seal chamber, is
located between the seals and
takes the radial load from the
pump impeller and cutter blades.
The motor winding, rotor, and ball
thrust bearing are mounted in a
housing sealed and filled with oil
to lubricate the bearing and
transmit the heat from motor
winding to outer shell. The ball
thrust bearing is held in a movable
cap so that the axial cutter and
cutter ring clearance can be
adjusted from the outside without
the use of shims.
The power cord is sealed into the
motor housing with a cord grip,
and the individual conductors are
sealed into the cord cap with
epoxy sealing compound.
Application:
These pumps are designed for
either home or industrial sewage
discharge applications with a pH
ranging from 6 to 9, specific
gravities from 0.9 to 1.1,
viscosities ranging from 28 to 35
S.S.U., and temperatures up
to 140°F.
General
Information
Pump
Information
Codes:
All local wiring codes must be
observed. Consult the local
inspector before installation to
avoid costly delays that can
occur due to rejection after job
is finished.
Installation
Instructions
Location:
If pumps are installed in an
existing basin or concrete sump,
the piping can either be connected
permanently or rails and brackets
can be furnished for mounting to
walls of basin. In either case, be
sure that the Hydromatic non-clog
check valve is used and that the
pumps are submerged in a vertical
position. The complete factory
built packaged system is
recommended for the most
satisfactory installation and
generally for the lowest cost
where expensive installation labor
is involved.
Electrical Connections:
Make all connections from motor
to control panel to comply with
local codes.
CAUTION: Be sure ground
wire is connected to a good
ground such as a water pipe.
This is important for safety.