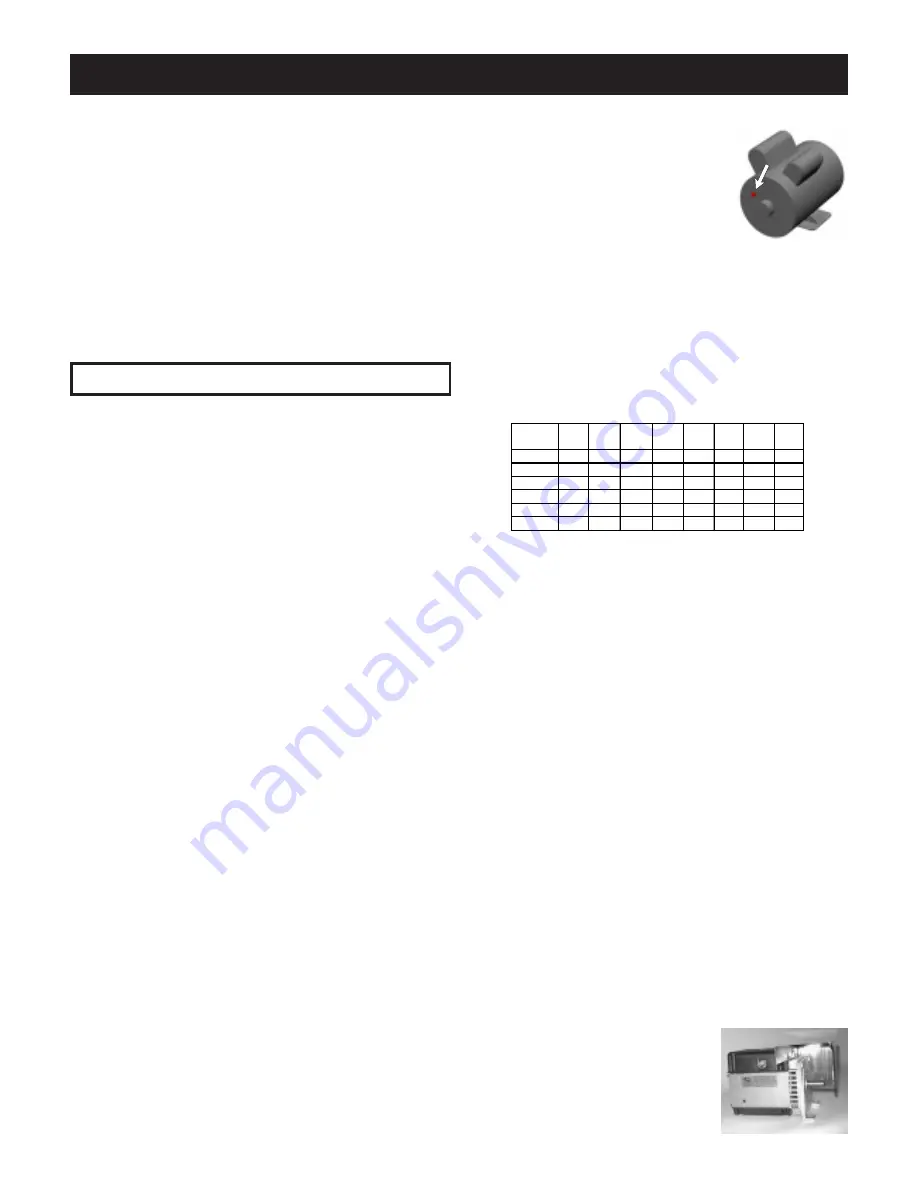
SHUT DOWN / SYSTEM INFORMATION
7
7. SET CHEMICAL INJECTION:
If unit is equipped with inlet chemical injection, place
chemical pickup tube in pre-mixed chemical solution and
open chemical valve for desired chemical concentration.
Rinse and close valve after use, do not use harsh chemi-
cals through the inlet injector system. If unit is equipped
with a downstream chemical injector, connect the chemical
injection assembly into the high pressure discharge hose
quick connects. Place the chemical pickup into chemical
solution and turn brass collar to adjust concentration. The
chemical will inject only when you drop the outlet pressure
by opening the valve on the dual wand or changing to a low
pressure nozzle. Soap the surface from the bottom up.
Close chemical valve when not in use.
8. If equipped, AF2 (2) gun operation, select "50%"
nozzle from panel and insert into coupler on spray gun
for full pressure output when using two guns at the
same time. Flow can be reduced by selecting flow
reduction nozzles only when one operator is using the
machine. Maximum temperature is 200° F.
SHUT DOWN:
1. TURN BURNER SWITCH TO THE OFF POSITION.
2. RINSE & CLOSE CHEMICAL VALVE.
3. SQUEEZE THE TRIGGER ON THE SPRAY GUN
UNTIL THE WATER BECOMES COOL.
4. TURN MOTOR/ENGINE SWITCH OFF with the
appropriate controls.
5. TURN OFF WATER SUPPLY.
6. SQUEEZE TRIGGER TO RELEASE ANY
TRAPPED PRESSURE IN DISCHARGE HOSE.
7. ANTIFREEZE EQUIPMENT:
In the event that the equipment is not to be used for an
extended period, store in heated space or antifreeze the unit.
Run the machine until the float tank is near empty, fill with
a 50% mix of water and antifreeze and run until antifreeze
appears at the high pressure outlet. If unit is equipped with
a blow out valve, it may be blown out with compressed air
in addition to using antifreeze solution. On direct feed units
(no float tank), use a 5' garden hose to draw the antifreeze
mix from a bucket. Or blow out the unit with compressed
air until only air and no water comes out of the discharge.
CHASSIS & TRAILER ASSEMBLY:
To maintain teh appearance of hte machne, use stainless steel
claner on teh stainless panels.
Check tire pressure. Check all bolts including the lug nuts for
tightness and condition periodically. Grease wheel bearings as
required and adjust after first month.
TIRE PRESSURE
T200
T300
T400
T500
35psi
35psi
40psi
40psi
POWER SYSTEMS:
ELECTRIC MOTORS: All single phase
electric motors contain a manual or auto-
matic thermal overload which will shut down
the motor if it overheats. If the overload or
starter shuts down the motor, have an elec-
trician or an authorized Hydro Tek distributor
check for electrical problems. Voltage reading under load
should be +/- 10% of name plate voltage on motor. The
motor can be reset by depressing the red overload button
located on either the motor or the starter, (as shown above).
Use thumb pressure only - DO NOT force. Wait for motor
to cool before re-setting. The automatic overload will reset
itself after the motor has cooled.
Never spray water on the unit, or damage to the electric
motor(s) may occur.
Consult the factory if running an electric machine from a
generator. Three times total system wattage is required.
A fused disconnect switch of sufficient ampere rating
should be installed by an electrician to provide power to the
machine. Refer to the chart above for electrical require-
ments: (208 Volt is acceptable, but unit motor must be under
nameplate amps; turn psi down). If your unit is equipped with
a ground fault interrupter, it will have to be reset whenever it
is plugged in, or if a ground fault interruption occurs. Test
regularly for proper operation.
GASOLINE ENGINE: With the proper care and main-
tenance, your gasoline engine will give years of trouble free
service. Please follow the Service and Maintenance Guide
and the enclosed engine sheet or contact your local authorized
engine dealer for maintenance and repairs.
Use unleaded gasoline with an octane rating of 87 or
higher in the engine fuel tank. Consult engine manual for
proper oil type and capacity. Change oil every 50 hours and
the filter every 100 hours (see engine manual). Do not rely
on the low oil shutdown (if equipped) as a reminder to add
oil. Engine damage from lack of oil will typically not be
warranted even if the low oil system failed.
On machines with a 115V generator or a 12V burner, the
throttle is preset at the factory (See Generator section on this
page for adjustment).
POWER TRANSMISSION:
DIRECT DRIVE: Pump is bolted
directly to the motor/engine. If pump
needs to be removed, do not force off by
prying or damage may occur. When
reassembling, coat the entire motor shaft
with heavy grease, or a generous amount
MAINTAIN PH BETWEEN 5 & 9
A=TOTAL SYSTEM AMPERES
HORSE
POWER
115V
1PH
WIRE
SIZE
208V
1PH
WIRE
SIZE
208V
3PH
WIRE
SIZE
230V
1PH
WIRE
SIZE
1.5
15A
12/3
N/A
N/A
N/A
N/A
10A
14
2
20A
12/3
N/A
N/A
N/A
N/A
12A
14
4
N/A
N/A
21A
10/3
N/A
N/A
20A
10/3
5
N/A
N/A
24A
10/3
N/A
N/A
23A
10/3
6.5
N/A
N/A
N/A
N/A
N/A
N/A
27A
10/3
7.5
N/A
N/A
N/A
N/A
N/A
N/A
35A
#8
Summary of Contents for HG SERIES
Page 16: ...WIRING DIAGRAMS ST 16 ...
Page 17: ...17 WIRING DIAGRAMS ST ...
Page 18: ...WIRING DIAGRAMS SR 18 ...
Page 19: ...19 WIRING DIAGRAMS SK ...
Page 20: ...20 WIRING DIAGRAM SH ...
Page 21: ...21 WIRING DIAGRAMS SH ...
Page 22: ...22 WIRING DIAGRAMS HG ...