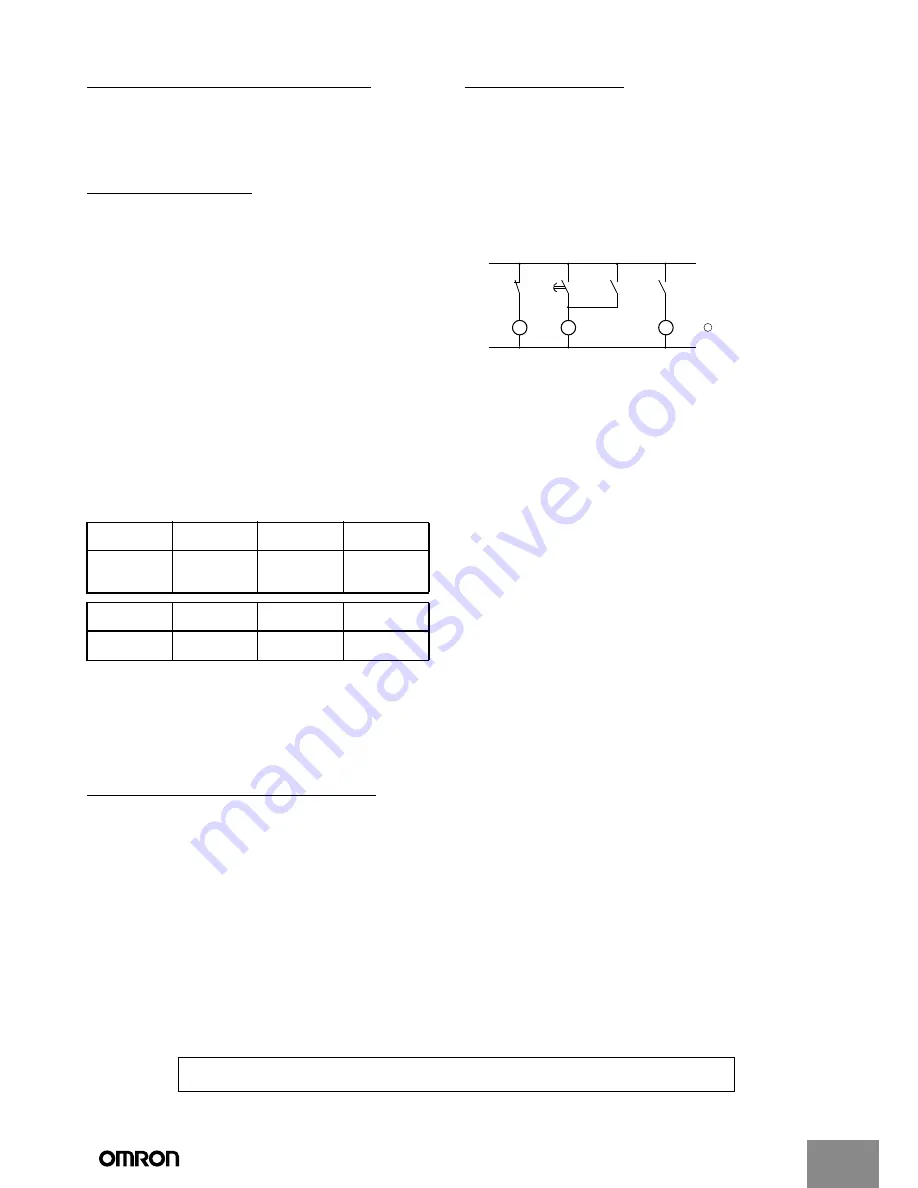
http://www.ia.omron.com/
C-2
(c)Copyright OMRON Corporation 2007 All Rights Reserved.
Correctly Handling Input Signals
Malfunction due to noise may occur if input wiring is placed in the
same duct or conduit as power lines or high-voltage lines. Separate
input wiring from power lines and wire them in a separate system.
Also, use shielded cables, use metal conduits, and keep wiring
distances as short as possible.
Timers with Relays
•
Do not connect a load that exceeds contact ratings, such as the
switching capacity (contact voltage or contact current). Insulation
faults, contact welding, contact faults, and other failures to achieve
specified performance may occur and the relay may be damaged or
may burn.
•
Continued use with deteriorated performance may ultimately result
in insulation breakdown between circuits or relay burning. The life
of the built-in relay is greatly affected by switching conditions.
Before using the Timer, test operation under actual application
conditions and confirm that the switching frequency presents no
problems in performance.
•
Electrical life depends on the type of load, switching frequency, and
ambient environment. Observe the following precautions when
using the Timer. When switching a DC load, contact transfer may
cause the contacts to stick or may cause contact failure. Confirm
applicability and consider using a surge absorbing element. When
switching at high frequencies, heat generated by arcing may cause
contacts to melt or may cause metal corrosion. Consider
connecting an arc absorbing element, reducing the switching
frequency, or lowering the humidity.
•
The surge current depends on the type of load, which also affects
contact switching frequency and the number of operations. Check
the rated current and the surge current, and design the circuits with
sufficient margin.
•
Arcing when switching and relay heating may result in ignition or
explosion. Do not use the Timer in atmospheres subject to
inflammable or explosive gases.
•
Contact faults may occur. Do not use the Timer in atmospheres
subject to sulfidizing gas, chloride gas, or silicon gas.
•
The switching capacity for DC voltage loads is lower than that for
AC voltage loads.
Timers with Non-contact Outputs
•
Short faults or open faults may occur due to destruction of the
output element. Do not use the Timer for a load that exceeds the
rated output current.
•
Short faults or open faults may occur due to destruction of the
output element from reverse electromotive force. When using the
Timer for a DC inductive load, always connect a diode as a
countermeasure against reverse electromotive force.
Other Precautions
•
Confirm that you have the correct model before using it.
•
Be sure that all terminals are wired correctly.
•
Always test the output status with a tester before using a Timer with
a built-in keep relay (e.g., the H3CR-H and H3DE-H). Shock
resulting from dropping the Timer during transport or handling may
cause the output contacts to reverse or to be in a neutral status.
•
Leaving the Timer with outputs ON at a high temperature for a long
time may hasten the degradation of internal parts (such as
electrolytic capacitors). Use the Timer in combination with relays
and avoid leaving the Timer with the output turned ON for an
extended period of time (e.g., for more than a month).
Reference Example (Use the Timer as shown below.)
•
Be sure that only a qualified worker (e.g., an electrical engineer)
performs electrical work for the Timer.
Resistive load
Solenoid load
Motor load
Incandescent
lamp load
Rated current
10 to 20 times
the rated
current
5 to 10 times
the rated
current
10 to 20 times
the rated
current
Sodium light
loads
Capacitor
loads
Transformer
loads
Mercury light
loads
1 to 3 times the
rated load
20 to 40 times
the rated load
5 to 15 times
the rated load
1 to 3 times the
rated load
X
X
1
T
X
2
X
2
/b
T/a
X
1
/a
X
1
/a
Auxiliary relay
(e.g., MY Relays)
In the interest of product improvement, specifications are subject to change without notice.
ALL DIMENSIONS SHOWN ARE IN MILLIMETERS.
To convert millimeters into inches, multiply by 0.03937. To convert grams into ounces, multiply by 0.03527.
Summary of Contents for AP Series
Page 1: ......
Page 15: ...Appendix 3 Technical Manual for Timers Grasslin 24 Hr Timer Omeron Micro Dose Timer ...
Page 29: ......
Page 30: ......
Page 31: ......
Page 32: ......
Page 33: ......
Page 34: ......
Page 35: ......
Page 36: ......
Page 37: ......
Page 38: ......
Page 39: ......
Page 40: ......
Page 41: ......
Page 42: ...Appendix 5 Drawings AP 500 ATU LPA 500 ATU AP 600 ATU AP 750 ATU AP 1000 ATU AP 1500 ATU ...