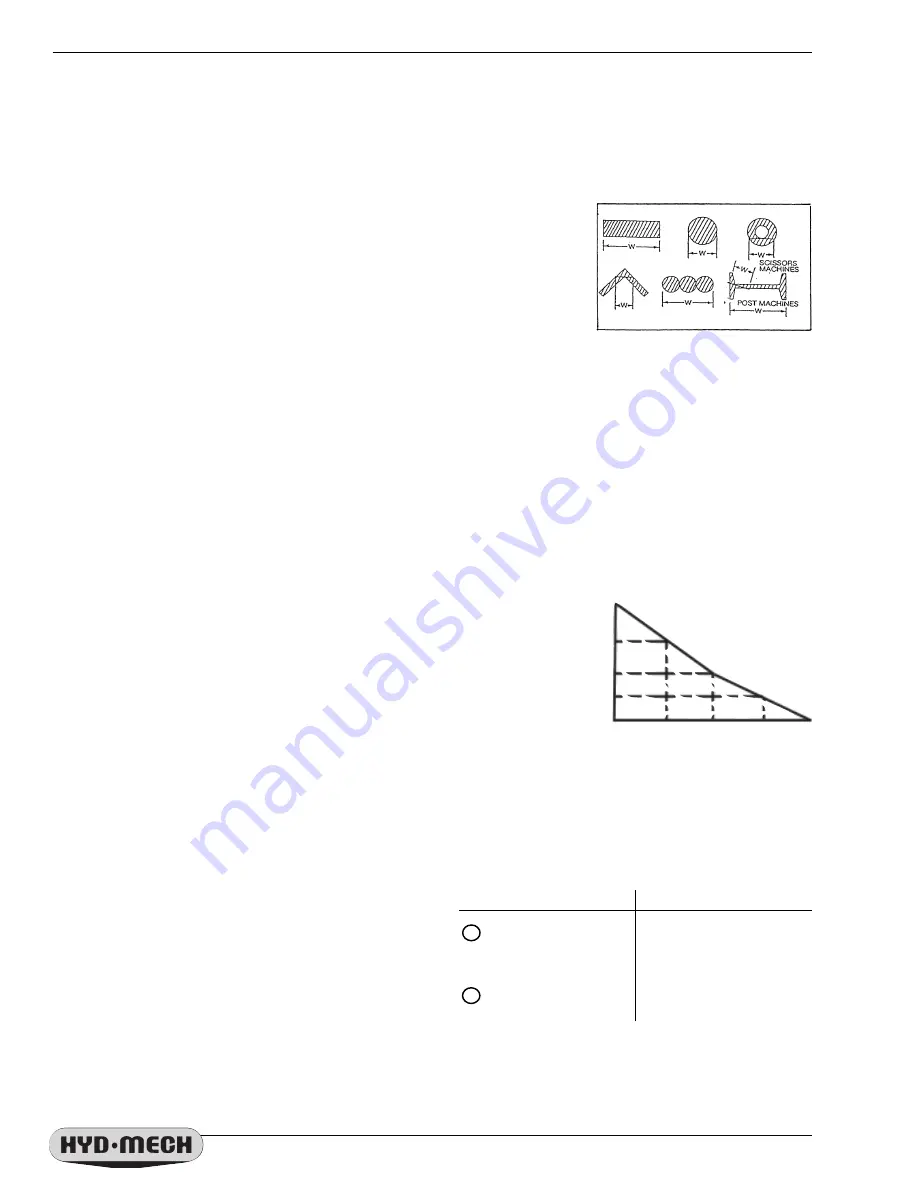
Pg 2.8
V18
CHART EXAMPLE #1
We will use the parameters chart to set up the saw for cutting 8" (200mm) Diameter #1045 Carbon Steel.
STEP 1,
DETERMINE EFFECTIVE MATERIAL WIDTH - W ( inches ) or (mm)
Effective material width, W (in.) for most common shapes of materials, is the
widest solid part of the material to be in contact with blade during cutting. For
simple shapes, as illustrated on the chart, this can be directly measured. For
bundles of tubes and structurals, measuring the effective width is difficult.
Effective width is 60% to 75% of the actual material width.
NOTES:
1) Both effective material width and guide arm width are used in setting the
saw.
2) Guide arm width is the distance between the guide arms and is used in STEP 2.
3) Effective material width, as determined here in STEP 1, can be thought of as the average width of material
“seen” by each tooth, and it is used in STEPS 3 and 4. In Example #1, for an 8" (200 mm) diameter solid,
Effective Material Width is 8" (200mm).
STEP 2,
SET FEED FORCE LIMIT
The Feed Force Limit is the maximum amount of force with which the head is allowed to push the blade into the
work-piece. FEED FORCE LIMIT should be set with the head in the down mode, according to the label.
CUTTING SOLIDS
For cutting solids, the wider the section, the less FF
should be set, to avoid blade overloading. See the graph.
EXAMPLE: When cutting a solid which is 1/2 of
machine capacity using the graph, locate 50% on the
horizontal line and travel upwards to the plotted line and
then travel directly across to the vertical FF Setting line.
The point that you have arrived at shows a setting of 40%
for a piece 50% of capacity.
CUTTING STRUCTURALS
A reduced Feed Force Setting is used when cutting
structurals:
For structurals, a blade finer than Optimum can be
used for more efficient cutting.
If a finer than optimum blade is going to be used, Feed
Force Setting should be reduced even further.
Material Width Chart
1 OPTIMUM PITCH
1 OPTIMUM PITCH
1 OPTIMUM PITCH
1 OPTIMUM PITCH
1 OPTIMUM PITCH
FROM STEP 3
FROM STEP 3
FROM STEP 3
FROM STEP 3
FROM STEP 3
20%
20%
20%
20%
20%
0%
0%
0%
0%
0%
2 PITCH FINER
2 PITCH FINER
2 PITCH FINER
2 PITCH FINER
2 PITCH FINER
THAN OPTIMUM
THAN OPTIMUM
THAN OPTIMUM
THAN OPTIMUM
THAN OPTIMUM
BLADE
BLADE
BLADE
BLADE
BLADE
FF SETTING
FF SETTING
FF SETTING
FF SETTING
FF SETTING
For OPTIMUM BLADE SELECTION, see STEP 3
For OPTIMUM BLADE SELECTION, see STEP 3
For OPTIMUM BLADE SELECTION, see STEP 3
For OPTIMUM BLADE SELECTION, see STEP 3
For OPTIMUM BLADE SELECTION, see STEP 3
100%
% of FF
70%
SETTING
40%
20%
0
25% 50%
75%
MAT’L WIDTH as % os
CAPACITY
Summary of Contents for V-18
Page 1: ...I N B A N D S A W T E C H N O L O G Y OPERATIONS MAINTENANCE M A N UA L ...
Page 3: ...THIS PAGE INTENTIONALLY LEFT BLANK ...
Page 6: ...SECTION 1 INSTALLATION SECTION 1 INSTALLATION ...
Page 7: ...SECTION 1 INSTALLATION ...
Page 13: ...THIS PAGE INTENTIONALLY LEFT BLANK ...
Page 14: ...SECTION 2 OPERATING INSTRUCTIONS SECTION 2 OPERATING INSTRUCTIONS ...
Page 15: ...SECTION 2 OPERATING INSTRUCTIONS ...
Page 28: ...SECTION 3 MAINTENANCE AND TROUBLE SHOOTING SECTION 3 MAINTENANCE AND TROUBLE SHOOTING ...
Page 29: ...SECTION 3 MAINTENANCE AND TROUBLE SHOOTING ...
Page 39: ...Pg 3 10 V18 2001e SERVICE RECORD NOTES DATE SERVICED BY COMMENTS ...
Page 40: ...SECTION 4 ELECTRICAL SYSTEM SECTION 4 ELECTRICAL SYSTEM ...
Page 41: ...SECTION 4 ELECTRICAL SYSTEM ...
Page 46: ...THIS PAGE INTENTIONALLY LEFT BLANK ...
Page 47: ...ELECTRICAL SCHEMATIC WIRING DIAGRAMS ...
Page 48: ......
Page 49: ......
Page 50: ......
Page 51: ......
Page 52: ......
Page 53: ......
Page 54: ......
Page 55: ......
Page 56: ......
Page 57: ...ELECTRICAL SCHEMATIC WIRING DIAGRAMS ...
Page 58: ......
Page 59: ......
Page 60: ......
Page 61: ......
Page 62: ......
Page 63: ......
Page 64: ......
Page 65: ......
Page 66: ......
Page 67: ...THIS PAGE INTENTIONALLY LEFT BLANK ...
Page 68: ...SECTION 5 HYDRAULIC SYSTEM SECTION 5 HYDRAULIC SYSTEM ...
Page 69: ...SECTION 5 HYDRAULIC SYSTEM ...
Page 71: ...Pg 5 2 V18 CYLINDER ASSEMBLIES Piston assemblies Gland assemblies ...
Page 72: ...THIS PAGE INTENTIONALLY LEFT BLANK ...
Page 73: ...HYDRAULIC SCHEMATIC and PLUMBING DRAWINGS ...
Page 74: ......
Page 75: ......
Page 76: ......
Page 77: ...THIS PAGE INTENTIONALLY LEFT BLANK ...
Page 78: ...SECTION 6 MECHANICAL ASSEMBLIES SECTION 6 MECHANICAL ASSEMBLIES ...
Page 79: ...SECTION 6 MECHANICAL ASSEMBLIES ...
Page 81: ...Pg 6 2 V18 2001c GUIDE ARM ASSEMBLIES ...
Page 89: ...Pg 6 10 V18 2001c COOLANT PARTS and ASSEMBLY DRAWING ...
Page 92: ...THIS PAGE INTENTIONALLY LEFT BLANK ...
Page 93: ...HM5 gear box assembly ...
Page 94: ......
Page 95: ...THIS PAGE INTENTIONALLY LEFT BLANK ...
Page 96: ...SECTION 7 OPTIONAL ASSEMBLIES SECTION 7 OPTIONAL ASSEMBLIES ...
Page 97: ...SECTION 7 OPTIONAL ASSEMBLIES ...
Page 108: ...Pg 7 11 V18 2001 a EXTENDED HEAD GUIDE ARM ASSEMBLIES ...
Page 110: ...SECTION 8 SPECIFICATIONS SECTION 8 SPECIFICATIONS ...
Page 111: ...SECTION 8 SPECIFICATIONS ...
Page 114: ...SECTION 9 WARRANTY SECTION 9 WARRANTY ...
Page 115: ...SECTION 9 WARRANTY ...