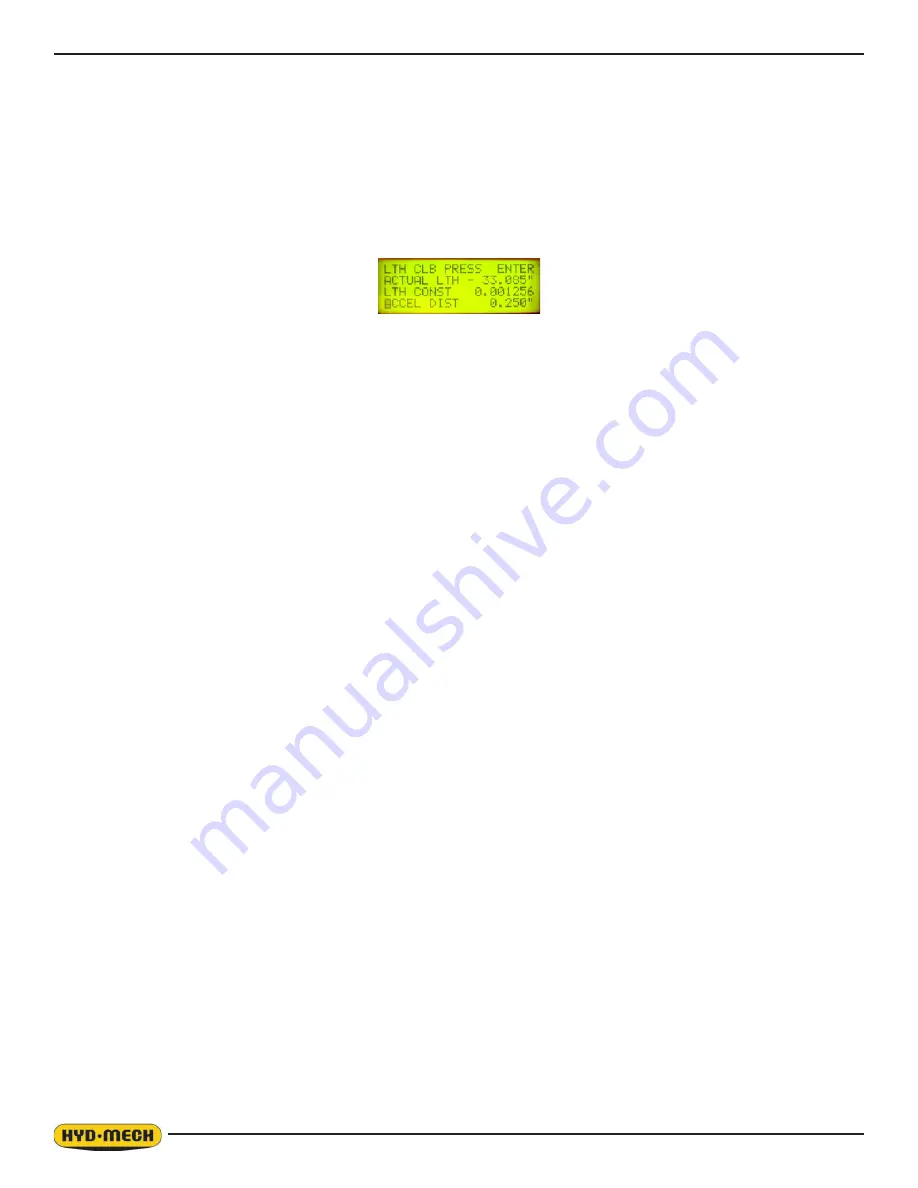
3.18
3.19
CALIBRATION PROCEDURE
Length calibration may be achieved in two ways, by inputting the ACTUAL LTH or LTH CONST parameter.
To determine the ACTUAL LTH value, the LTH CLB (length calibration) procedure must be executed.
In manual mode, position a piece of material, which is longer that the shuttle full stroke length and close the
front vise. Simultaneously press the “FWD” and “REV” buttons on the PLC to access the parameter. A pass-
word is required at this point, which can be obtained from the Hyd·Mech Service Dept. The screen will then
display as follows:
With the cursor at the shown position press the enter button. The cycle start button will the start to flash and
the “Enter” will change to “On” indication self calibration modes. Start the blade and the trim cut will be made.
After the trim cut is made the head will rise, the shuttle will retract fully in slow speed, clamp the material and
come fully forward in slow speed to the home position and make a cut. After the cut is complete “On” will
change back to “Press Enter”. Measure the length of the cut part.
Move the cursor down to the “ACTUAL LTH” and enter the length of the cut part. Then exit the parameters by
pressing the AUTO/MAN key (the cycle start button will stop flashing). To determine if the encoder channels
are connected correctly, observe the actual length parameter for the sign only during shuttle retraction in cali-
bration mode. If the actual length value shows as a negative number, then the channels must be reversed and
the calibration procedure repeated.
To determine “LTH CONST” value, use this formula;
LTH CONST = ENCODER PINION CIRCUMFERENCE (TTd)
÷
ENCODER RESOLUTION
Example:
For a 1” pinion diameter and 2500 PPR encoder:
LTH CONST = TTD
÷
2500PPR = 0.001257
NOTE:
When first entering the parameters screen if not running the self-calibration do not use the enter key but use
the cursor keys to scroll through the parameters.
To check length control consistency:
1. Perform test cuts of three different lengths (i.e. 1”, 12”, 20”) and measure as accurately as possible with
a Vernier or dial caliper.
2. If the measurements indicate a linear problem (measured length error increases as the programmed
length increases), the “ACTUAL LGTH” or “LTH CONST” value will have to be adjusted.
To adjust “ACTUAL LGTH” value
The Length Calibration Procedure MUST be performed. This may be done
with material in the machine (cut and measure material length) or with no material in the machine (let machine
complete the calibration cycle, then enter new value).
If part length error gets longer as the programmed length increases; ACTUAL LTH value should be increased.
If part length error gets shorter as the programmed length increases; ACTUAL LTH value should be decreased.
Make small adjustments at a time (i.e. .020” - .030”) and check with test cuts.
Summary of Contents for H-18 ASV
Page 4: ......
Page 6: ...1 2 H 18 22 SV LIFTING INSTRUCTIONS ...
Page 24: ......
Page 44: ......
Page 46: ...4 2 Electrical Disconnect and Fuses Mitsubishi PLC Transformer Mitsubishi Inverter ...
Page 49: ...4 5 ...
Page 53: ...4 9 ...
Page 54: ...4 10 ...
Page 55: ...4 11 ...
Page 56: ...4 12 H 18 22 SV ELECTRICAL WIRING DIAGRAM NO OPTIONS 208 240 VAC ...
Page 57: ...4 13 ...
Page 58: ...4 14 ...
Page 59: ...4 15 ...
Page 60: ...4 16 ...
Page 61: ...4 17 ...
Page 62: ...4 18 H 18 22 SV ELECTRICAL WIRING DIAGRAM INPUTS OUTPUTS NO OPTIONS 208 240 VAC ...
Page 63: ...4 19 ...
Page 64: ...4 20 H 18 22 SV ELECTRICAL SCHEMATIC WITH OPTIONS 208 240 VAC ...
Page 65: ...4 21 ...
Page 66: ...4 22 ...
Page 67: ...4 23 ...
Page 68: ...4 24 H 18 22 SV ELECTRICAL WIRING DIAGRAM WITH OPTIONS 208 240 VAC ...
Page 69: ...4 25 ...
Page 70: ...4 26 ...
Page 71: ...4 27 ...
Page 72: ...4 28 ...
Page 73: ...4 29 ...
Page 74: ...4 30 H 18 22 SV ELECTRICAL WIRING DIAGRAM INPUTS OUTPUTS WITH OPTIONS 208 240 VAC ...
Page 75: ...4 31 ...
Page 76: ...4 32 H 18 22 SV ELECTRICAL SCHEMATIC NO OPTIONS 480 575 VAC ...
Page 77: ...4 33 ...
Page 78: ...4 34 ...
Page 79: ...4 35 ...
Page 80: ...4 36 H 18 22 SV ELECTRICAL WIRING DIAGRAM NO OPTIONS 480 575 VAC ...
Page 81: ...4 37 ...
Page 82: ...4 38 ...
Page 83: ...4 39 ...
Page 84: ...4 40 ...
Page 85: ...4 41 ...
Page 86: ...4 42 H 18 22 SV ELECTRICAL WIRING DIAGRAM INPUTS OUTPUTS WITH NO OPTIONS 480 575 VAC ...
Page 87: ...4 43 ...
Page 88: ...4 44 H 18 22 SV ELECTRICAL SCHEMATIC WITH OPTIONS 480 575 VAC ...
Page 89: ...4 45 ...
Page 90: ...4 46 ...
Page 91: ...4 47 ...
Page 92: ...4 48 H 18 22 SV ELECTRICAL WIRING DIAGRAM WITH OPTIONS 480 575 VAC ...
Page 93: ...4 49 ...
Page 94: ...4 50 ...
Page 95: ...4 51 ...
Page 96: ...4 52 ...
Page 97: ...4 53 ...
Page 98: ...4 54 H 18 22 SV ELECTRICAL WIRING DIAGRAM INPUTS OUTPUTS WITH OPTIONS 480 575 VAC ...
Page 99: ...4 55 ...
Page 100: ......
Page 102: ...5 2 GLAND ASSEMBLIES PISTON ASSEMBLIES ...
Page 103: ...5 3 H 18 22 SV HYDRAULIC SCHEMATIC ...
Page 104: ...5 4 H 18 22 SV PLUMBING DIAGRAM ...
Page 105: ...5 5 ...
Page 106: ......
Page 120: ...6 14 H 18 SV DRIVE ASSEMBLY ...
Page 121: ...6 15 ...
Page 122: ...6 16 H 22 SV DRIVE ASSEMBLY ...
Page 123: ...6 17 ...
Page 124: ......
Page 126: ...7 2 H 18 22 SV OUTBOARD BUNDLING ASSEMBLY ...
Page 128: ...8 2 H 18 SV LAYOUT ...
Page 129: ...8 3 H 22 SV LAYOUT ...
Page 130: ......