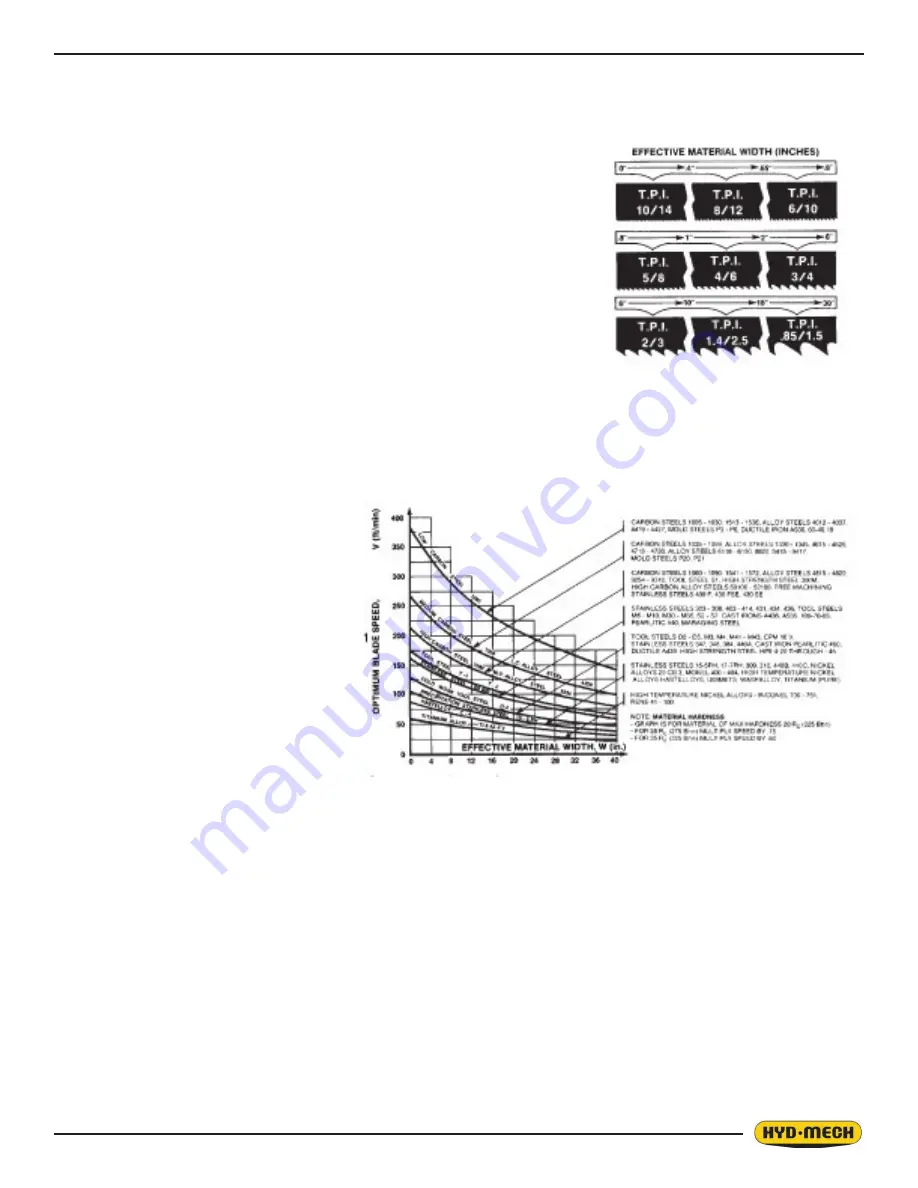
2.10
2.11
many teeth per inch (T.P.I.) is recommended. For wide materials a blade with a coarse pitch should be used. The sketch
can be referenced for the blade pitch changes for differing effective material widths.
It is impractical to change the blade to the proper pitch every time a different
width of material is cut and it is not necessary, but remember that the optimum
blade will cut most efficiently. Too fine a blade must be fed slower on wide
material because the small gullets between the teeth will get packed with
chips before they get across and out of the cut. Too coarse a blade must be
fed slower because it has fewer teeth cutting and there is a limit to the depth
of a cut taken by each tooth. Allowance for the use of a non-optimum blade is
made in STEP 5.
In our Example #1: Effective material width of 8” (200 mm) & Optimum blade
has 2/3 teeth per inch.
STEP 4; DETERMINE OPTIMUM BLADE SPEED, V (ft/min) (m/min)
The relationship between optimum blade speed and effective material width
for various materials is represented on the graph shown.
The graph shows that as effective material width gets wider or as material gets harder, lower blade speeds are recom-
mended. If material is narrow or soft, higher blades speeds should be selected.
In Example #1
1. 8” (200mm) diameter #1045 Medium
Carbon Steel solid bar is to be cut.
2. On the graph above find the Me-
dium Carbon Steel Curve which
represents the optimum blade
speeds for 1045 Carbon Steel.
3. On the horizontal axis (effective
material width axis) find number 8
which represents effective material
width of an 8” (200mm) diameter
solid.
4. Find the point where a vertical line
from 8” (200mm) intersects the
Medium Carbon Steel Curve.
5. From this intersection point run
horizontally left to the vertical axis
(optimum blade speed axis) and
find the point marked “200”.
6. For 8” (200mm) diameter, 1045 Carbon Steel solid bar 200 ft/min (60m/min) is the optimum blade speed.
NOTE:
1. Higher than optimum blade speed will cause rapid blade dulling. Lower than optimum blade speeds reduce
cutting rates proportionately and do not result in significantly longer blade life except where there is a vibration
problem. If the blade vibrates appreciably at optimum speed as most often occurs with structurals and bundles, a
lower blade speed may reduce vibration and prevent premature blade failure.
2. Material Hardness - The graph above illustrates blade speed curves for materials of hardness 20 RC (225 Bhn) or
lower. If the material is hardened then the multipliers need to be used. These multipliers are given in the NOTE at
the bottom right of the graph. As the hardness increases the optimum blade speed decreases.
STEP 5, DETERMINE FEED RATE SETTING, FR (in/min) (mm/min).
FEED RATE is the vertical speed at which the blade descends through the work-piece.
The FEED RATE Knob controls FEED RATE of the blade descent in the range 0 to 15 in/min (380mm/min). The FEED
RATE should be adjusted only in one direction (from “O” to required value). If you go too far, go back to “O” and come
Summary of Contents for H-18 ASV
Page 4: ......
Page 6: ...1 2 H 18 22 SV LIFTING INSTRUCTIONS ...
Page 24: ......
Page 44: ......
Page 46: ...4 2 Electrical Disconnect and Fuses Mitsubishi PLC Transformer Mitsubishi Inverter ...
Page 49: ...4 5 ...
Page 53: ...4 9 ...
Page 54: ...4 10 ...
Page 55: ...4 11 ...
Page 56: ...4 12 H 18 22 SV ELECTRICAL WIRING DIAGRAM NO OPTIONS 208 240 VAC ...
Page 57: ...4 13 ...
Page 58: ...4 14 ...
Page 59: ...4 15 ...
Page 60: ...4 16 ...
Page 61: ...4 17 ...
Page 62: ...4 18 H 18 22 SV ELECTRICAL WIRING DIAGRAM INPUTS OUTPUTS NO OPTIONS 208 240 VAC ...
Page 63: ...4 19 ...
Page 64: ...4 20 H 18 22 SV ELECTRICAL SCHEMATIC WITH OPTIONS 208 240 VAC ...
Page 65: ...4 21 ...
Page 66: ...4 22 ...
Page 67: ...4 23 ...
Page 68: ...4 24 H 18 22 SV ELECTRICAL WIRING DIAGRAM WITH OPTIONS 208 240 VAC ...
Page 69: ...4 25 ...
Page 70: ...4 26 ...
Page 71: ...4 27 ...
Page 72: ...4 28 ...
Page 73: ...4 29 ...
Page 74: ...4 30 H 18 22 SV ELECTRICAL WIRING DIAGRAM INPUTS OUTPUTS WITH OPTIONS 208 240 VAC ...
Page 75: ...4 31 ...
Page 76: ...4 32 H 18 22 SV ELECTRICAL SCHEMATIC NO OPTIONS 480 575 VAC ...
Page 77: ...4 33 ...
Page 78: ...4 34 ...
Page 79: ...4 35 ...
Page 80: ...4 36 H 18 22 SV ELECTRICAL WIRING DIAGRAM NO OPTIONS 480 575 VAC ...
Page 81: ...4 37 ...
Page 82: ...4 38 ...
Page 83: ...4 39 ...
Page 84: ...4 40 ...
Page 85: ...4 41 ...
Page 86: ...4 42 H 18 22 SV ELECTRICAL WIRING DIAGRAM INPUTS OUTPUTS WITH NO OPTIONS 480 575 VAC ...
Page 87: ...4 43 ...
Page 88: ...4 44 H 18 22 SV ELECTRICAL SCHEMATIC WITH OPTIONS 480 575 VAC ...
Page 89: ...4 45 ...
Page 90: ...4 46 ...
Page 91: ...4 47 ...
Page 92: ...4 48 H 18 22 SV ELECTRICAL WIRING DIAGRAM WITH OPTIONS 480 575 VAC ...
Page 93: ...4 49 ...
Page 94: ...4 50 ...
Page 95: ...4 51 ...
Page 96: ...4 52 ...
Page 97: ...4 53 ...
Page 98: ...4 54 H 18 22 SV ELECTRICAL WIRING DIAGRAM INPUTS OUTPUTS WITH OPTIONS 480 575 VAC ...
Page 99: ...4 55 ...
Page 100: ......
Page 102: ...5 2 GLAND ASSEMBLIES PISTON ASSEMBLIES ...
Page 103: ...5 3 H 18 22 SV HYDRAULIC SCHEMATIC ...
Page 104: ...5 4 H 18 22 SV PLUMBING DIAGRAM ...
Page 105: ...5 5 ...
Page 106: ......
Page 120: ...6 14 H 18 SV DRIVE ASSEMBLY ...
Page 121: ...6 15 ...
Page 122: ...6 16 H 22 SV DRIVE ASSEMBLY ...
Page 123: ...6 17 ...
Page 124: ......
Page 126: ...7 2 H 18 22 SV OUTBOARD BUNDLING ASSEMBLY ...
Page 128: ...8 2 H 18 SV LAYOUT ...
Page 129: ...8 3 H 22 SV LAYOUT ...
Page 130: ......