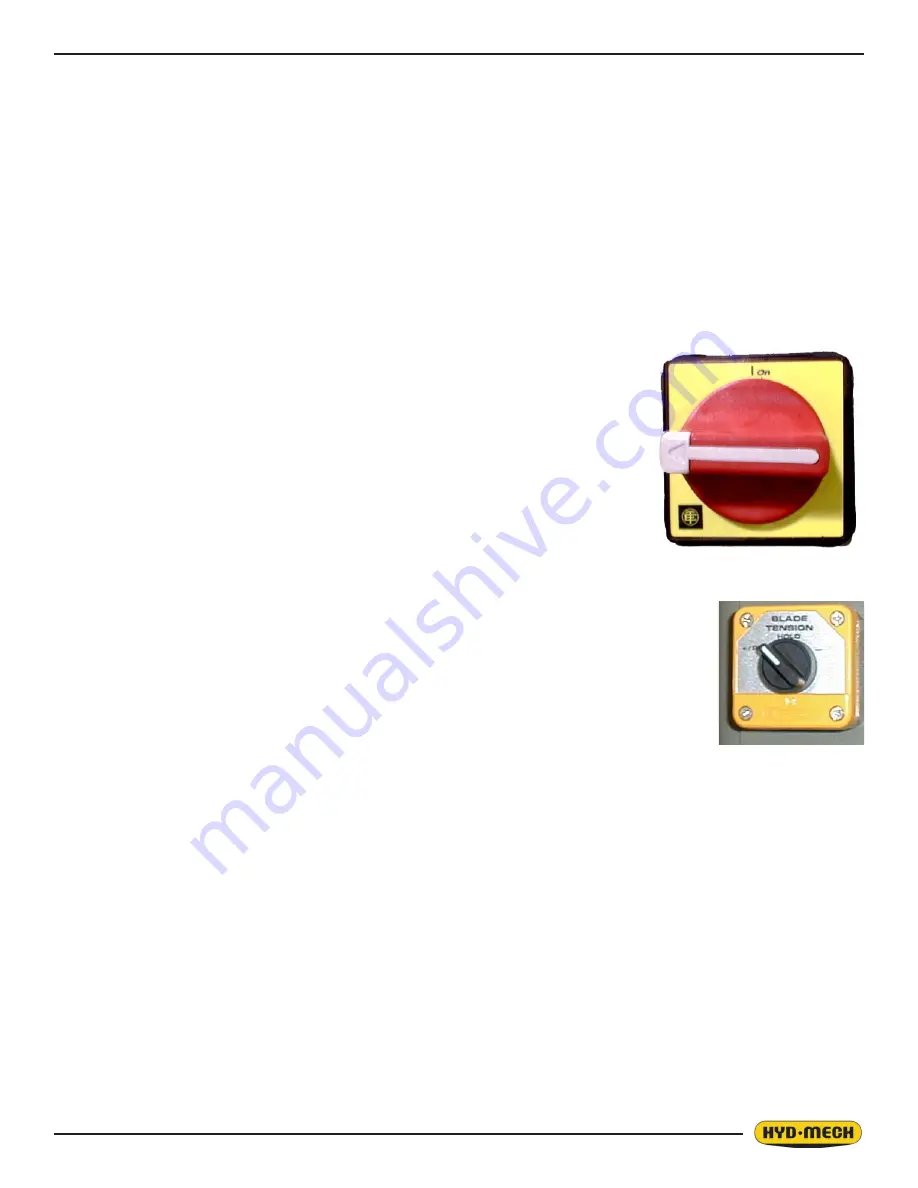
3.1
SECTION 3, MAINTENANCE AND TROUBLE SHOOTING
LOCK -OUT
Purpose:
To prevent injury to workers caused by unexpected start-up of machines being worked on.
OR
Where the starting of a machine or device may endanger the safety of a worker
a. Control switches or other control mechanisms shall be locked out;
AND
b. Other effective precautions necessary to prevent such starting shall be taken
LOCK OUT PROCEDURE
Whenever work is to be performed on a machine, the person in charge should follow
Lockout procedures as is required by his organization. The main power disconnect box
is supplied with a suitable mechanism for this purpose as shown below. To place a lock
on the switch, turn the switch to OFF.
BLADE CHANGING PROCEDURE
NOTE:
Wear gloves, safety glasses and a long sleeve shirt for protection from the sharp blade.
The hydraulics should be OFF any time the operator has his/her hands in contact with
the blade.
1. Select MANUAL mode and raise the head so the drive door will clear the elec-
trical control panel.
2. Release the blade tension by turning the Blade Tension Switch to “-”.
3. Remove the blade guard.
4. Shut the machine off and open the idler and drive doors.
5. At the top of the head, the saw blade runs in a protective channel. Grip the blade at each
end of this channel and twist the blade teeth down past the channel and slide the blade
forward. Let the blade rest on the out feed table, then slide the blade down and out of the
carbide guides.
6. Before installing the new blade, check that it measures 1.615” wide including the teeth.
Some blade manufacturers supply blades that measure 1.5” including the teeth. The
same applies to 2” blades, they should measure 2.120”. In this case you may not be able
to adjust the head down limit to complete the cut.
7. Your new blade will be in a coil. While wearing gloves hold the blade away from you, twist the blade to uncoil it.
Do not let the blade teeth bounce on the concrete floor as some damage to the blade may be caused.
8. Place the new blade in the carbide guides and then slide the blade over the wheels. The teeth should be pointing
towards the drive side as they pass through the carbide guides.
9. Turn the machine on and the blade tension switch to the “+ RUN” position, turn the two carbide locking handles
clockwise to the locked position. Jog the blade a few rotations to check that the blade is not moving on or off the
wheels.
NOTE:
Whenever the blade is changed, the KERF value (1 1/4” blade = 0.060” - 0.065”, 1 1/2” blade = 0.076 - 0.082”) should be
checked and the new value entered into the PLC. See page 12 for entering instructions.
Summary of Contents for H-18 ASV
Page 4: ......
Page 6: ...1 2 H 18 22 SV LIFTING INSTRUCTIONS ...
Page 24: ......
Page 44: ......
Page 46: ...4 2 Electrical Disconnect and Fuses Mitsubishi PLC Transformer Mitsubishi Inverter ...
Page 49: ...4 5 ...
Page 53: ...4 9 ...
Page 54: ...4 10 ...
Page 55: ...4 11 ...
Page 56: ...4 12 H 18 22 SV ELECTRICAL WIRING DIAGRAM NO OPTIONS 208 240 VAC ...
Page 57: ...4 13 ...
Page 58: ...4 14 ...
Page 59: ...4 15 ...
Page 60: ...4 16 ...
Page 61: ...4 17 ...
Page 62: ...4 18 H 18 22 SV ELECTRICAL WIRING DIAGRAM INPUTS OUTPUTS NO OPTIONS 208 240 VAC ...
Page 63: ...4 19 ...
Page 64: ...4 20 H 18 22 SV ELECTRICAL SCHEMATIC WITH OPTIONS 208 240 VAC ...
Page 65: ...4 21 ...
Page 66: ...4 22 ...
Page 67: ...4 23 ...
Page 68: ...4 24 H 18 22 SV ELECTRICAL WIRING DIAGRAM WITH OPTIONS 208 240 VAC ...
Page 69: ...4 25 ...
Page 70: ...4 26 ...
Page 71: ...4 27 ...
Page 72: ...4 28 ...
Page 73: ...4 29 ...
Page 74: ...4 30 H 18 22 SV ELECTRICAL WIRING DIAGRAM INPUTS OUTPUTS WITH OPTIONS 208 240 VAC ...
Page 75: ...4 31 ...
Page 76: ...4 32 H 18 22 SV ELECTRICAL SCHEMATIC NO OPTIONS 480 575 VAC ...
Page 77: ...4 33 ...
Page 78: ...4 34 ...
Page 79: ...4 35 ...
Page 80: ...4 36 H 18 22 SV ELECTRICAL WIRING DIAGRAM NO OPTIONS 480 575 VAC ...
Page 81: ...4 37 ...
Page 82: ...4 38 ...
Page 83: ...4 39 ...
Page 84: ...4 40 ...
Page 85: ...4 41 ...
Page 86: ...4 42 H 18 22 SV ELECTRICAL WIRING DIAGRAM INPUTS OUTPUTS WITH NO OPTIONS 480 575 VAC ...
Page 87: ...4 43 ...
Page 88: ...4 44 H 18 22 SV ELECTRICAL SCHEMATIC WITH OPTIONS 480 575 VAC ...
Page 89: ...4 45 ...
Page 90: ...4 46 ...
Page 91: ...4 47 ...
Page 92: ...4 48 H 18 22 SV ELECTRICAL WIRING DIAGRAM WITH OPTIONS 480 575 VAC ...
Page 93: ...4 49 ...
Page 94: ...4 50 ...
Page 95: ...4 51 ...
Page 96: ...4 52 ...
Page 97: ...4 53 ...
Page 98: ...4 54 H 18 22 SV ELECTRICAL WIRING DIAGRAM INPUTS OUTPUTS WITH OPTIONS 480 575 VAC ...
Page 99: ...4 55 ...
Page 100: ......
Page 102: ...5 2 GLAND ASSEMBLIES PISTON ASSEMBLIES ...
Page 103: ...5 3 H 18 22 SV HYDRAULIC SCHEMATIC ...
Page 104: ...5 4 H 18 22 SV PLUMBING DIAGRAM ...
Page 105: ...5 5 ...
Page 106: ......
Page 120: ...6 14 H 18 SV DRIVE ASSEMBLY ...
Page 121: ...6 15 ...
Page 122: ...6 16 H 22 SV DRIVE ASSEMBLY ...
Page 123: ...6 17 ...
Page 124: ......
Page 126: ...7 2 H 18 22 SV OUTBOARD BUNDLING ASSEMBLY ...
Page 128: ...8 2 H 18 SV LAYOUT ...
Page 129: ...8 3 H 22 SV LAYOUT ...
Page 130: ......