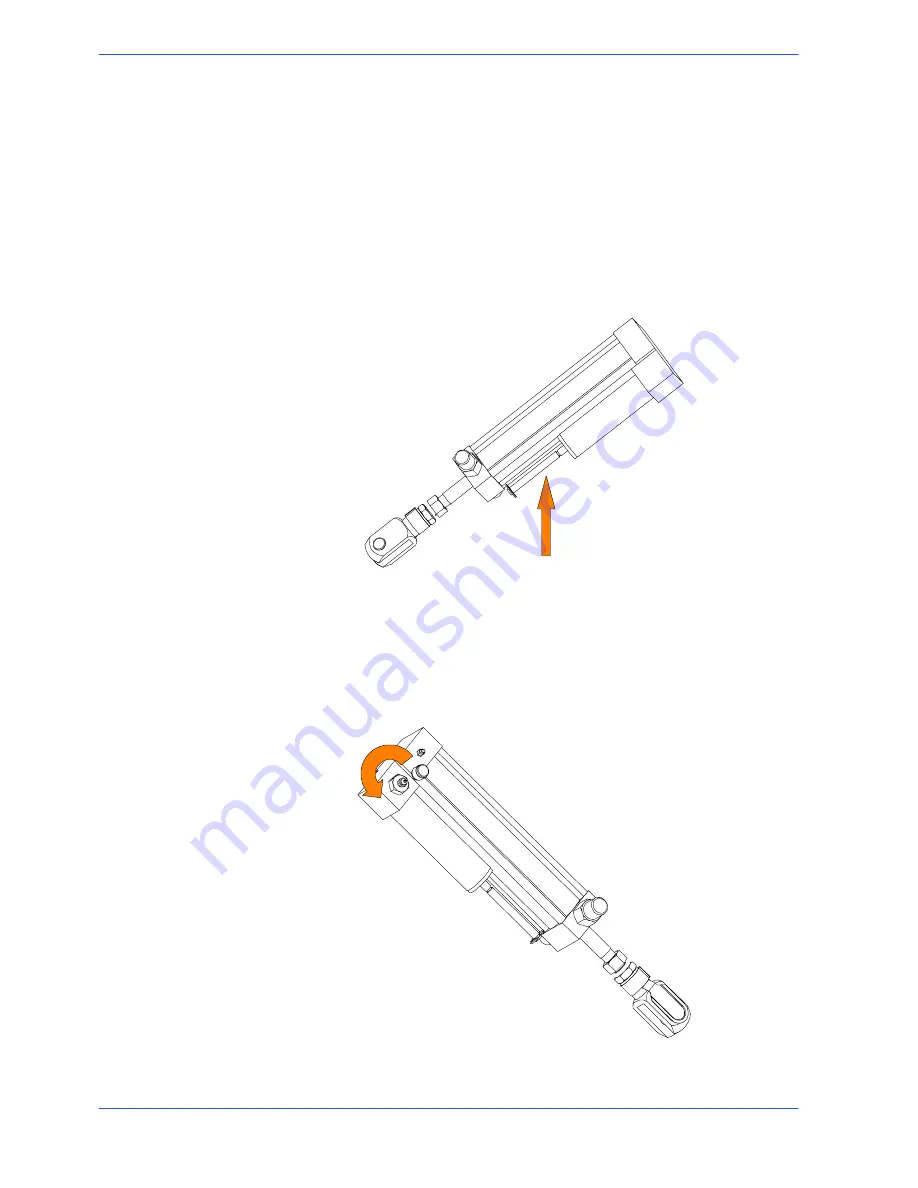
MEP S.p.A.
7--2
Use and maintenance manual DM 8
Topping up and bleeding the cylinder (Cut Control System)
Topping up the head cylinder
This operation is done when the oil in the hydraulic cylinder compensator tank is
low.
First the cylinder head is brought to the HUL (Head Up Limiter) position so that
the oil level in the compensation tank (see photograph below) can be checked
using the rod. If the rod upper ring location is not visible, the oil level is insuffi-
cient.
To top up the oil in the tank, the instructions are as follows:
"
keep the head in the HUL position (fully up) by closing the head descent reg-
ulator;
"
unscrew the filler valve cap;
Summary of Contents for DM8
Page 1: ...CA YEAR OF MANUFACTURE ______________ USE AND MAINTENANCE MANUAL DM 8 ...
Page 2: ......
Page 6: ......
Page 57: ...MEP S p A 6 8 Use and maintenance manual DM 8 DM 8 G 208 60 ...
Page 58: ...Version 24DM Diagrams exploded views and replacement parts 6 9 DM 8 G 208 60 K42 ...
Page 59: ...MEP S p A 6 10 Use and maintenance manual DM 8 DM 8 G 208 60 ...
Page 65: ...MEP S p A 6 16 Use and maintenance manual DM 8 DM 8 G 240 60 ...
Page 66: ...Version 24DM Diagrams exploded views and replacement parts 6 17 DM 8 G 240 60 K42 ...
Page 67: ...MEP S p A 6 18 Use and maintenance manual DM 8 DM 8 G 240 60 ...
Page 73: ...MEP S p A 6 24 Use and maintenance manual DM 8 DM 8 G 575 60 ...
Page 74: ...Version 24DM Diagrams exploded views and replacement parts 6 25 DM 8 G 575 60 K42 ...
Page 75: ...MEP S p A 6 26 Use and maintenance manual DM 8 DM 8 G 575 60 ...
Page 81: ...MEP S p A 6 32 Use and maintenance manual DM 8 DM 8 G 220 Vac ...
Page 82: ...Version 24DM Diagrams exploded views and replacement parts 6 33 DM 8 G 220 Vac K42 ...
Page 83: ...MEP S p A 6 34 Use and maintenance manual DM 8 DM 8 G 220 Vac ...
Page 91: ...MEP S p A 6 42 Use and maintenance manual DM 8 Front flywheel assembly ...
Page 93: ...MEP S p A 6 44 Use and maintenance manual DM 8 Motor flywheel assembly ...
Page 95: ...MEP S p A 6 46 Use and maintenance manual DM 8 Cutting head cover ...
Page 97: ...MEP S p A 6 48 Use and maintenance manual DM 8 Vice assembly ...
Page 99: ...MEP S p A 6 50 Use and maintenance manual DM 8 Base assembly ...
Page 101: ...MEP S p A 6 52 Use and maintenance manual DM 8 Control panel ...
Page 103: ...MEP S p A 6 54 Use and maintenance manual DM 8 Handgrip 3OUT3 ...
Page 105: ...MEP S p A 6 56 Use and maintenance manual DM 8 Reduction gear ...
Page 107: ...MEP S p A 6 58 Use and maintenance manual DM 8 Fixed work table and turntable ...
Page 109: ...MEP S p A 6 60 Use and maintenance manual DM 8 Optional Cut Control System ...
Page 111: ...MEP S p A 6 62 Use and maintenance manual DM 8 Supplementary pneumatic vice ...
Page 113: ......
Page 155: ......
Page 156: ......