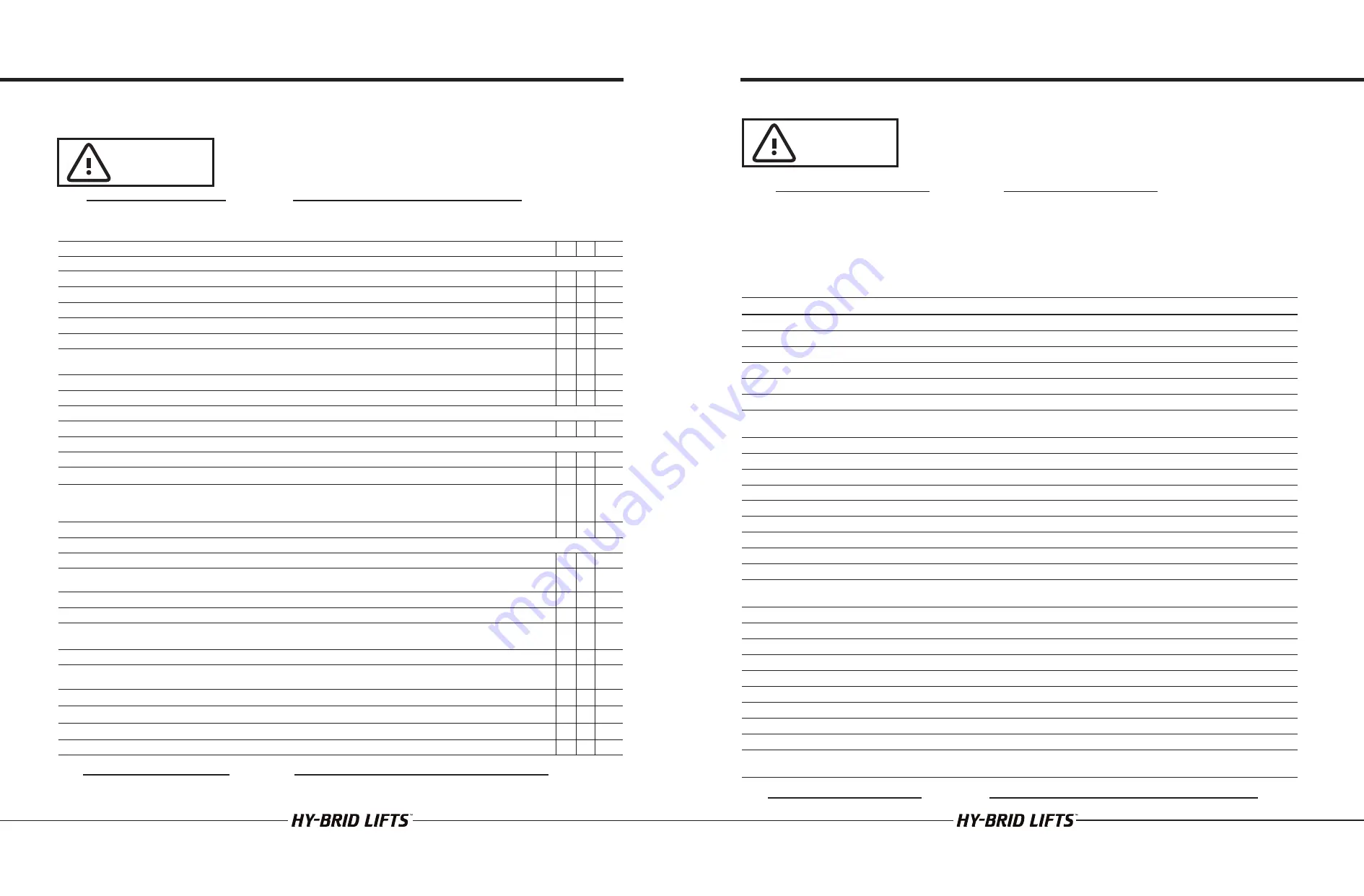
Model:
Serial Number:
• Check each item listed below.
• Use proper operating, service, and maintenance manual for specifi c information and settings
• If an item is found to be unacceptable make the necessary repairs and check the “repaired” box.
• When all items are “acceptable”, the unit is ready for service.
• If an item is found to be unacceptable, make the necessary repairs and check the “repaired” box. When all
items are “acceptable,” the unit is ready for service.
Y — Yes/Acceptable N — No/Unacceptable R — Repaired N/A — Not equipped with this feature
WORK PLATFORMS SHALL BE INSPECTED, SERVICED, AND ADJUSTED TO
MANUFACTURER’S REQUIREMENTS BY A QUALIFIED MECHANIC PRIOR TO
EACH SALE, LEASE, OR RENTAL, AND EVERY 3 MONTHS OR 150 HOURS,
WHICHEVER COMES FIRST, AND ANNUALLY.
CAUTION
Y N R N/A
Y N R N/A
Base:
Rails/Extending platform:
Inspect slide tracks for damage
□ □ □ □
Extends freely
□ □ □ □
All frame bolts tight
□ □ □ □
Cables in place/secure
□ □ □ □
Pump secure
□ □ □ □
Locks in stowed position
□ □ □ □
DC motors secure
□ □ □ □
Locks in extended position
□ □ □ □
Batteries fully charged
□ □ □ □
Functions:
For PS Series models:
Tie rods secure
□ □ □ □
All functions (Drive,Elevate,Steer) operational
(see Pre-Start Inspection for details)
□ □ □ □
Wheels:
Pothole guards deploy when platform elevated
□ □ □ □
Snap rings secure
□ □ □ □
Emergency stop breaks circuits
□ □ □ □
Bolts/nuts tight
□ □ □ □
Slow speed limit switch set properly
□ □ □ □
All shields/guards in place
□ □ □ □
Pothole interlock functions correctly
□ □ □ □
Scissors:
Brakes:
Operational
□ □ □ □
No broken welds
□ □ □ □
Emergency Down operational
□ □ □ □
No bent beam members
□ □ □ □
Wiring:
All rollers turn freely
□ □ □ □
Switches secure
□ □ □ □
Ret. rings secure on pivots
□ □ □ □
Contactor(s) secure
□ □ □ □
Maintenance locks:
Stored in designated location
□ □ □ □
Tight on terminals (No loose wiring)
□ □ □ □
Platform:
Oil:
Level 1” from top (when platform stowed)
□ □ □ □
No bent rails
□ □ □ □
Check all hose for leaks
□ □ □ □
No broken welds
□ □ □ □
Check all fi ttings for leaks
□ □ □ □
All rails in place/secure
□ □ □ □
Battery charger secure/operational
□ □ □ □
110V outlet safe/working (if applicable)
□ □ □ □
Tilt sensor
□ □ □ □
Entrance gate closes freely
□ □ □ □
Warning horn (if applicable)
□ □ □ □
Decals:
Hour meter operational
□ □ □ □
Legibile
□ □ □ □
Battery indication operational
□ □ □ □
Correct capacity noted
□ □ □ □
Operator’s Manual is on the unit
□ □ □ □
Proper placement & quantity
□ □ □ □
If equipped with load sensing:
Overload light & alarm sounds when overloaded
□ □ □ □
Date:
Inspected by:
SECTION 3 | MAINTENANCE CHECKLISTS
SECTION 3 | MAINTENANCE CHECKLISTS
3.1 | PRE-START INSPECTION CHECKLIST
3.2 | PRE-DELIVERY/ANNUAL/FREQUENT INSPECTION CHECKLIST
Y-Yes/Acceptable N-No/Unacceptable R-Repaired N/A - Not equipped with this feature
Y
N
R
N/A
VISUAL INSPECTIONS
There are no loose or missing parts.
□ □ □
□
Check that warning and instructional labels are legible and secure. Ensure that load capacity is clearly marked.
□ □ □
□
Check the platform rails and safety gate for damage.
□ □ □
□
Platform and base controls are not missing, damaged, or disconnected.
□ □ □
□
Electrical cables and wires are not torn, frayed, or disconnected.
□ □ □
□
Hydraulic hoses are not torn or loose, and there are no leaks. Hoses and the cables have no worn areas or
chafi ng.
□ □ □
□
Check the tires for damage. Check that wheel axle retaining rings and any set screw(s) in rear wheel are tight.
□ □ □
□
Check that all snap rings are secure in grooves on pivot pins.
□ □ □
□
FUNCTIONAL TESTS
Gate closes automatically and latches.
□ □ □
□
Platform Controls: Check all switches and push buttons for proper operation.
Emergency Stop (Stops all movement)
□ □ □
□
Enable Switch (Does not elevate unless enable is pressed)
□ □ □
□
Joystick (Return to neutral, drives forward & reverse,)
Enable Trigger (Must be activated for joystick-operated movement)
Thumb rocker steers right & left
□
□
□
□
□
□
□
□
□
□
□
□
If so equipped,
horn sounds when button is pressed.
□ □ □
□
Base Controls: Check all switches and push buttons for proper operation.
Emergency Stop (Stops all movement)
□ □ □
□
Key Switch (Selects Platform Control, Ground Control, or Off )
□ □ □
□
Up/Down Rocker Switch (Elevates, Lowers)
□ □ □
□
Descent Alarm (Not damaged, sounds for descent; may also sound for drive & elevate, if so equipped)
□ □ □
□
Tilt Alarm (Not damaged, sounds when tilted and machine elevated above designated height)
□ □ □
□
Master Power Switch disconnects battery
□ □ □
□
Wheels: Front and rear wheels rotate freely.
□ □ □
□
Drives in slow speed when elevated.
□ □ □
□
Brakes: Machine stops when joystick released.
□ □ □
□
Pothole guards deploy and lock when platform is elevated.
□ □ □
□
Lift does not elevate when pothole guards are blocked.
□ □ □
□
Date:
Inspected by:
Model:
Serial Number:
• Keep inspection records up-to-date.
• Record and report all discrepancies to your supervisor.
• A dirty machine cannot be properly inspected.
THIS CHECKLIST MUST BE USED AT THE BEGINNING OF EACH SHIFT OR
AFTER EVERY SIX TO EIGHT HOURS OF USE. FAILURE TO DO SO COULD
AFFECT THE SAFETY OF THE OPERATOR.
CAUTION
Pre-start Inspection (Pro Series Models)
MAINTENANCE & TROUBLESHOOTING
PS-1030 | PS-1430
SUPO-742
REV A
MAINTENANCE & TROUBLESHOOTING
PS-1030 | PS-1430
SUPO-742
REV A
14
15