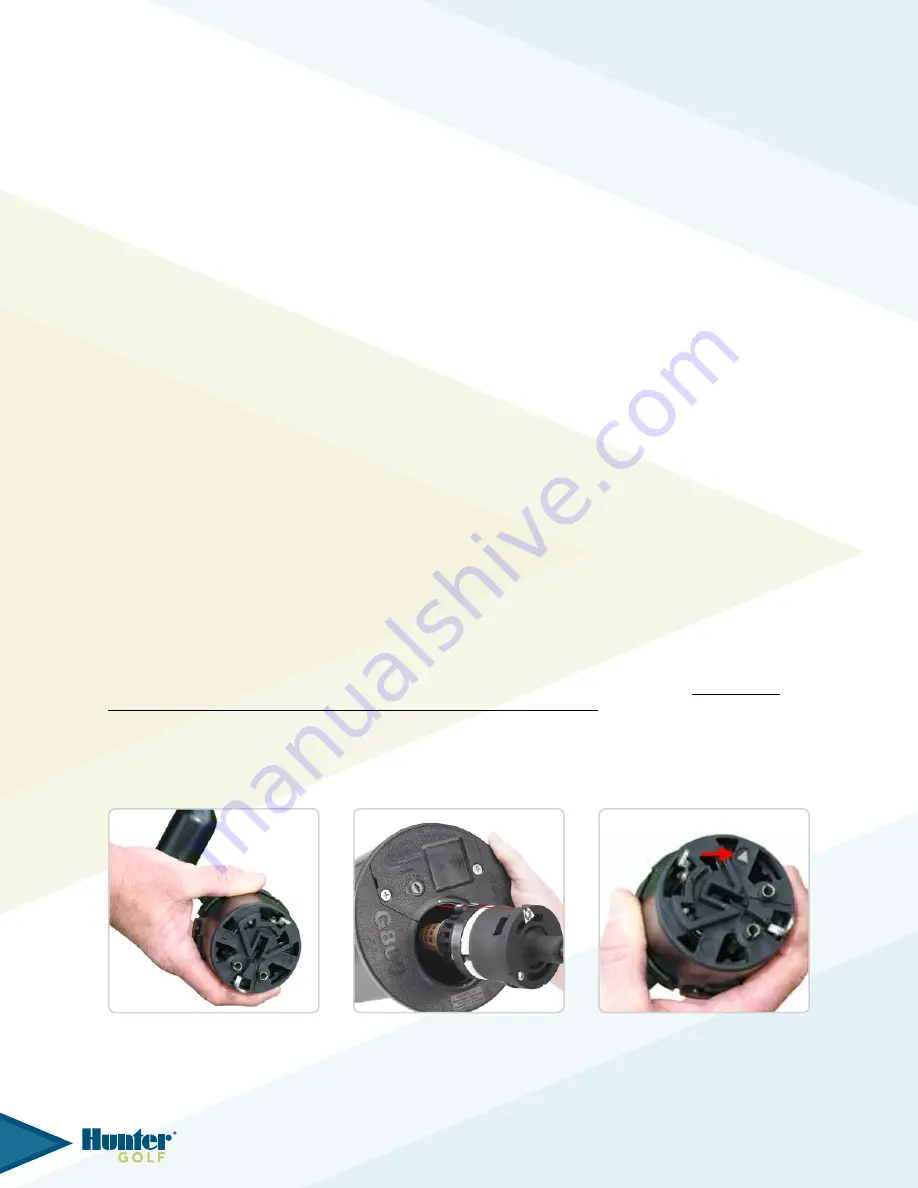
inleT VAlVe inSTAllATion – SAfeTy WARningS
Caution! If inlet valve (also commonly known as a foot valve) is not properly installed and held securely in
place with a properly installed snap-ring, the inlet valve can be expelled from the rotor when the piping is
re-pressurized. Serious bodily injury can occur. Keep head and body parts away from the rotor when piping is
being re-pressurized.
Attention! Read and understand the inlet valve installation instructions outline below. If you are unsure or not
clear on any portion of the installation procedure, contact your local Hunter Golf Distributor Representative or
Hunter Technical Services can be contacted at 800-733-2823 and choose option #3.
inleT VAlVe inSTAllATion – g800 SeRieS
remove excess water from the rotor’s body cavity. Inspect the upper and lower snap ring grooves making sure there
are no damaged or missing sections of plastic adjacent to (next to) the snap ring grooves. remove all plastic shavings
or burrs of plastic that are found within the body cavity.
If needed, a small amount of Dow Corning™ #111 Valve Lubricant or pure petroleum jelly like Vaseline™ can be
used around the o-ring on the inlet valve. In most instances, residual water within the rotor’s body cavity is sufficient
lubrication for inlet valve installation.
Caution!
use of other non-specified lubricants can attack and deteriorate the plastic used in golf rotors. stress cracks
or leaking caused by the use of improper lubricants are not covered under warranty.
Inlet valve installation option 1
– g800 series inlet valves are installed in the body using the g800 Valve tool. prior
to using the tool, familiarize yourself with the individual features of the g800 Valve tool. First, notice there are two
metal hooks at the bottom of the tool (fig 100). these hooks are used to grab/hook the inlet valve during installation.
the black plastic part of the g800 Valve tool includes physical features that hold or nest the inlet valve and the white
lower snap ring to the tool during installation.
In order to engage the inlet valve and white lower snap ring with the g800 Valve tool properly, you must be familiar
with the pointing and alignment features on the tool’s black plastic part. First, look at the three retaining screws on
top of the tool. next, find the screw that has a pointer arrow engraved around the head of the screw (fig 101). this
pointer is used to indicate the direction and alignment that the tool must have as it is inserted into the rotor’s body.
a second pointer arrow is located directly below on the underside of the g800 Valve tool (fig 102).
the underside of the black plastic part on the g800 Valve tool includes a feature that will hold the white lower snap
ring in position during installation. the white lower snap ring must be oriented correctly in the tool and the raised
areas at each end of the snap ring must be facing the black plastic part on the tool. the white lower snap ring must be
loaded to the g800 Valve tool correctly. If the snap ring is not loaded correctly, the valve cannot be loaded to the tool.
FIg 100
FIg 101
FIg 102
Fig 99
Fig 100
Fig 101
Fig 99
Fig 100
Fig 101
Fig 99
Fig 100
Fig 101
33
Summary of Contents for G835
Page 2: ......
Page 21: ...Fig 47 Fig 49 Fig 50 Fig 48 Fig 48 Fig 47 Fig 48 Fig 47 18...
Page 57: ...54...